The Future of Manufacturing 3D Printed Sand Casting
The manufacturing landscape is evolving at an unprecedented pace, and one of the most exciting advancements is the integration of 3D printing technologies into traditional manufacturing processes. Among these innovations, 3D printed sand casting is emerging as a revolutionary method, offering a myriad of benefits that stand to transform how we produce intricate metal components.
Understanding 3D Printed Sand Casting
3D printed sand casting combines the principles of additive manufacturing with the traditional casting process. In this method, a 3D printer is used to create a mold from sand mixed with a binding agent. The mold is printed layer by layer, allowing for complex geometries that would be difficult or impossible to achieve with conventional methods. Once the mold is completed, liquid metal is poured into it to create the desired part.
Advantages of 3D Printed Sand Casting
One of the primary advantages of 3D printed sand casting is design flexibility. Engineers and designers can create highly detailed and intricate designs without the constraints of traditional mold-making techniques. This capability not only fosters innovation in product development but also significantly reduces the time and cost associated with prototyping.
Moreover, this method minimizes waste material. Traditional sand casting often involves excess materials that need to be removed later, leading to increased costs and environmental impact. In contrast, 3D printing allows for precise control over the amount of material used, resulting in a more sustainable manufacturing process.
Another significant benefit is the reduction of lead times. Traditional sand casting typically requires a lengthy mold creation process, which can take days or even weeks. With 3D printing, molds can be produced in a matter of hours, enabling manufacturers to speed up production cycles and respond more swiftly to market demands.
3d printed sand casting
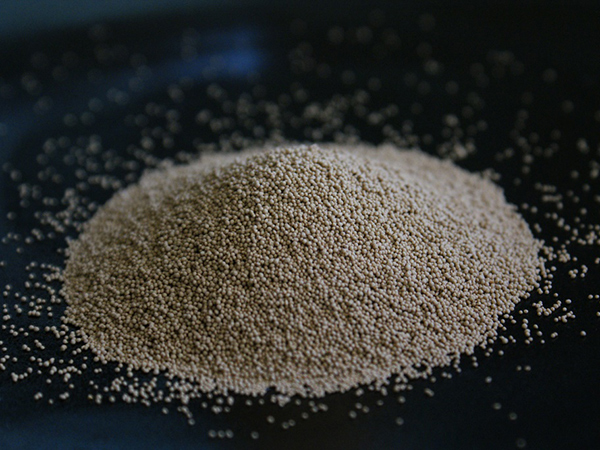
Applications Across Industries
3D printed sand casting is applicable across various industries, including aerospace, automotive, and heavy machinery. In the aerospace sector, for instance, the lightweight and complex structures that can be achieved through this method are invaluable for improving fuel efficiency and performance. Similarly, in the automotive industry, manufacturers can create custom components for vehicles that enhance both functionality and aesthetic appeal.
The heavy machinery sector also benefits significantly from 3D printed sand casting. Equipment parts that face extreme wear and tear can be produced with specific design features that prolong their lifespan, reducing maintenance costs and increasing operational efficiency.
Challenges and Future Outlook
Despite its numerous advantages, 3D printed sand casting does face some challenges. The technology is still relatively new, and there may be hesitance among industries to adopt it fully. Additionally, questions around the consistency and quality of printed molds compared to traditional methods remain a concern. However, ongoing research and development in the field of materials science and additive manufacturing technology are likely to address these issues.
Looking to the future, the potential for 3D printed sand casting remains vast. As the technology matures, we can expect to see even greater advancements that enhance its capabilities, further streamlining production processes. Businesses that leverage this technology can expect to gain a competitive edge, driving innovation, reducing costs, and improving sustainability in their operations.
Conclusion
3D printed sand casting is poised to redefine the manufacturing landscape by merging the best of both additive and traditional manufacturing techniques. With its advantages in design flexibility, waste minimization, and reduced lead times, it presents a promising solution for industries seeking efficiency and innovation. As we move forward, embracing this technology will be essential for any manufacturer aiming to thrive in an increasingly competitive market.
Post time:Okt . 20, 2024 20:39
Next:Understanding the Basics of Sand Casting in Metal Manufacturing Techniques