Understanding Sand Casting Processes
Sand casting is one of the oldest manufacturing processes, revered for its simplicity and versatility. This method involves creating a mold from a mixture of sand, clay, and water, into which molten metal is poured to create a desired shape. Sand casting is widely used in industries ranging from automotive to aerospace, and here we delve into the intricacies of this process, its advantages, and applications.
The Basics of Sand Casting
The sand casting process begins with the creation of a pattern, which is typically made from metal, plastic, or wood and represents the final shape of the cast object. This pattern is used to form the mold. The first step involves compacting sand around the pattern in a mold box. The sand is often mixed with a bonding agent like clay to ensure that it holds shape. Once the pattern is removed, a cavity in the shape of the object remains.
Two halves of the mold are then assembled and held together. Before pouring in the molten metal, the mold must be treated to ensure it can withstand the high temperatures and to facilitate the release of the finished product. This can involve applying a release agent or preheating the mold.
Pouring the Metal
Once the mold is ready, the next step is pouring the molten metal. The choice of metal can vary depending on the desired properties of the final product, with common choices including aluminum, iron, and copper alloys. The transformation of metal from solid state to liquid is carefully controlled to prevent defects such as porosity or inclusions in the cast.
After the metal is poured, it takes time to cool and solidify. The cooling process is critical, as the rate of cooling affects the microstructure of the cast, which in turn influences mechanical properties. Once cooled, the sand mold is broken away, revealing the cast product.
sand casting processes
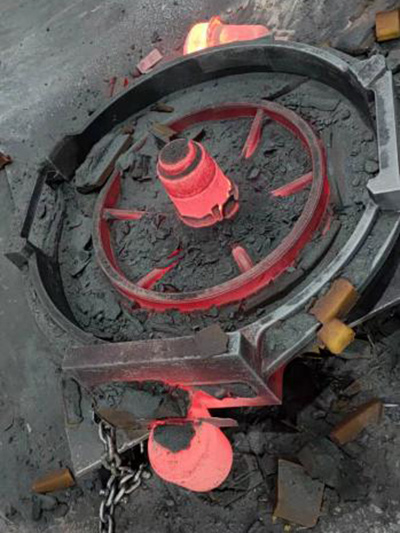
Advantages of Sand Casting
One of the primary advantages of sand casting is its cost-effectiveness, especially for large parts and intricate shapes. The process allows for the production of complex geometries without the need for expensive tooling. Additionally, the use of sand as a mold material provides excellent thermal insulation, enabling better control over the cooling rate and reducing the risk of defects.
Sand casting also boasts a high degree of flexibility. It can accommodate a range of metal types and can be adapted for both small and large production runs. This adaptability makes it an ideal choice for prototyping or when specific and unique designs are required.
Applications of Sand Casting
Sand casting is employed across various industries. In the automotive sector, it is used to produce engine blocks, transmission housings, and brake components. The aerospace industry utilizes sand casting for lightweight and robust components necessary for aircraft and spacecraft. Additionally, art and sculpture creation often rely on sand casting techniques to produce intricate designs.
Furthermore, the growing trend towards sustainable manufacturing practices has led to an increased interest in green sand casting, which utilizes more environmentally friendly materials and processes, reducing the carbon footprint associated with traditional methods.
Conclusion
The sand casting process stands as a testament to the ingenuity of traditional manufacturing techniques. By merging age-old practices with modern technology, sand casting continues to evolve, maintaining its relevance in a rapidly advancing technological landscape. Its combination of adaptability, cost-efficiency, and capability to produce complex shapes ensures that sand casting will remain a crucial method in the manufacturing world for years to come. Whether creating automotive parts or artistic sculptures, the sand casting process holds a significant place in the heart of industrial production.
Post time:des. . 03, 2024 18:10
Next:dry sand casting