Understanding the Resin Sand Casting Process
The resin sand casting process is a modern manufacturing technique that combines the traditional methods of sand casting with innovative materials to produce high-quality metal components. This method has gained popularity in various industries due to its ability to achieve precise dimensions, complex geometries, and superior surface finishes. In this article, we will explore the resin sand casting process, its advantages, applications, and the critical factors that contribute to its success.
What is Resin Sand Casting?
Resin sand casting involves creating a mold from a mixture of sand and a resin binding agent. Unlike traditional sand casting, which uses water-based binders, resin sand molds are created using thermosetting resins that harden when heated. This process enables the production of molds that are more durable and better suited for intricate designs and high-temperature applications.
The first step in the resin sand casting process is preparing the sand mixture. The sand used is typically silica sand, which is combined with a resin binder and a hardening catalyst. The proportion of these materials is critical and must be carefully controlled to ensure the right properties of the sand mixture. Once the mixture is prepared, it is compacted around a pattern, which can be made of metal or other materials. This pattern defines the geometry of the final cast component.
After the mold is formed and the resin has cured, the pattern is removed, leaving a cavity that represents the shape of the desired metal part. This cavity is then ready to be filled with molten metal, which could include various alloys such as aluminum, iron, or copper, depending on the specific requirements of the application.
Advantages of Resin Sand Casting
One of the primary advantages of the resin sand casting process is its ability to produce high-precision components. The use of resin-based binders allows for tighter tolerances compared to traditional sand casting. As a result, parts manufactured through this process often require minimal post-casting machining, which saves time and reduces production costs.
Another significant advantage is the improved surface finish that resin sand casting can achieve. The smooth surface of the resin-cured molds results in castings that have fewer defects and surface irregularities. This feature is particularly important for industries that require aesthetic considerations, such as automotive and consumer products.
resin sand casting process
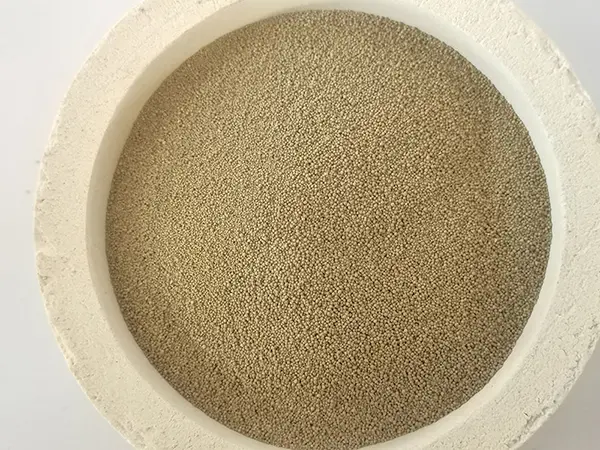
Additionally, the resin sand casting process allows for a wide range of complex geometries to be produced. Manufacturers can create intricate designs that would be difficult or impossible to achieve using other casting methods. This flexibility makes resin sand casting a preferred choice for prototype development and custom manufacturing.
Applications of Resin Sand Casting
The versatility of resin sand casting makes it applicable in various sectors, including automotive, aerospace, marine, and machinery manufacturing. In the automotive industry, for instance, it is used to produce engine blocks, transmission housings, and other components requiring high strength and precision. The aerospace industry similarly benefits from resin sand casting for parts like brackets, housings, and structural components that demand lightweight and durable solutions.
Moreover, the marine sector utilizes this casting method for producing propellers, pump housings, and other components exposed to harsh environmental conditions. The machinery manufacturing sector leverages resin sand casting to create intricate parts for equipment, enabling enhanced functionality and durability.
Key Considerations in the Resin Sand Casting Process
Though resin sand casting offers numerous benefits, there are essential factors to consider for successful implementation. The quality of the sand-resin mixture is critical, as improper ratios or inadequate mixing can lead to defects in the mold and, consequently, in the final casting. Additionally, the curing time and temperature must be carefully controlled to ensure the resin fully hardens for optimal performance.
Furthermore, the choice of patterns significantly influences the success of the resin sand casting process. Patterns should be designed with the material shrinkage in mind, ensuring the final cast part meets the required specifications.
Conclusion
The resin sand casting process is a robust and versatile manufacturing technique that brings together the advantages of sand casting and modern materials technology. Its ability to produce high-precision, complex components with excellent surface finishes makes it a valuable method across multiple industries. As manufacturing continues to progress, resin sand casting is likely to play an increasingly vital role in producing high-quality metal parts for an ever-growing range of applications.
Post time:Dis . 04, 2024 23:28
Next:how to sand 3d print