The Evolution of 3D Sand Printing in Casting
In recent years, 3D sand printing has emerged as a revolutionary technology within the field of metal casting, significantly transforming traditional manufacturing processes. This innovative approach utilizes advanced printing techniques to create molds from sand, offering remarkable precision and efficiency in producing complex metal components. The use of 3D printed sand molds and cores is redefining the landscape of casting by allowing for more intricate designs, reducing production time, and minimizing waste.
The Evolution of 3D Sand Printing in Casting
One of the key advantages of 3D sand printing is the ability to create complex geometries that were previously difficult or impossible to achieve with traditional methods. The technology allows for the production of intricate internal features, thin walls, and fine details, greatly enhancing the design flexibility. This capability not only enables engineers and designers to push the boundaries of their creativity but also optimizes material usage, as 3D printing can produce molds that are tailored precisely to the shape and function of the final metal part.
3d sand printing casting
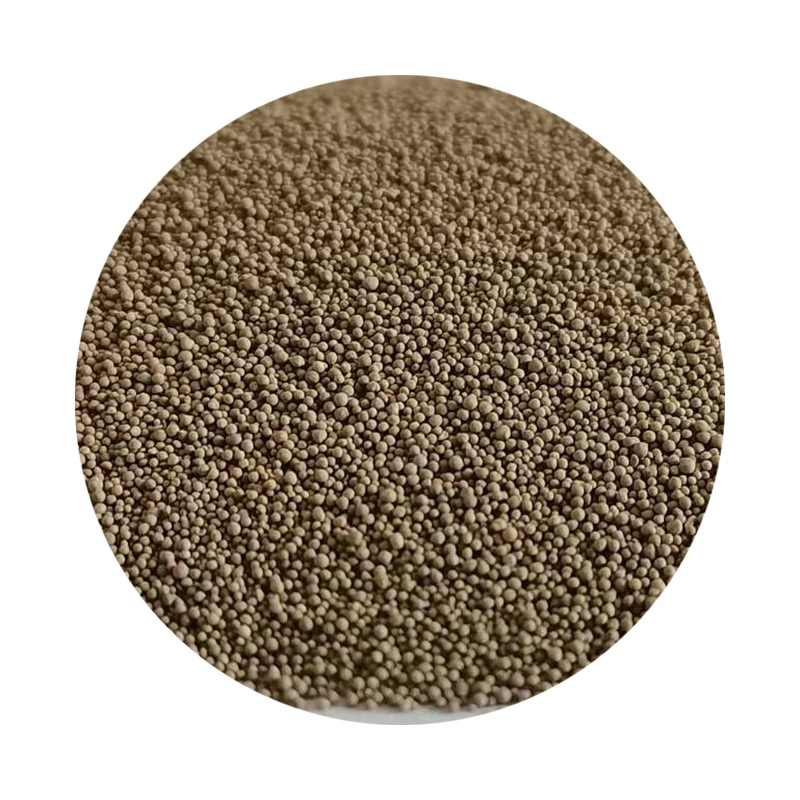
Moreover, 3D sand printing significantly reduces lead times. Traditionally, the process of creating molds could take days or even weeks due to the manual artistry involved. In contrast, 3D sand printers can produce molds in a matter of hours, enabling rapid prototyping and faster turnarounds for production runs. This agility is especially beneficial in industries where time-to-market can be a critical factor for maintaining competitiveness.
Additionally, sustainability is an increasingly important consideration in manufacturing, and 3D sand printing aligns well with this trend. By utilizing sand as a primary material, the process minimizes waste and can use recyclable materials. Traditional casting methods often generate substantial waste due to the excess sand and materials used. In contrast, 3D printing allows for more efficient use of resources, as molds can be created with precision, significantly reducing the amount of material consumed and the energy required for production.
Despite its numerous advantages, 3D sand printing in casting is not without challenges. The initial investment in 3D printing technology and equipment can be substantial, which may deter some companies from making the transition. Furthermore, there may be a learning curve associated with integrating this new process into existing manufacturing workflows. However, as the technology continues to evolve and more industries recognize its potential, it is likely that these barriers will be overcome.
In conclusion, 3D sand printing is revolutionizing the field of metal casting by enhancing design possibilities, improving production efficiency, and promoting sustainability. As industries embrace this innovative technology, we can expect to see a democratization of complex design capabilities and a shift towards more environmentally conscious manufacturing practices. The future of casting looks not only promising but also more dynamic, as 3D sand printing continues to reshape the way we think about and create metal components.
Post time:Okt . 06, 2024 22:58
Next:sand casting