The Art and Science of Casting Sand A Pillar of Modern Manufacturing
Casting sand, often referred to as foundry sand, plays a pivotal role in the manufacturing industry, especially in the production of metal parts. It is a crucial material used in sand casting, a process that dates back thousands of years and remains integral to modern engineering and manufacturing practices. This article explores the significance of casting sand, its properties, and its applications, illustrating why it is often deemed the backbone of metal fabrication.
What is Casting Sand?
Casting sand is a specialized type of sand that is used to create molds for metal casting. It is primarily composed of silica grains, which provide the necessary heat resistance and durability. The characteristics of the sand, including its grain size, shape, and chemical composition, influence the quality of the cast products. Typically, foundry sand may also contain bentonite clay and other additives to enhance its binding properties and improve mold strength.
The most common type of casting sand is silica sand, recognized for its excellent thermal stability and ability to withstand the high temperatures experienced during the metal casting process. Other variations include zircon sand and chromite sand, each offering unique benefits tailored to specific applications.
Properties of Casting Sand
One of the defining features of effective casting sand is its flexibility
. The sand must be capable of retaining its shape while also allowing easy removal of the cast metal. This dual requirement is fulfilled through the careful selection of sand grain size and the mixing with binding agents. Moreover, the ability of the sand to absorb metal during the casting process is vital, ensuring that the final product is free from defects such as porosity or inclusions.casting sand
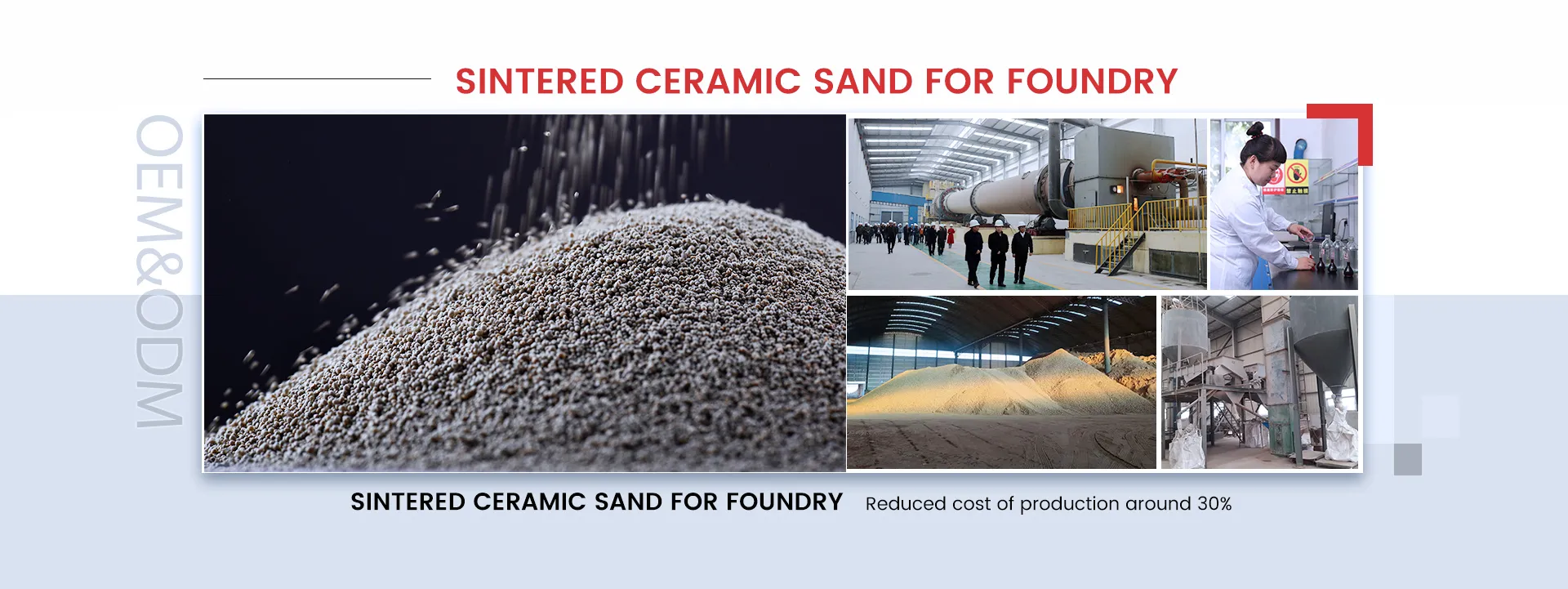
Manufacturers place a significant emphasis on the recycling and reusability of casting sand. After a casting operation, the sand can often be cleaned and reused multiple times, making it an economical and sustainable choice. This recycling process not only lowers production costs but also minimizes environmental impact, aligning with the growing emphasis on sustainable manufacturing practices.
Applications of Casting Sand
Casting sand is indispensable across a wide array of industries. It is commonly used in the automotive sector for producing engine blocks, transmission cases, and other crucial components. The aerospace industry also relies on casting sand for creating lightweight yet strong parts necessary for aircraft. Additionally, it finds applications in construction, art, and toy manufacturing, thanks to its versatility.
Furthermore, advancements in technology have propelled the development of new casting sand formulations, incorporating innovative materials that enhance performance. For instance, newer resin-bonded sands can create extremely fine surface finishes for intricate designs, catering to the needs of modern aerospace and medical device manufacturing.
Conclusion
In conclusion, casting sand remains a fundamental component of the manufacturing landscape. Its unique properties, coupled with the ability to be recycled and reused, make it a preferred choice for various industries. As manufacturing continues to evolve, so too will the applications and technologies surrounding casting sand. Its enduring significance highlights the blend of ancient techniques and modern science, ensuring that it will remain a cornerstone of metal fabrication for years to come.
Post time:Set . 25, 2024 11:16
Next:Understanding the Process and Benefits of Sand Casting in Metal Fabrication Industry