Sand Casting An Overview of Metal Casting Techniques
Sand casting is one of the oldest and most widely used methods for manufacturing metal parts. It is a versatile casting process that can accommodate a wide range of metals, including aluminum, bronze, iron, and many others. The method is known for its flexible design options, affordability, and ability to create complex shapes with high-dimensional accuracy, making it a favorite among engineers and manufacturers.
The Sand Casting Process
The sand casting process begins with the creation of a pattern, which is essentially a replica of the object to be cast. This pattern is usually made from wood, plastic, or metal and is used to form a mold. The mold itself is made by packing a mixture of sand and a binding agent around the pattern. This mixture is typically raw sand mixed with clay and water, which provides the necessary cohesiveness to hold the shape.
Once the pattern is removed, the resulting cavity is then ready for pouring molten metal. The metal is heated to its melting point and then carefully poured into the mold. After the metal cools and solidifies, the sand mold is broken away to reveal the cast part. This part may then be further processed through machining or finishing techniques to achieve the desired surface quality and dimensions.
Advantages of Sand Casting
One of the primary benefits of sand casting is its flexibility. It can produce large and complex parts that might be impossible or costly to manufacture using other methods. The sand mold can be easily modified to adapt to different designs, which makes it an ideal choice for prototype development or low-volume production runs.
Another advantage of sand casting is its cost-effectiveness. The materials used—sand and a binding agent—are relatively inexpensive and widely available. Moreover, the casting process does not require elaborate setups, which reduces overall production costs. This makes sand casting particularly appealing for small to medium-sized businesses looking to create custom parts without a significant financial investment.
sand casting metal
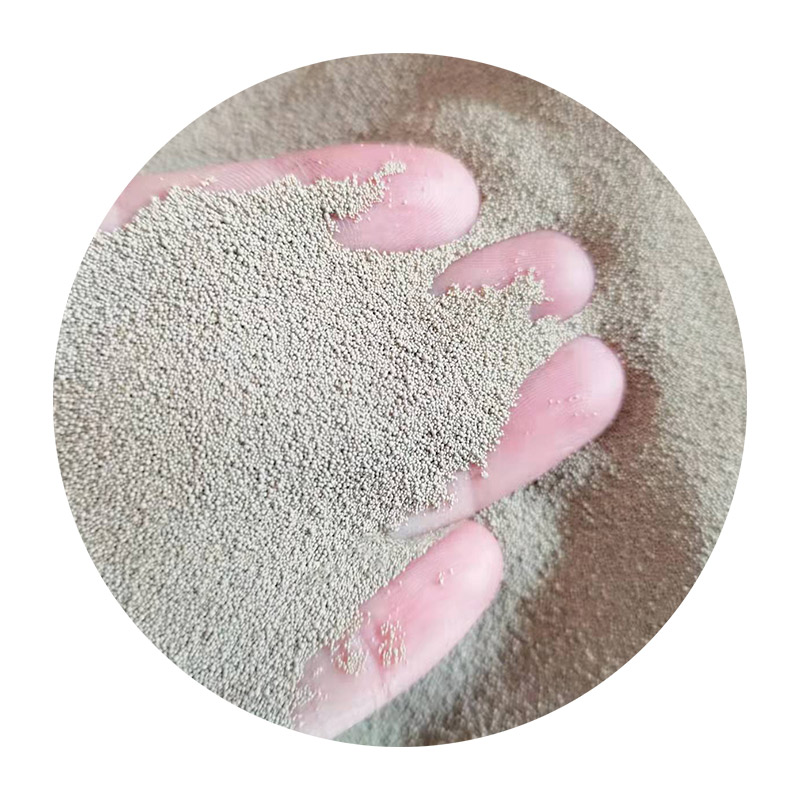
Additionally, sand casting accommodates a wide variety of metal types, which further increases its versatility. Whether it's ferrous metals like cast iron or non-ferrous metals like aluminum and bronze, sand casting can effectively handle them all. This adaptability opens the door for numerous applications, from automotive components to industrial equipment.
Disadvantages of Sand Casting
Despite its many advantages, sand casting does come with some drawbacks. One significant limitation is the surface finish. The finish obtained from sand casting is generally rougher compared to other methods like die casting or investment casting. This means that additional processing, such as grinding or polishing, is often required to achieve a smoother surface.
Moreover, sand casting typically has lower dimensional accuracy compared to more advanced casting techniques. While it can produce intricate designs, the tolerances may not be as tight as those achievable through other methods. This is particularly important in high-precision applications where exact dimensions are crucial.
Applications of Sand Casting
Sand casting is used in a myriad of industries, including aerospace, automotive, and machinery manufacturing. Components such as engine blocks, brackets, and frames can all be effectively produced using this method. In addition, the process is widely utilized in creating artistic sculptures and decorative items, offering a broad canvas for creative expression.
Conclusion
In summary, sand casting remains a cornerstone in the field of metal fabrication due to its flexibility, cost-effectiveness, and ability to produce complex shapes. While it has its limitations regarding surface finish and dimensional accuracy, the advantages it offers make it an enduring choice for manufacturers across various industries. As technology advances, innovations in sand casting techniques continue to improve the quality and efficiency of this ancient method, ensuring its relevance in modern manufacturing. Whether for prototyping or large-scale production, sand casting will undoubtedly remain an essential tool in the metallurgical toolbox.
Post time:Dis . 05, 2024 02:28
Next:molding sand for metal casting