Lost-Foam Casting An Innovative Approach to Metal Casting
Lost-foam casting (LFC) is an advanced metalcasting technique that has gained popularity in recent years due to its ability to produce high-quality complex shapes with minimal waste. This method involves creating a foam pattern, which is coated with a fine layer of sand to form a mold. Once the mold is prepared, molten metal is poured into it, evaporating the foam and leaving behind a precise metal replica. This process offers several advantages over traditional casting methods, making it a pivotal technique in many industries today.
The Process of Lost-Foam Casting
The lost-foam casting process begins with the creation of a foam model, typically made from polystyrene. This model is designed to represent the final product’s shape and dimensions. One of the key benefits of using foam is its versatility, allowing for intricate designs that would be difficult or impossible to achieve with conventional patterns.
Once the foam pattern is developed, it is coated with a refractory material, often a mixture of fine sand and a binder, to form the mold shell. This mixture is applied carefully to ensure a uniform coating, which is crucial for the mold's integrity. After coating, the mold is allowed to cure, ensuring that it can withstand the pouring of molten metal.
When the mold is ready, it is placed in a foundry and molten metal is poured directly onto it. As the metal flows into the mold cavity, it exothermically reacts with the foam, causing it to evaporate. This process eliminates the need for mold removal after casting, as the foam effectively vanishes, leaving behind only the desired metal part. This method stands in stark contrast to other casting techniques, where the mold typically must be destroyed to retrieve the finished product.
Advantages of Lost-Foam Casting
lost-foam casting
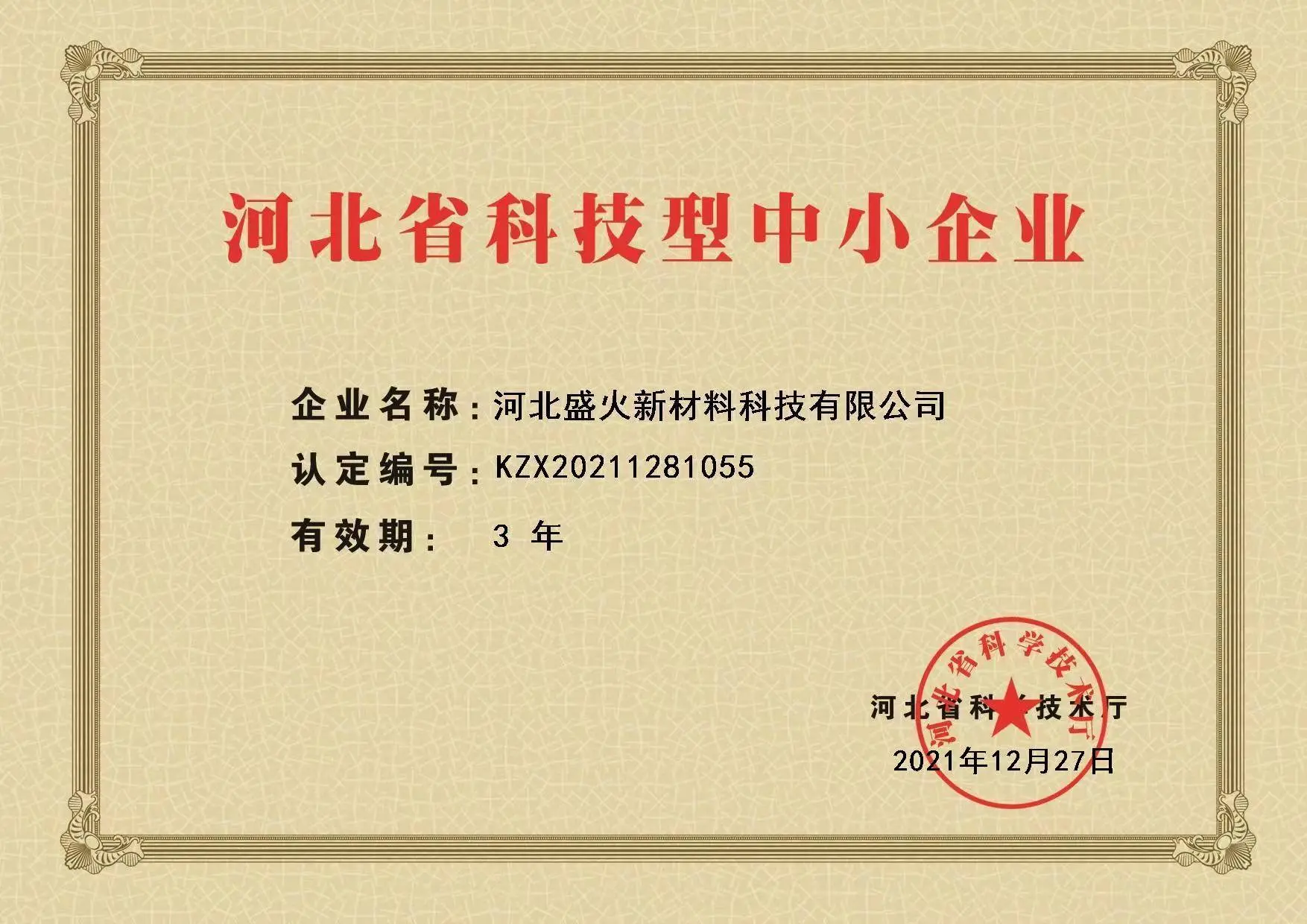
One of the most significant advantages of lost-foam casting is its ability to produce complex geometries at a relatively low cost
. The foam patterns can be created quickly using computerized design software and CNC technology, reducing lead times and labor costs associated with traditional pattern-making techniques. Additionally, because the mold is created using the foam pattern, there is no need for draft angles typically required in metal molds, which allows for sharper corners and finer details.Another advantage is the reduction of waste. In conventional sand casting, excess material may need to be trimmed away, leading to increased waste and higher material costs. In lost-foam casting, however, the process is designed to be near-net-shape, meaning that the final product closely matches the dimensions of the original foam pattern, thereby minimizing excess material and reducing scrap.
Moreover, lost-foam casting allows for the casting of a variety of metals, including aluminum, magnesium, and certain steel alloys. This versatility makes it applicable in diverse sectors, including automotive, aerospace, and even art and sculpture. Components produced through this method can vary from engine blocks and transmission cases to intricate decorative items.
Environmental Impact
In today’s eco-conscious world, the environmental impact of manufacturing processes is under scrutiny. Lost-foam casting is generally considered more environmentally friendly compared to conventional methods. Since the foam pattern evaporates during casting, less energy is consumed in mold production, and the process generates fewer pollutants. Additionally, advancements in materials and technology continue to improve the sustainability of lost-foam casting, aligning it with global efforts to reduce industrial waste.
Conclusion
Lost-foam casting represents an exciting advancement in metal casting technology, offering unique benefits such as reduced costs, intricate design capabilities, and environmental sustainability. As industries continue to seek innovative solutions to meet the demands of modern manufacturing, lost-foam casting will likely play an increasingly significant role. This method is not just a technical improvement; it is a testament to how combining creativity with technological advancements can lead to better, more efficient manufacturing processes. As we move forward, the potential of lost-foam casting in both traditional and emerging sectors will undoubtedly shape the future of metalworking.
Post time:Dis . 04, 2024 19:01
Next:fine casting sand