Ceramic Sand Casting An Innovative Approach to Metal Fabrication
Ceramic sand casting is a revolutionary method in the field of metal fabrication that has gained significant attention in recent years. This innovative technique combines traditional sand casting methods with the unique properties of ceramic materials, resulting in enhanced dimensional accuracy, improved surface finish, and superior mechanical properties. It is particularly beneficial for industries requiring complex geometries and high-performance components.
At its core, ceramic sand casting utilizes a special type of sand that is coated with a ceramic material. This ceramic coating allows the sand grains to retain heat better, providing a more stable mold for the molten metal. The process begins with the preparation of a pattern, typically made from metal or plastic, which is then embedded in the ceramic sand mixture. Once the pattern is removed, it leaves a highly detailed mold that captures the intricacies of the original design.
One of the standout advantages of ceramic sand casting is its ability to produce intricate shapes that would be challenging to achieve with traditional metal casting methods
. The precise molding capability enables manufacturers to create complex components with tighter tolerances. This advantage is particularly useful in industries such as aerospace, automotive, and energy, where components must meet stringent requirements for performance and durability.ceramic sand casting
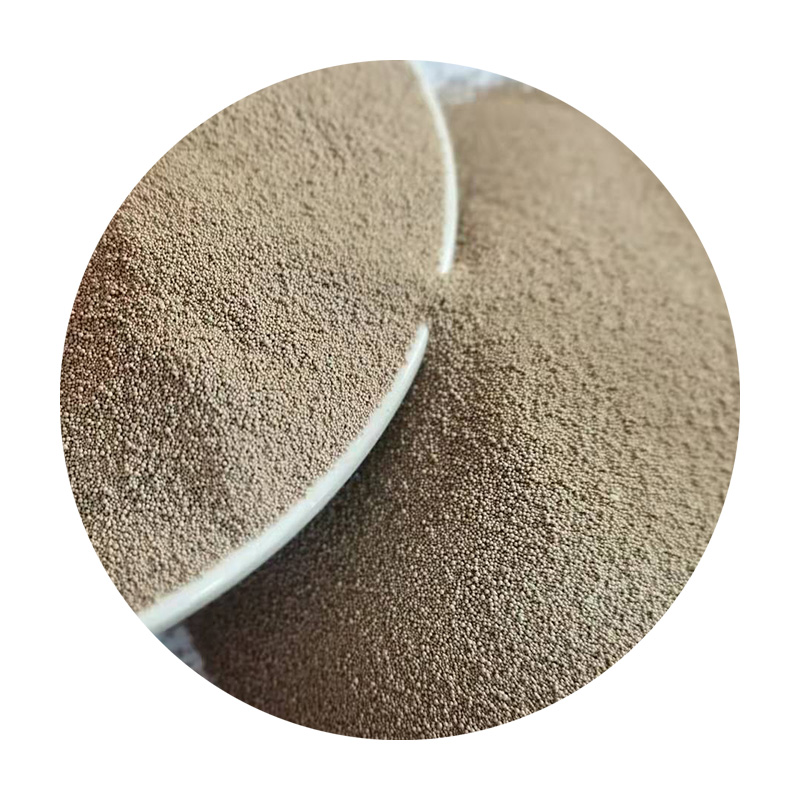
Moreover, the ceramic material used in the sand casting process contributes to improved thermal stability. This characteristic allows the mold to withstand higher temperatures without deforming, making it suitable for casting high-temperature alloys. As a result, the final products demonstrate enhanced mechanical properties such as strength and resistance to wear, making them ideal for demanding applications.
Another highlight of ceramic sand casting is its environmental benefits. The process typically generates less waste compared to traditional methods, and the ceramic materials used can be recyclable. This aspect aligns with the growing trend towards sustainability in manufacturing, appealing to companies looking to reduce their environmental footprint while maintaining high standards of quality.
In terms of cost-effectiveness, while the initial setup for ceramic sand casting may be higher than traditional sand casting, the long-term benefits often outweigh the initial investment. The durability of the molds leads to longer production runs and decreased downtime for mold repairs. Additionally, the ability to produce high-quality components allows manufacturers to reduce costs associated with rework and scrap.
In summary, ceramic sand casting stands out as a modern solution for industries that demand high precision and performance. With its ability to create intricate designs, enhanced thermal properties, and environmental advantages, it represents a significant advancement in metal fabrication. As technology continues to evolve, we can expect ceramic sand casting to play an even more pivotal role in the manufacturing landscape, driving innovation and efficiency in various sectors.
Post time:Zář . 04, 2024 02:10
Next:foundry sand composition