Molding Sand for Metal Casting
Molding sand is a vital material in the metal casting industry, serving as the primary medium through which metal is poured and shaped into desired forms. Its unique properties make it an ideal choice for various casting processes, such as sand casting, where molds are formed to hold molten metal until it solidifies. Understanding the composition, types, and characteristics of molding sand can profoundly influence the quality and efficiency of metal casting.
Composition of Molding Sand
The key component of molding sand is silica sand, which provides the bulk of the material. Silica, or silicon dioxide (SiO2), contributes to the sand’s ability to withstand high temperatures and forms a stable mold. Besides silica, molding sand often contains additives that enhance its properties. These can include clay, which binds the sand grains together; water, which serves to hydrate the clay and improve mold strength; and various chemical additives that can influence the sand’s cohesion, permeability, and flexibility.
Types of Molding Sand
There are several types of molding sands used in the metal casting process, each with distinct characteristics suited for specific applications
1. Green Sand This is the most commonly used molding sand and consists of a mixture of silica sand, clay, and water. It is called green because it is not baked or hardened. Green sand is cost-effective and allows for excellent mold replication and thermal stability, making it suitable for ferrous and non-ferrous metals.
2. Dry Sand In contrast to green sand, dry sand is molded in a dry state, resulting in molds that are more rigid and capable of producing high-quality surface finishes. Dry sand is often used for larger castings or when a finer detail is required.
3. Skin-Dried Sand This type of sand is coated with a thin layer of moisture, which makes it easy to handle while still providing some of the strength and detail benefits of dry sand, suitable for specific casting processes.
molding sand for metal casting
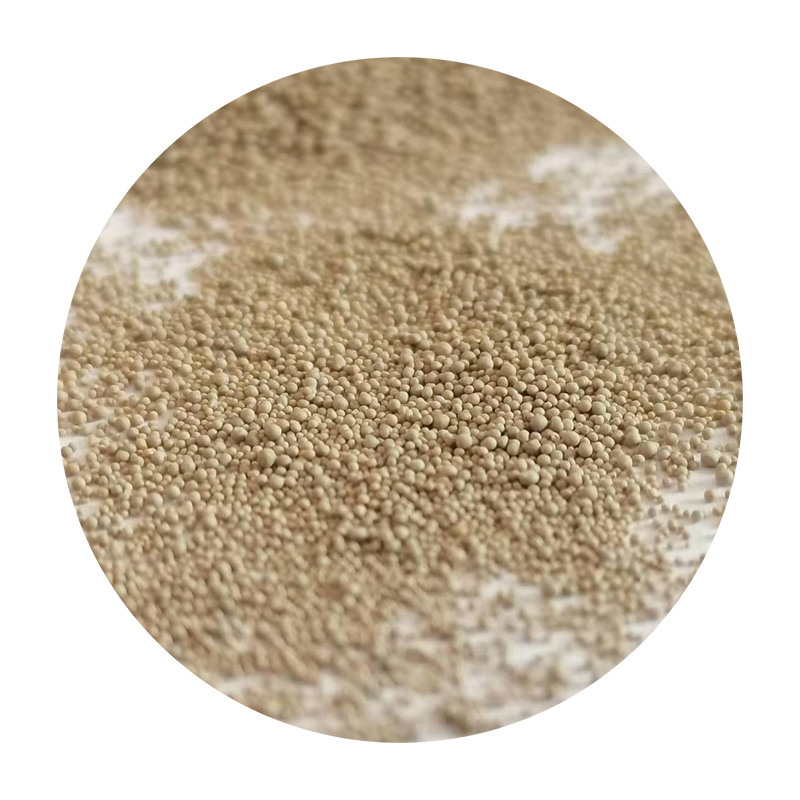
4. Loam Sand Loam sand is a mixture of sand, clay, and water, but it has a higher proportion of clay. This type of sand is often used in large-scale casting operations, such as in the production of larger components like engine blocks.
Characteristics of Molding Sand
The performance of molding sand is dictated by its characteristics, which include
- Permeability The ability of the sand to allow gases to escape during the casting process. High permeability prevents defects caused by trapped gases, crucial for maintaining the integrity of the casting.
- Strength A strong mold can withstand the pressure of molten metal without breaking down. Molding sands are formulated to have sufficient mechanical strength to support the weight of the metal while maintaining their shape.
- Thermal Stability The ability of the sand to withstand the high temperatures of molten metal is vital. Molding sand should not deform or burn away upon contact with the liquid metal.
- Reusability One of the significant advantages of molding sand is its reusability. After the casting process, sand can often be reclaimed, cleaned, and reused for future molds, making it an economically advantageous choice.
Conclusion
Molding sand plays an indispensable role in the metal casting industry. Its unique composition, variety of types, and essential characteristics enable metal to be shaped into intricate designs and robust structures. As the industry continues to evolve, advancements in molding sand technology promise to further enhance casting processes, contributing to the production of superior metal components across various sectors. Understanding and optimizing the use of molding sand is thus crucial for achieving high-quality results in metal casting operations.
Post time:set. . 13, 2024 01:56
Next:Fundição em Espuma Perdida - Método Inovador para Alta Precisão