3D Printer Sand Casting Revolutionizing Manufacturing Processes
The advent of 3D printing technology has ushered in a new era in manufacturing, offering innovative solutions to conventional processes. One such application is the integration of 3D printing with sand casting, a traditional metal casting method. This combination is transforming the way industries approach the production of complex metal parts, providing enhanced efficiency, reduced costs, and greater design flexibility.
Understanding Sand Casting
Sand casting is a widely used method for producing metal parts by pouring molten metal into a sand mold. The sand is mixed with a binding agent to create a mold, which is then shaped according to the desired component. Once the metal cools and solidifies, the sand is removed, leaving behind the cast part. This technique has been relied upon for its ability to create intricate shapes and large components, but it also has its limitations, particularly in terms of lead times and design complexity.
The Role of 3D Printing in Sand Casting
3D printing, also known as additive manufacturing, creates objects layer by layer based on digital models. By combining 3D printing with sand casting, manufacturers can leverage the strengths of both technologies. 3D printers can create complex sand molds that would be challenging or impossible to produce using traditional methods.
Enhanced Design Flexibility
One of the most significant benefits of utilizing 3D printing in sand casting is the increased design flexibility. With the ability to easily create intricate geometries, manufacturers can design parts that are lighter yet stronger, optimizing performance and reducing materials waste. This innovation also allows for the incorporation of organic shapes and customized features, which can lead to enhancements in product functionality.
Reducing Lead Times and Costs
Traditionally, creating molds for sand casting requires significant time and resources. However, 3D printing dramatically reduces the lead time associated with mold production. Rapid prototyping can be achieved, allowing for quick iterations and modifications before final production. This accelerated process not only saves money but also brings products to market faster, giving companies a competitive advantage.
3d printer sand casting
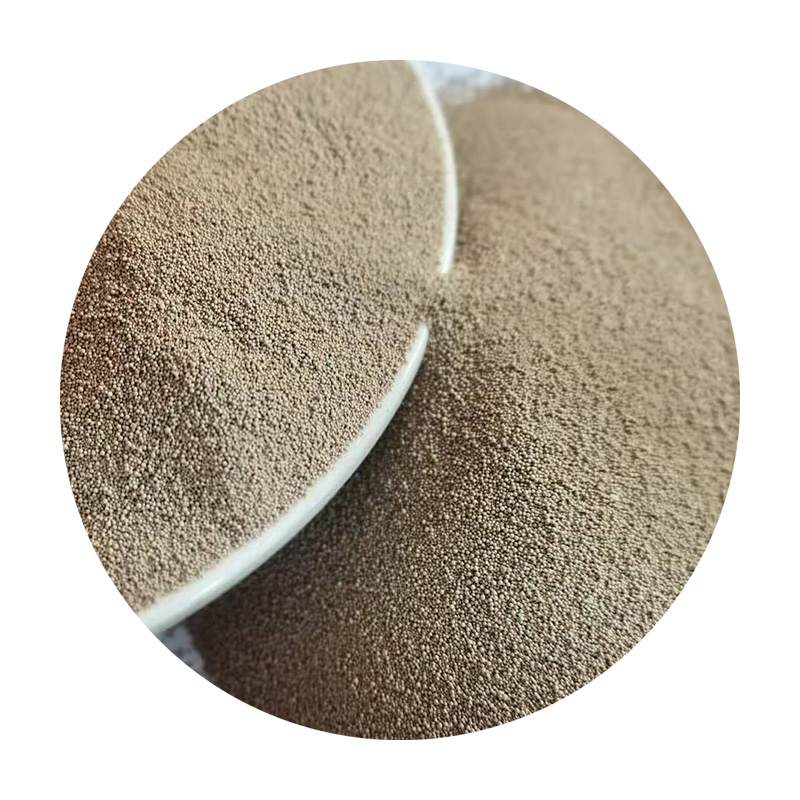
Environmental Considerations
As industries increasingly seek sustainable practices, the integration of 3D printing into sand casting contributes to environmental benefits. Traditional sand casting often generates significant waste, but 3D printing allows for more efficient use of materials. Moreover, technologies such as binder jetting can use recycled sand, reducing the need for new resources. By minimizing waste and energy consumption, manufacturers are stepping closer to more sustainable production methods.
Case Studies and Industry Applications
Several industries have already started to recognize the benefits of 3D printer sand casting. For instance, the aerospace sector is utilizing this technology to produce lightweight components with intricate designs that are impossible to achieve through traditional means. Similarly, the automotive industry is implementing 3D printed sand molds to manufacture engine parts and prototypes, allowing for rapid testing and design adjustments.
Furthermore, companies like General Electric and BMW have been at the forefront of integrating 3D printing with sand casting. They have successfully produced complex geometries that enhance performance while efficiently managing production costs and timelines.
Challenges and Future Directions
Despite its advantages, 3D printing in sand casting is not without challenges. The technology is still developing, and issues related to mold durability and finishing processes need to be addressed. Additionally, the initial investment in 3D printing technologies can be high, which may deter some manufacturers from adopting this approach.
However, as advancements continue and costs decrease, it is anticipated that more industries will embrace 3D printer sand casting. The future looks promising, with ongoing research and innovation paving the way for even more efficient and sustainable manufacturing practices.
Conclusion
The integration of 3D printing into sand casting is redefining the landscape of manufacturing. By combining design flexibility and reduced lead times with environmental benefits, this innovative approach is poised to revolutionize industries. As technology advances and becomes more accessible, we can expect to see even more transformative applications emerge, enabling manufacturers to meet the demands of an ever-evolving market. The future of 3D printer sand casting indeed holds tremendous potential, marking a significant step forward in the world of manufacturing.
Post time:Dec . 05, 2024 15:15
Next:sand casting suppliers