The Difference Between Sand Casting and Die Casting
Casting is a fundamental manufacturing process that involves pouring liquid material into a mold to create a desired shape. Among various casting methods, sand casting and die casting are two of the most widely used techniques, each with its own advantages, disadvantages, and ideal applications. Understanding the differences between these two processes can help manufacturers select the appropriate method for their specific needs.
1. Process Overview
Sand Casting is an ancient casting method that utilizes sand as the primary mold material. It involves several steps creating a pattern (usually from metal or plastic), embedding it in sand mixed with a bonding agent, and then removing the pattern to form a mold. Molten metal is poured into the sand mold, allowed to cool, and finally removed to reveal the cast part.
Die Casting, on the other hand, employs high-pressure techniques to force molten metal into pre-shaped steel molds (dies). This method is typically used for metals like aluminum, zinc, and magnesium. The die is designed with precision to create parts with complex geometries. Once the metal solidifies, the die is opened, and the casting is ejected.
2. Material Compatibility
One of the significant differences between sand casting and die casting lies in the types of materials they can accommodate. Sand casting is highly versatile and can work with various metals, including cast iron, aluminum, and brass. This flexibility makes it an ideal choice for low-volume production and prototype work.
Conversely, die casting is best suited for non-ferrous metals, particularly aluminum and zinc alloys. The precision and strength of the die-cast parts make them suitable for high-volume production, but their application is restricted to specific materials, limiting its versatility compared to sand casting.
3. Cost and Production Rate
When evaluating cost-effectiveness, sand casting generally has lower initial setup costs, making it affordable for small production runs
. The patterns can be made from various materials and do not require elaborate tooling, allowing quick changes to be made if necessary.Die casting, while having higher initial tooling costs due to the complexity of the dies, is more economical for large-scale production. The high-pressure process allows for the rapid production of identical parts with consistent quality, making it advantageous for mass production environments.
difference between sand casting and die casting
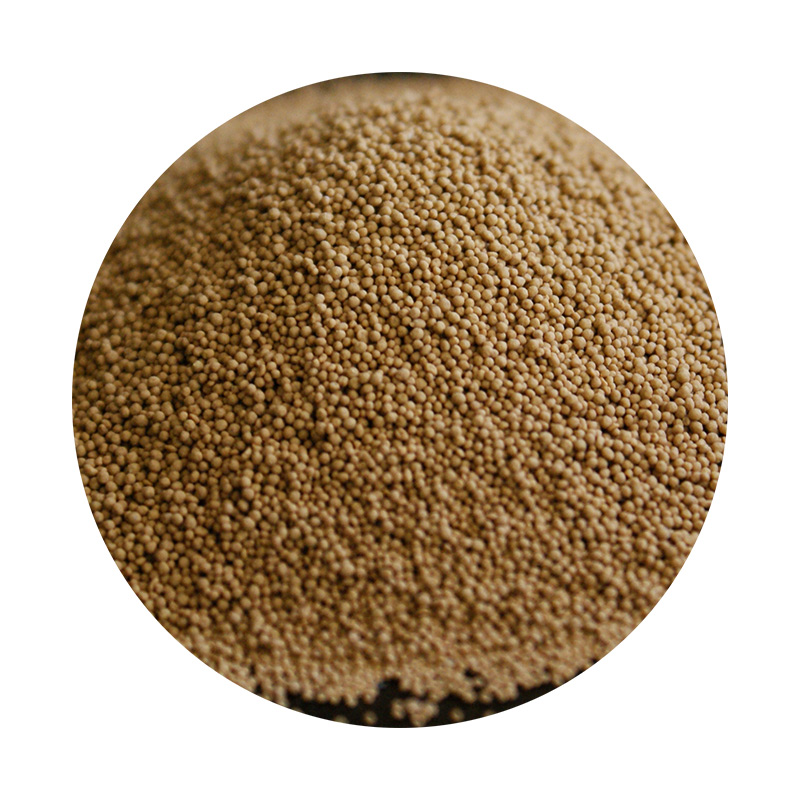
4. Surface Finish and Tolerances
The surface finish and dimensional tolerances of cast parts vary significantly between the two methods. Sand casting often results in a rougher surface finish due to the nature of sand molds, which may require additional processing, such as grinding or machining, to achieve desired specifications. Tolerances in sand casting are generally broader due to the variability in the sand and the molding process.
In contrast, die casting produces parts with a much smoother surface finish and tighter dimensional tolerances. The precision of the dies allows for intricate designs and complex shapes while also minimizing the need for additional machining. This aspect makes die-cast parts highly desirable in industries where appearance and dimensional accuracy are crucial.
5. Applications
Both casting methods serve different industries and applications based on their characteristics. Sand casting is commonly used in foundries for manufacturing large parts such as engine blocks, heavy machinery components, and sculptures. Its adaptability to various sizes and shapes makes it suitable for low-volume production.
Die casting excels in automotive, electronics, and consumer goods sectors, where high-volume production of lightweight, durable parts is essential. Components such as housings, brackets, and intricate parts found in electronic devices often utilize die casting for its efficiency and precision.
6. Environmental Impact
Finally, environmental considerations play a role in the choice between sand casting and die casting. Sand casting is generally seen as more environmentally friendly, as it can use sand repeatedly, and leftover materials can often be recycled. Die casting, on the other hand, can produce waste in the form of scrap metal and often requires the use of lubricants or coatings that may have environmental implications.
Conclusion
In conclusion, the difference between sand casting and die casting is rooted in their processes, material compatibility, cost, surface finish, applications, and environmental impact. While sand casting is ideal for low-volume runs and diverse materials, die casting shines in high-volume production of precise, complex parts. Understanding these differences allows manufacturers to choose the most suitable casting method for their projects, ultimately leading to more efficient production processes and higher-quality products.
Post time:Dis . 05, 2024 15:38
Next:Exploring Techniques and Advantages of Sand Casting in Manufacturing Processes