Understanding Sand Cast Iron A Comprehensive Overview
Sand cast iron is one of the most popular materials used in the manufacturing industry, prized for its versatility, durability, and cost-effectiveness. This article aims to provide an in-depth understanding of sand cast iron, exploring its composition, manufacturing process, properties, and applications.
Composition of Sand Cast Iron
Sand cast iron is primarily composed of iron, with carbon as its major alloying element. The carbon content in cast iron typically ranges from 2% to 4%, which significantly affects the material’s properties. In addition to carbon, sand cast iron may contain other elements such as silicon, manganese, phosphorus, and sulfur. The specific composition can vary based on the intended application, but the fundamental structure remains the same. The presence of silicon, for example, improves fluidity during casting and enhances casting strength.
Manufacturing Process
The process of manufacturing sand cast iron involves several key steps
1. Pattern Making The first step is to create a pattern, which serves as a template for the final product. Patterns are typically made from wood or metal and are designed to accommodate the shrinkage that occurs during cooling.
2. Mold Preparation The pattern is placed in a flask, and a mixture of sand and a binder is packed around it to create a mold. This sand mix is often referred to as ‘green sand’, a mixture of sand, clay, and moisture. Once the mold is prepared, it is removed from the pattern, and the pattern is extracted, leaving a cavity in the shape of the desired object.
3. Melting and Pouring The raw iron is then melted in a furnace. Once it reaches the appropriate temperature, the molten iron is carefully poured into the mold cavity.
4. Cooling and Solidification After pouring, the molten iron cools and solidifies, taking the shape of the mold. The cooling rate can influence the grain structure and overall properties of the finished product.
5. Finishing Once the casting has cooled, it is removed from the mold, and any excess material is trimmed away. Further finishing processes, such as machining or surface treatments, may be applied to achieve precise dimensions and surface quality.
Properties of Sand Cast Iron
Sand cast iron exhibits several key properties that make it a desirable material for various applications
sand cast iron
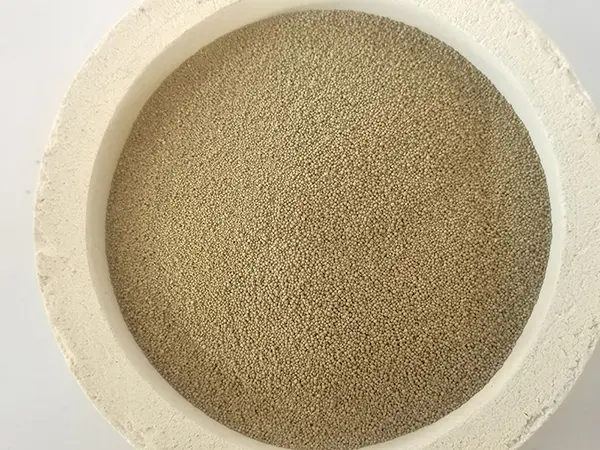
- High Wear Resistance The presence of carbon and the unique microstructure of cast iron provide excellent resistance to wear and abrasion, making it ideal for applications involving heavy loads and friction.
- Good Machinability Despite its strength, sand cast iron is relatively easy to machine
. This property allows for precise shaping and finishing of components after casting.- Excellent Damping Capacity Cast iron has superior vibration damping characteristics, making it an excellent choice for applications in machinery and equipment where stability and reduced noise levels are essential.
- Corrosion Resistance While not as corrosion-resistant as other alloys, cast iron can be treated or coated to enhance its resistance to rust and degradation.
Applications of Sand Cast Iron
Sand cast iron is widely used across various industries due to its beneficial properties. Common applications include
- Engine Blocks Many automotive and machinery components, particularly engine blocks, utilize sand cast iron due to its durability and ability to withstand high temperatures.
- Pipes and Fittings Cast iron pipes and fittings are commonly used in plumbing and drainage systems due to their strength and resistance to wear.
- Machine Parts Numerous machine components, including gears, housings, and frame structures, are made from sand cast iron, benefiting from its machinability and strength.
- Artistic Castings Beyond industrial applications, sand cast iron is also used for artistic purposes, including sculptures and decorative elements, thanks to its ability to capture fine details.
Conclusion
In conclusion, sand cast iron remains a fundamental material in modern manufacturing, offering a unique blend of properties that match a wide array of applications. From engineering and construction to artistic endeavors, its versatility and cost-effectiveness make it an enduring choice for many industries. Understanding its composition, manufacturing process, and properties is crucial for anyone involved in design and production, ensuring the appropriate use of this remarkable material.
Post time:Dis . 11, 2024 06:49
Next:Exploring the Benefits and Uses of Cerabead Sand in Various Industries