Sand Casting Iron A Timeless Technique in Metalworking
Sand casting is one of the oldest and most versatile methods of metal casting, and it plays a critical role in the production of iron components. This process involves creating a mold from sand and pouring molten iron into the cavity to produce various shapes and sizes. Its simplicity and adaptability make sand casting a preferred technique for many industries, from automotive to aerospace.
At its core, sand casting involves using a mixture of sand, clay, and water to create a mold. The mold is formed around a pattern, typically made from wood or metal, which provides the shape of the final product. Once the pattern is placed in the sand mixture, it is compacted to form a sturdy mold. After the mold is created, the pattern is removed, leaving a cavity that mirrors its shape.
Sand Casting Iron A Timeless Technique in Metalworking
Iron is a prevalent material used in sand casting, primarily due to its availability and favorable properties. Cast iron, for instance, is one of the most widely used forms of iron in sand casting. It has excellent fluidity, making it easy to pour into molds, and it solidifies to form a hard and durable final product. The ability to incorporate various alloying elements also allows for the customization of cast iron to meet specific strength, wear resistance, and machinability requirements.
sand casting iron
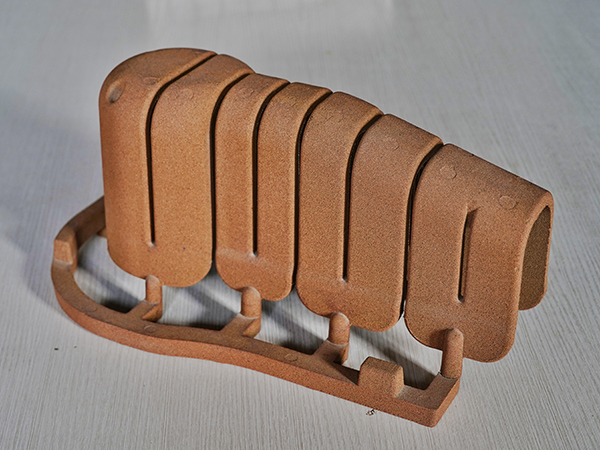
Environmental considerations have also influenced sand casting as a preferred method. Modern practices in sand casting emphasize recycling and sustainability. The sand used in molds can often be reclaimed and reused multiple times, significantly reducing waste. Furthermore, advancements in sand casting technology, such as the implementation of green sand and no-bake processes, have minimized the environmental impact associated with traditional casting methods.
The sand casting process generally includes several key steps preparing the mold, pouring the molten iron, cooling, and finishing. After the molten iron is poured into the mold, it is allowed to cool and solidify. Once adequate cooling has occurred, the sand mold is broken away, revealing the cast iron object. Subsequent finishing processes such as grinding, machining, or polishing may then be applied to achieve the desired surface quality and dimensions.
In recent years, the integration of modern technology, such as computer-aided design (CAD) and simulation software, has transformed traditional sand casting practices. These tools enhance precision, reduce lead times, and improve overall efficiency, allowing manufacturers to produce high-quality castings more effectively.
In conclusion, sand casting iron remains a fundamental process in metalworking. Its ability to produce intricate designs, combined with the favorable properties of cast iron, ensures its continued relevance in various industries. The advancements in technology and sustainability practices further solidify its importance in modern manufacturing, making sand casting a timeless technique that is both practical and efficient. As industries evolve, sand casting will undoubtedly adapt, continuing to be a vital part of the casting landscape for years to come.
Post time:set. . 05, 2024 10:14
Next:Coated Sand Solutions for Enhanced Performance in Construction and Manufacturing