Wet Sanding 3D Prints A Guide to Achieving a Smooth Finish
3D printing has revolutionized the way we create objects, allowing for unmatched customization and rapid prototyping. However, the transition from digital model to a tangible product often comes with its own set of challenges, especially when it comes to surface finish. One effective technique to enhance the smoothness and appearance of 3D prints is wet sanding. This article explores the benefits of wet sanding, the process involved, and some tips to achieve the best results.
What is Wet Sanding?
Wet sanding is a finishing process that involves sanding a surface with the addition of water or another lubricant. Unlike traditional dry sanding, wet sanding reduces friction, which helps to minimize dust and debris while producing a smoother finish. This method is particularly beneficial for 3D printed parts, which can have visible layers and imperfections typical of the FDM (Fused Deposition Modeling) process.
Benefits of Wet Sanding
1. Smoother Finish One of the primary advantages of wet sanding is the ultra-smooth finish it can achieve. The water lubricates the sandpaper, allowing it to glide over the surface without scratching it, which can lead to a polished look that is ideal for display models or functional parts.
2. Reduced Dust and Particles Wet sanding significantly reduces the amount of dust created compared to dry sanding. This creates a cleaner working environment and minimizes the risk of inhaling particulate matter.
3. Less Clogging When sanding materials like PLA, ABS, or PETG, dry sanding tends to clog the sandpaper quickly. Wet sanding helps to wash away debris, prolonging the lifespan of the sandpaper and enabling more effective sanding.
4. Better Control The lubrication provided by water allows for better control of the sanding process. This means fewer mistakes and a greater ability to focus on specific areas of the print that require extra attention.
The Wet Sanding Process
wet sanding 3d prints
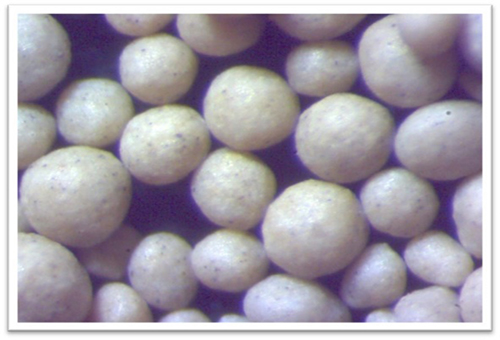
To effectively wet sand your 3D prints, follow these steps
1. Preparation Begin by removing any large imperfections from your print using a coarse sandpaper (around 120-220 grit). This initial sanding should be done dry before transitioning to the wet sanding phase.
2. Gather Materials You will need wet/dry sandpaper (typically ranging from 400 to 2000 grit), a water source, and a container to capture any runoff. You may also choose to add a few drops of dish soap to your water to improve lubrication.
3. Start Wet Sanding Dip the sandpaper into water and gently sand the print using circular motions. It's essential to keep the sandpaper wet throughout the process to prevent clogging and to allow particles to wash away. Start with lower grit sandpaper, gradually moving to higher grit for a finer finish.
4. Regularly Check Your Work Frequently rinse the print under running water to assess the surface’s smoothness. This will help determine if you need to switch to a finer grit sandpaper.
5. Final Rinse and Drying Once you are satisfied with the smoothness of the surface, thoroughly rinse your print to remove any residual debris and water. Allow it to dry completely before proceeding to any additional finishing steps, such as painting or applying a clear coat.
Tips for Success
- Be Patient Achieving a perfectly smooth finish takes time. Rushing the process can lead to uneven surfaces or even damage to your print. - Test on Scraps Before working on your main print, practice on a scrap piece of filament to get a feel for how the material responds to wet sanding. - Ventilation Although wet sanding minimizes dust, it's still wise to work in a well-ventilated area and wear appropriate safety gear, especially if your print material produces fumes.
In conclusion, wet sanding is a fantastic technique for enhancing the surface finish of 3D printed objects. With proper preparation and technique, you can transform your prints from rough to sleek, making them ready for display or use. Whether you're a hobbyist or a professional, incorporating wet sanding into your finishing process can elevate your 3D printing projects to the next level.
Post time:des. . 19, 2024 07:51
Next:Innovative Techniques in 3D Sand Printing for Enhanced Casting Applications