Exploring Large Sand Casting Techniques and Benefits
Large sand casting is a prominent manufacturing process utilized in various industries to create sizable metal components with precision and efficiency. Sand casting, a technique that has been relied upon for centuries, involves pouring molten metal into a sand mold, which subsequently is allowed to cool and solidify. This method is particularly advantageous for producing large components due to its adaptability, cost-effectiveness, and ability to achieve intricate shapes.
One primary reason for the popularity of large sand casting is its versatility. The process can accommodate a wide range of metals, including aluminum, iron, and bronze. This flexibility allows manufacturers to select materials that best fit their project requirements based on factors like strength, weight, and corrosion resistance. Furthermore, large sand casting can be utilized to create complex geometries that would be difficult or impossible to achieve with other manufacturing techniques.
The sand casting process begins with the creation of a mold, typically made from a mixture of sand, clay, and water. This mixture is compacted around a pattern that resembles the final product, forming a cavity. Once the mold is prepared, the pattern is removed, leaving behind a void that will define the shape of the casting. The sand mold’s ability to withstand high temperatures ensures that it can handle the molten metal poured into it, making the process reliable for producing large components, such as engine blocks and large machinery parts.
large sand casting
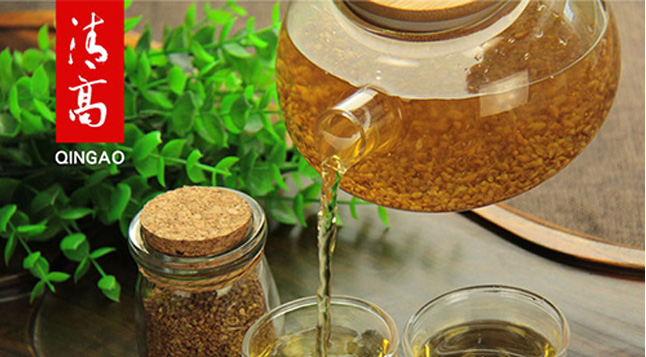
Moreover, large sand casting offers excellent scalability for production. Whether a single prototype is needed or a large batch of components, sand casting can be adapted accordingly. For instance, when creating small quantities, manufacturers can use a wooden or plastic pattern to produce molds. For larger production runs, metal patterns are used to enhance durability and improve mold accuracy. This scalability is crucial for industries such as automotive and aerospace, where both limited runs of specialized parts and large volumes of standard components are often required.
Another significant advantage of large sand casting is its cost-effectiveness compared to other manufacturing processes, such as die casting or machining. The materials used in sand molds are typically less expensive, and the process allows for a high degree of material utilization with minimal waste. Additionally, the setup costs for sand casting can be lower, particularly for less complex geometries, enabling manufacturers to reduce their overall production expenses.
From an environmental perspective, large sand casting is also increasingly adopting sustainable practices. Many foundries are exploring ways to recycle sand and reduce waste in the casting process, contributing to a more eco-friendly manufacturing environment. Efforts to improve energy efficiency in melting and pouring operations also signal a growing commitment to sustainability within the industry.
In conclusion, large sand casting is a fundamental process in manufacturing that combines versatility, cost-effectiveness, and the ability to produce complex shapes. Its advantages make it an appealing choice for industries requiring large metal components. As technology continues to evolve, the future of large sand casting looks promising, with ongoing advancements in materials, methods, and sustainability practices poised to enhance its role in modern manufacturing.
Post time:oct. . 17, 2024 05:47
Next:Innovative Ceramics Solutions for Enhanced Performance and Durability in Various Applications