What is Sand Casting Process?
Sand casting is a widely used metal casting process that provides a cost-effective and efficient method for producing metal parts. It involves the use of sand as the primary molding material to create a mold into which molten metal is poured. This article will explore the sand casting process in detail, covering its advantages, applications, and the steps involved.
Advantages of Sand Casting
One of the primary advantages of sand casting is its versatility. This process can be used to cast a variety of metals, including iron, aluminum, bronze, and more. Furthermore, it can accommodate complex shapes and large parts, making it suitable for a wide range of applications. Another significant benefit is the relatively low cost associated with sand casting. The materials required—primarily sand and a binder—are inexpensive, and the equipment needed is readily available and does not require high initial investment.
Moreover, sand casting is highly adaptable. It allows for both small-scale production runs and large quantities of parts to be made. This adaptability makes it an ideal choice for both prototype development and large batch manufacturing. Additionally, sand molds can be reused several times, which contributes to the overall cost efficiency of the process.
Applications of Sand Casting
Sand casting is employed in various industries, including automotive, aerospace, construction, and art. In the automotive sector, for instance, sand casting is used to produce engine blocks, transmission cases, and other critical components. The aerospace industry utilizes sand casting to manufacture complex geometries required for aircraft parts. In construction, sand casting is often used for creating concrete molds, while artists use the process to create sculptures and custom art pieces.
Steps in the Sand Casting Process
The sand casting process can be broken down into several key steps
what is sand casting process
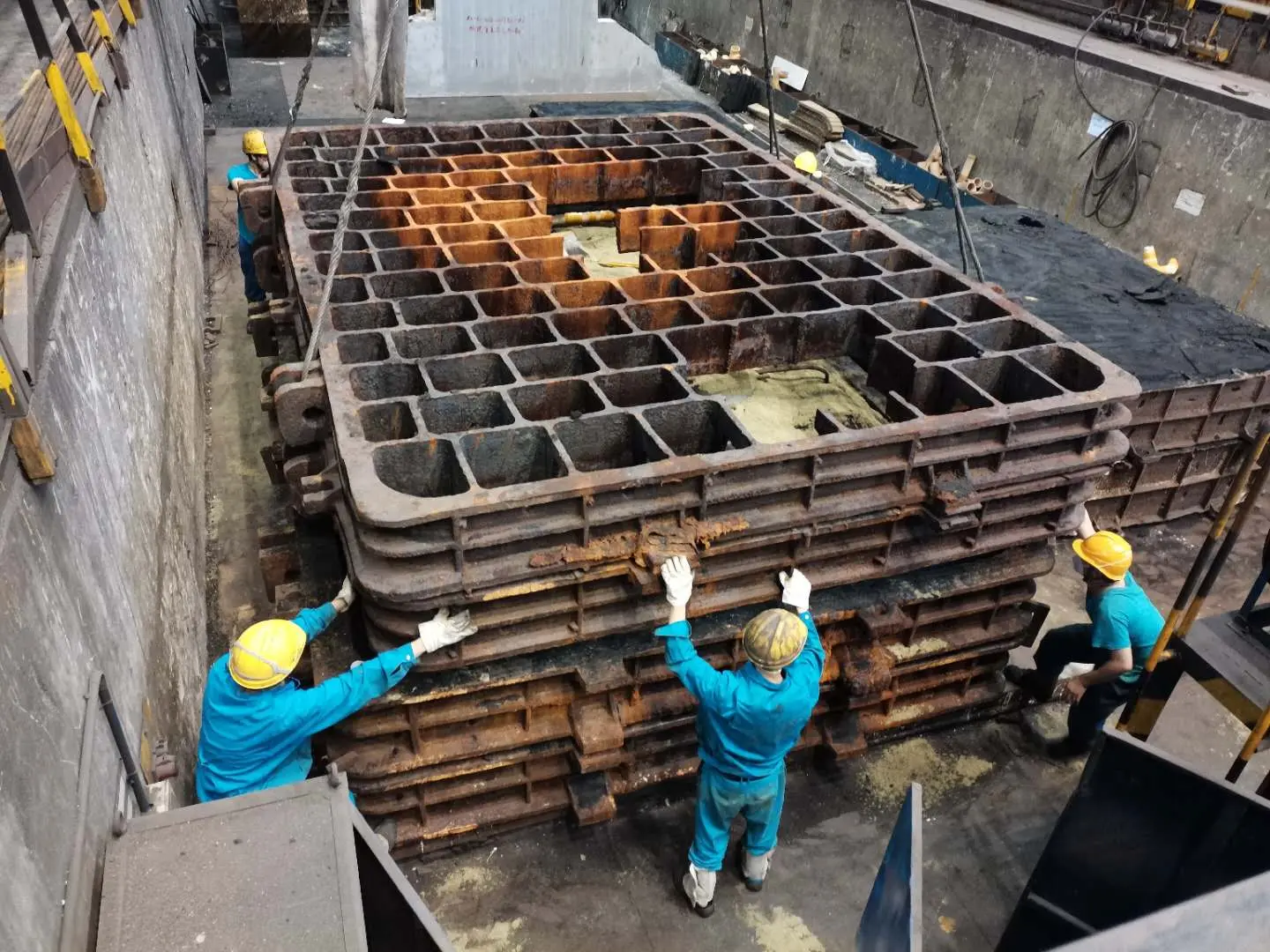
1. Pattern Making The first step involves creating a pattern, which is a replica of the final product. Patterns can be made from various materials such as wood, metal, or plastic. The pattern design must account for shrinkage of the metal and ensure proper draft angles for easy removal from the sand mold.
2. Mold Making The next step is making the mold. The sand is mixed with a binder to create a mixture that can hold its shape. This sand is then packed around the pattern in a mold box. Once the sand is compacted, the pattern is removed, leaving a cavity that represents the shape of the part to be cast.
3. Melting the Metal The chosen metal is then melted in a furnace. The metal must reach a specific temperature to ensure that it flows easily into the mold.
4. Pouring Once the metal is molten, it is carefully poured into the mold cavity through a pouring cup or sprue. This step requires precision to avoid imperfections in the final casting.
5. Cooling After the metal is poured, it is allowed to cool and solidify. Cooling time varies depending on the size and type of metal used.
6. Mold Removal Once the metal has cooled sufficiently, the sand mold is broken away to reveal the cast part. This is often done through vibration or shaking, which helps release the sand.
7. Finishing Finally, the casting may require additional finishing processes such as machining, grinding, or surface treatment to achieve the desired surface finish and dimensional accuracy.
Conclusion
In summary, sand casting is a fundamental process in the manufacturing of metal parts that offers impressive versatility and cost-effectiveness. By understanding the various steps involved in the sand casting process, manufacturers can efficiently produce high-quality metal components suitable for a wide range of applications. Whether used for industrial or artistic purposes, sand casting remains a pivotal technique shaping modern production methods.
Post time:des. . 16, 2024 23:02
Next:3d sand printer price