Different Types of Foundry Sand
Foundry sand plays a crucial role in the metal casting process, serving as a mold material that forms the shape of the final product. The type of sand chosen can greatly influence the quality, integrity, and cost-effectiveness of the castings produced. Here, we explore the different types of foundry sand, their properties, and their applications in the metal casting industry.
1. Silica Sand
Silica sand is the most common type of foundry sand used in casting operations. Composed primarily of silicon dioxide (SiO2), it offers excellent thermal stability, a high melting point, and good flowability. Silica sand is often processed to remove impurities, ensuring that it has the desired grain size and shape. Its use is particularly prominent in the manufacture of ferrous and non-ferrous casting molds. However, due to its crystalline structure, workers may be at risk for respiratory illnesses if proper safety protocols are not followed.
2. Olivine Sand
Olivine sand is a natural sand derived from the mineral olivine. This type of sand is gaining popularity due to its unique properties, including a high melting point and resistance to thermal shock. Olivine sand is also characterized by its angular particles, which improve the strength of molds and cores while reducing the amount of binding agents needed. Its ability to withstand high temperatures makes it suitable for ferrous and non-ferrous castings, as well as in applications where reduced metal penetration is desired.
3. Chromite Sand
different types of foundry sand
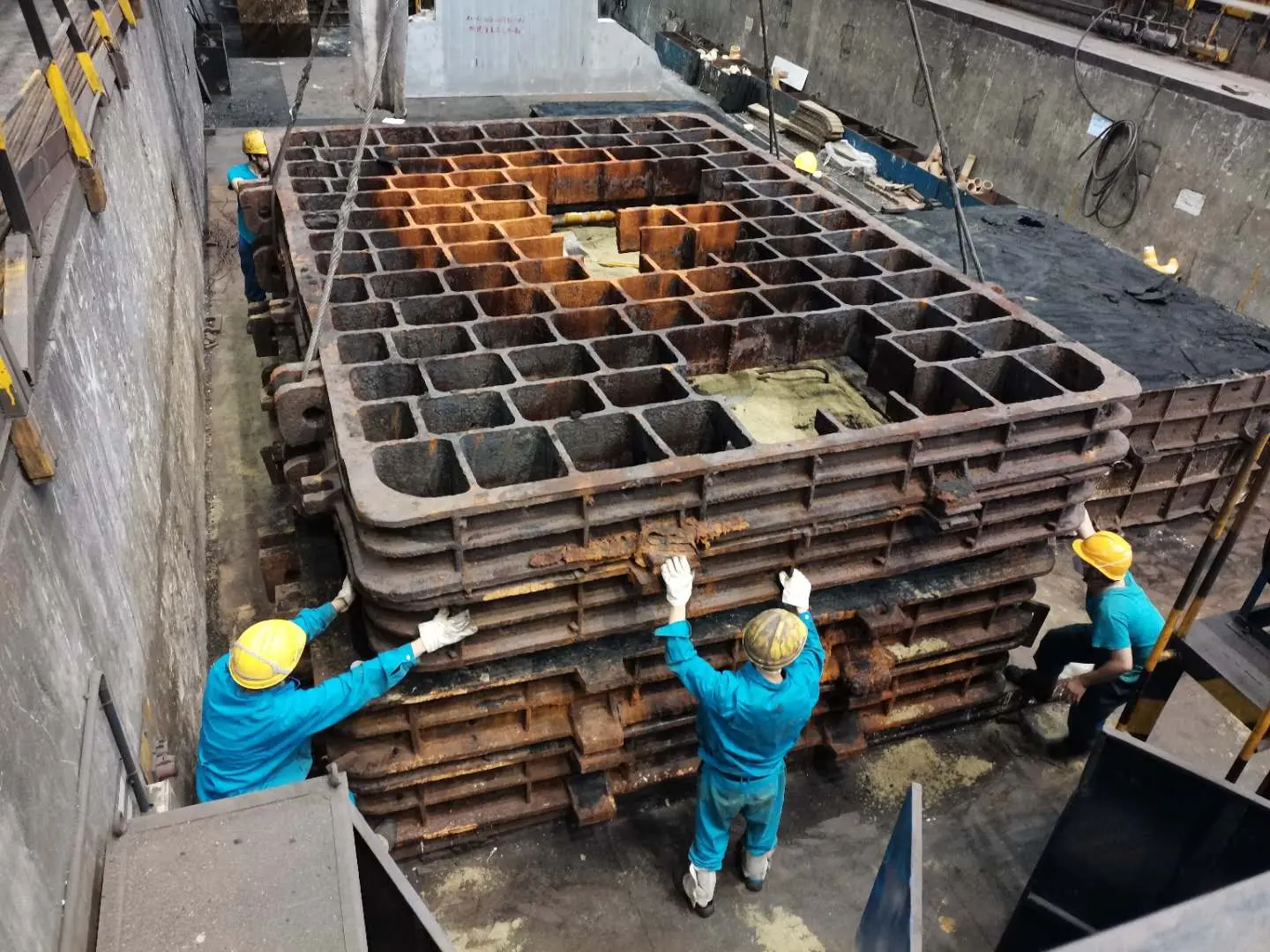
Chromite sand is another specialized type of foundry sand, produced from the mineral chromite. Renowned for its high thermal stability and low thermal expansion, chromite sand is ideal for investment casting, particularly in industries that require high-precision components, such as aerospace and automotive. It also provides excellent resistance to metal penetration and is often used in the production of molds and cores for high-quality castings.
4. Zircon Sand
Zircon sand, derived from the mineral zirconium silicate, is used in high-performance applications due to its superior thermal properties and chemical stability. It has a low expansion rate, which minimizes defects associated with thermal expansion during casting. Zircon sand is often used in investment casting and in applications requiring high dimensional accuracy, such as in the manufacturing of turbine blades or intricate engine components.
5. Resin Coated Sand
Resin-coated sand is a mixture of sand and a resin binder. This type of sand is used primarily in the shell molding process, where a thin shell of sand and resin is formed over a heated pattern. The resulting molds are exceptionally strong and can withstand higher temperatures, making them suitable for high-quality castings with excellent surface finishes. The flexibility derived from the resin coating allows for the production of complex patterns that might be difficult to achieve with traditional sand.
Conclusion
Each type of foundry sand brings distinct advantages and is selected based on the specific requirements of the casting process. From the commonly used silica sand to advanced options like zircon and resin-coated sands, the choice of material can significantly impact the quality and performance of metal castings. By understanding the properties and applications of different foundry sands, manufacturers can optimize their processes to produce superior castings that meet industry standards and customer expectations. As innovations continue to emerge in the foundry industry, the development of new sand types and processing techniques will likely enhance the capabilities of metal casting even further.
Post time:des. . 20, 2024 23:19
Next:history of sand casting