What is Sand Casting in Engineering?
Sand casting, also known as sand mold casting, is one of the oldest and most widely used manufacturing processes in the engineering and foundry industries. This method involves creating a mold from sand to produce metal castings, where molten metal is poured into the mold cavity created by a pattern. The sand provides several critical benefits that make it an ideal material for mold-making.
Process Overview
The sand casting process begins with the preparation of a pattern, which is a replica of the desired final product. The pattern is then used to create a mold by packing sand around it. This sand is typically mixed with a binder such as clay to help it hold its shape. Once the sand is compacted, the pattern is removed, leaving a cavity that corresponds to the design of the object to be cast.
After the mold is prepared, it is assembled, and molten metal is poured into the cavity. The metal can be any type of metal suitable for casting, including aluminum, iron, bronze, and steel. The casting is allowed to cool and solidify, after which the mold is broken away to reveal the finished component.
Advantages of Sand Casting
1. Cost-Effectiveness Sand casting is relatively inexpensive compared to other casting methods. The materials required for the mold are readily available and inexpensive, making it a preferred choice for low-volume production.
2. Versatility This method can be used with a wide range of metals, from ferrous to non-ferrous alloys. It is suitable for both small and large parts, and there are few limitations on the size and complexity of the components that can be produced.
what is sand casting in engineering
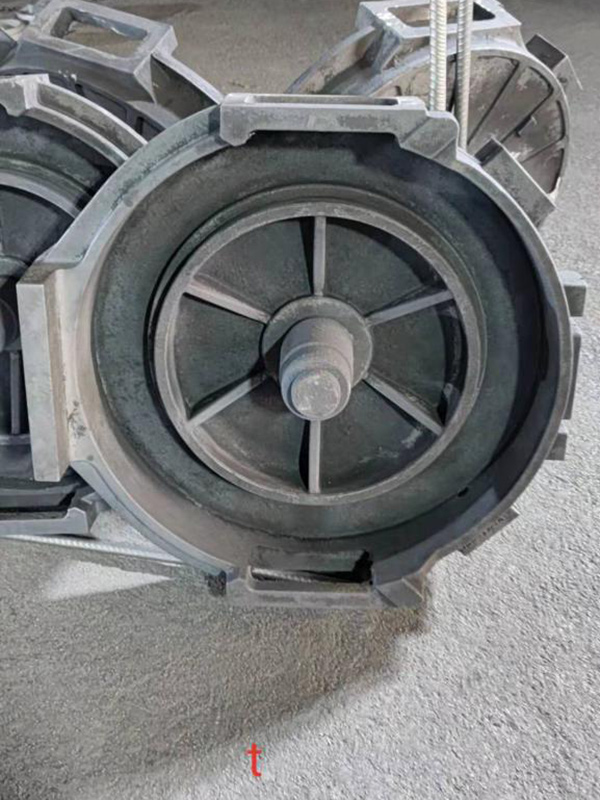
4. Ability to Produce Complex Shapes Sand casting allows for the creation of intricate designs that might be difficult or impossible to achieve with other methods.
5. Scalability Sand casting can be efficiently scaled for both small and large production runs. It is ideal for prototypes as well as for larger quantities needed in manufacturing.
Disadvantages of Sand Casting
Despite its many advantages, sand casting also has several drawbacks. The final product may require significant finishing work to meet specific tolerances and surface qualities. The process can also be labor-intensive and time-consuming, particularly in the pattern-making phase. Additionally, sand molds do not have the same strength and durability as metal molds, requiring careful handling and often leading to shorter production runs.
Applications of Sand Casting
Sand casting is prevalent in various industries, including automotive, aerospace, and construction. It is used to make a diverse range of components such as engine blocks, pump housings, and brackets. In the automotive sector, for example, sand casting is utilized to create complex shapes in engine parts, allowing for enhanced engine efficiency and performance.
In the aerospace sector, the lightweight characteristics of sand-cast aluminum alloys are often exploited. The ability to create parts that meet precise weight and strength requirements is critical in this industry. Applications also extend to art and sculpture, where artists and artisans use sand casting to create detailed and finely crafted pieces.
Conclusion
Sand casting remains a fundamental process in engineering and manufacturing due to its versatility, cost-effectiveness, and capability to produce complex shapes. While it has its drawbacks, improvements in technology and materials continue to enhance its effectiveness, making it a valuable method for producing various components across multiple sectors. As industries evolve and new metal alloys are developed, sand casting will likely continue to be a crucial process in the manufacturing landscape. With its long history and ongoing relevance, understanding sand casting is essential for anyone involved in engineering and production engineering fields.
Post time:Dis . 19, 2024 00:20
Next:foundry sand pdf