Understanding Foundry Sand Composition, Importance, and Recycling
Foundry sand is a crucial material in the metal casting industry, playing a vital role in shaping and forming metal parts with precision and efficiency. This specific type of sand is primarily used in the production of molds and cores, which are instrumental in the casting process of metals, including aluminum, iron, and steel. Its unique properties and composition make it an essential resource in modern manufacturing.
Composition of Foundry Sand
Foundry sand is predominantly composed of silica (SiO2), making up about 90% of its composition. The high silica content provides excellent thermal stability, allowing the sand to withstand the high temperatures encountered during the metal casting process. In addition to silica, foundry sand may also include clay, which acts as a binding agent, and other additives to enhance its performance during casting.
There are two main types of foundry sand green sand and resin-bonded sand. Green sand consists of a mixture of sand, clay, and water, making it moisture-rich and malleable. It is widely favored for its ability to create complex shapes with smooth surfaces. On the other hand, resin-bonded sand uses synthetic resins as a binding agent, providing greater strength and stiffness. This type of sand is often employed in precision casting applications, as it allows for finer detail and better dimensional accuracy.
Importance of Foundry Sand in Metal Casting
The significance of foundry sand in metal casting cannot be overstated. Its ability to withstand extreme heat and maintain structural integrity under pressure makes it ideal for creating molds that can handle molten metal. The sand's thermal properties ensure that it does not break down under high temperatures, which is vital for producing high-quality castings.
making foundry sand
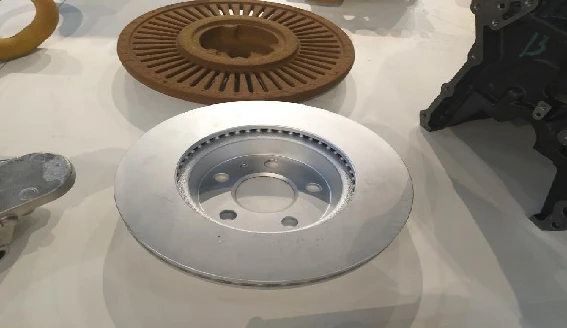
Additionally, foundry sand contributes to the efficiency of the casting process. The use of sand molds allows for rapid production cycles and the ability to create multiple casts without significant downtime. This efficiency translates into cost savings for manufacturers, as they can produce high volumes of parts in a shorter amount of time.
Moreover, foundry sand plays a crucial role in achieving the desired surface finish and accuracy of cast products. The fine grains of the sand create a smooth surface, reducing the need for extensive post-casting machining. This quality is particularly important in industries where precision is critical, such as aerospace and automotive manufacturing.
Sustainability and Recycling of Foundry Sand
As environmental concerns continue to grow, the recycling and sustainable management of foundry sand have gained significant attention. A considerable amount of waste sand is generated during the casting process, leading to environmental challenges if not managed properly. Fortunately, many foundries are now adopting recycling practices that allow them to reclaim used sand for reuse in new molds.
Recycling foundry sand not only conserves natural resources but also reduces landfill waste and the environmental impact of mining virgin sand. The reuse of foundry sand can be done through various processes, including thermal reclamation, where high temperatures are used to remove impurities, and mechanical reclamation, which involves sieving and cleaning the sand for reuse. In addition to reducing waste, these practices can result in cost savings for foundries, as they spend less on purchasing new sand.
Conclusion
In conclusion, foundry sand is an integral component of the metal casting industry, essential for producing high-quality metal parts efficiently. Its unique properties, combined with the increasing emphasis on sustainability, highlight the importance of innovative practices in managing foundry sand resources. By prioritizing recycling and reclamation, the industry can pave the way for a more sustainable future while continuing to meet the demands of modern manufacturing.
Post time:nov. . 08, 2024 09:06
Next:Reasons for the Popularity of Sand Casting in Manufacturing Processes