Lost Foam Casting An Innovative Approach to Precision Metal Casting
Lost foam casting (LFC) is a modern metal casting process that has gained popularity due to its ability to produce complex shapes with great accuracy and excellent surface finish. This technique, which was developed in the 1970s, combines elements of traditional investment casting with the speed and cost-effectiveness of modern manufacturing methods. The following explores the process of lost foam casting, its advantages, applications, and some considerations for manufacturers.
The Process of Lost Foam Casting
At its core, lost foam casting involves creating a foam pattern that is coated with a refractory material. Here’s how it typically works
1. Foam Pattern Creation The process begins with the fabrication of a foam pattern, commonly made from polystyrene. This foam can be easily shaped into intricate designs, allowing for high complexity in the final metal part. 2. Coating the Foam The foam pattern is then coated with a fine layer of sand mixed with a binder. This coating forms a shell around the foam, providing the necessary support during the casting process. 3. Pattern Installation Once the foam is coated and hardened, it is placed in a mold. The mold can be made of metal or sand, and it is designed to capture the shape of the foam pattern.
4. Pouring the Metal After the setup is complete, molten metal is poured into the mold. As the metal fills the cavity, it evaporates the foam pattern, leaving behind a hollow impression in the exact shape of the original design.
5. Cooling and Finishing Once the metal has cooled and solidified, the mold is broken away, revealing the final product. The residual sand and any surface imperfections can be removed through various finishing techniques.
Advantages of Lost Foam Casting
Lost foam casting offers several notable advantages over traditional casting methods
- Complex Geometries One of the most significant benefits of LFC is its ability to produce parts with highly intricate shapes and internal features that would be difficult or impossible to achieve through other methods. - Reduced Tooling Costs Since the foam patterns can be created quickly and inexpensively, tooling costs are significantly lower compared to traditional casting techniques, making LFC an attractive option for low- to medium-volume production.
lost-foam casting
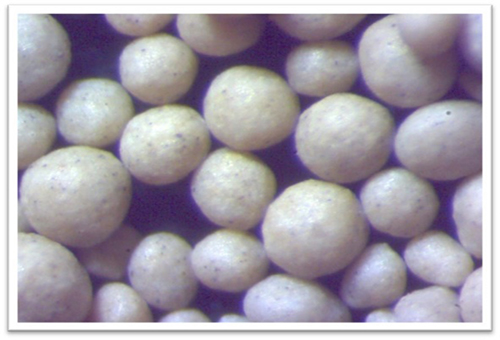
- Minimal Waste The process produces minimal waste compared to traditional methods where extra material must often be machined away. The foam pattern is completely converted into gas during metal pouring, which adds to the eco-friendliness of the process.
- Enhanced Surface Finish The surface finish achieved through lost foam casting can eliminate or reduce the need for extensive machining, further reducing production time and costs.
Applications of Lost Foam Casting
The versatility of lost foam casting allows it to be used in various industries. Some common applications include
- Automotive Parts LFC is popular for manufacturing engine components, brackets, and other intricate parts that require precision and reliability. - Aerospace Components The aerospace industry benefits from the lightweight yet durable components produced through this method, essential for reducing overall aircraft weight.
- General Engineering The process can also be applied to produce complex housings and fittings for various machinery and equipment.
Considerations for Manufacturers
While lost foam casting presents numerous advantages, it is essential for manufacturers to consider certain factors such as material selection, mold design, and cycle time. Additionally, the availability of skilled technicians and equipment can influence the successful implementation of the process.
In conclusion, lost foam casting is a revolutionary technique that combines precision with cost-effectiveness, making it an ideal choice for manufacturers seeking to create complex components. As technology continues to advance, the potential applications and benefits of LFC are only expected to grow, solidifying its place in the future of metal casting.
Post time:Nov . 07, 2024 09:55
Next:Understanding the Uses and Benefits of Sand Casting in Manufacturing Processes