The Importance of Sand Casting in the Foundry Industry
Sand casting, one of the oldest and most widely used manufacturing processes, plays a vital role in the foundry industry. This method has been utilized for centuries to create metal parts and products, and despite advancements in technology, it remains integral due to its simplicity, cost-effectiveness, and versatility. Understanding the significance of sand casting can provide insights into its enduring popularity in manufacturing.
Process Overview
The sand casting process involves several steps. First, a pattern, usually made of metal or plastic, is created to shape the final product. This pattern is then placed into a mold box, and sand mixed with a binding agent is packed around it. Once the sand is set and the pattern is removed, a mold cavity is formed. After that, molten metal is poured into the mold to create the desired shape. Once the metal cools and solidifies, the sand mold is broken away to reveal the finished cast product.
The flexibility of sand casting allows it to accommodate a wide variety of shapes and sizes. It can produce anything from small intricate components to large heavy parts, making it ideal for industries such as automotive, aerospace, and construction.
Cost-Effectiveness
One of the key advantages of sand casting is its cost-effectiveness. The materials used—primarily sand—are inexpensive and readily available. Moreover, the sand molds can be reused multiple times, further reducing production costs. This makes sand casting an attractive option for manufacturers looking to minimize expenses. While initial setup costs for patterns can be significant, the low cost of materials and the ability to produce complex shapes without the need for extensive additional tooling contributes to its overall affordability.
Versatility and Complexity
sand cast foundry
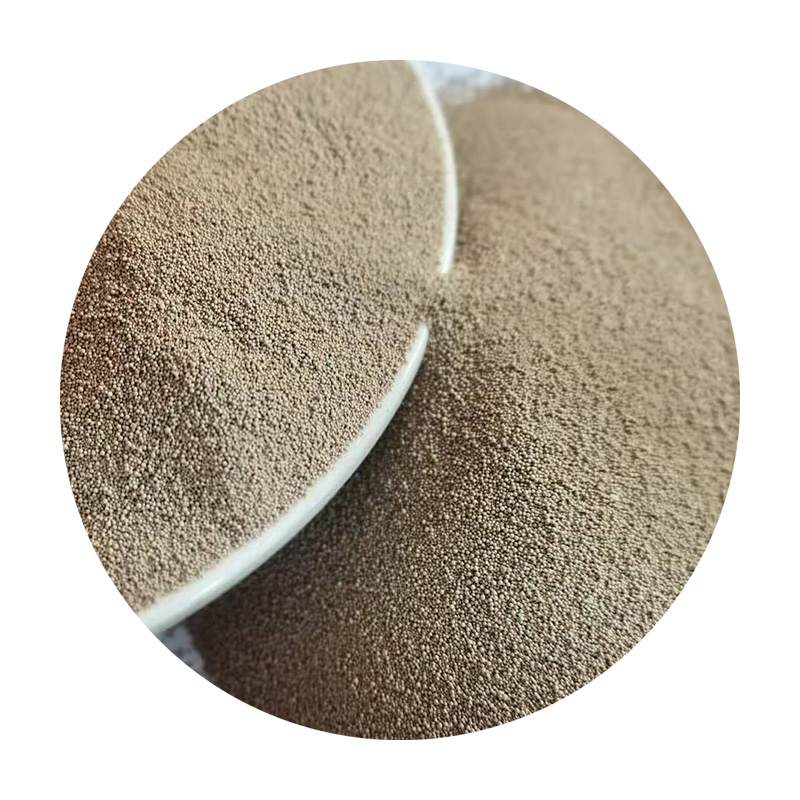
Another important benefit of sand casting is its versatility. It can be used to cast a range of metals, including aluminum, iron, and bronze, and can produce intricate designs that are difficult to achieve with other casting methods. Additionally, sand casting can accommodate various production volumes, from single prototypes to large-scale production runs. This flexibility makes it suitable for small businesses and large industrial manufacturers alike.
Furthermore, advancements in technology, such as 3D printing for patterns and molds, have enhanced the capabilities of sand casting. This integration allows for more complex geometries and precise designs, pushing the boundaries of what can be achieved through traditional processes.
Quality and Strength
The quality of products derived from sand casting is another significant factor in its continued use. Cast products often exhibit excellent strength and durability, which is essential for applications that require robust components. The cooling rate of the molten metal in sand molds promotes the development of favorable microstructures, resulting in high-quality final products.
However, it is crucial for manufacturers to maintain strict quality control throughout the process. Factors such as sand composition, moisture content, and pouring techniques can significantly influence the quality of the casted parts. By adhering to meticulous practices, foundries can ensure that their sand-cast components meet the required specifications and performance standards.
Conclusion
In conclusion, sand casting remains a cornerstone of the foundry industry due to its cost-effectiveness, versatility, and ability to produce high-quality components. Its simplicity allows for the production of a diverse range of parts, making it a go-to method for many manufacturers. Even as technology advances and new casting methods emerge, the traditional art of sand casting continues to be relevant, demonstrating the enduring significance of this remarkable process in modern manufacturing. As industries evolve and demand for complex, high-quality products increases, the sand casting process is likely to adapt and thrive, securing its position in the future of manufacturing.
Post time:des. . 16, 2024 06:03
Next:steps in sand casting