Understanding Sand Casting A Comprehensive Overview
Sand casting, also known as sand mold casting, is one of the most versatile and widely used metal casting processes. This method has been utilized for centuries and remains a dominant technique in various industries due to its simplicity and efficiency. In this article, we will explore what sand casting is, its process, advantages, applications, and some considerations for its use.
What is Sand Casting?
Sand casting is a manufacturing process that involves pouring molten metal into a mold made from sand. The sand mold forms the shape of the object to be created, and once the metal cools and solidifies, the mold is removed to reveal the final product. This technique can accommodate a wide variety of metals, including aluminum, bronze, iron, and steel.
The Sand Casting Process
The sand casting process consists of several essential steps
1. Pattern Making The first step involves creating a pattern, which is a replica of the object to be cast. Patterns can be made from wood, metal, or plastic, and they are designed slightly larger than the finished product to account for shrinkage of the metal during cooling.
2. Mold Preparation The pattern is then placed in a frame, called a flask, and sand is packed around it to form a mold. The most common type of sand used is a mixture of silica sand, clay, and water. The clay acts as a binder, helping the sand retain its shape.
3. Core Making In cases where the casting requires internal features, cores made of sand are inserted into the mold. These cores create hollow sections within the casting.
4. Pouring Once the mold is prepared and the pattern removed, it is ready for pouring. Molten metal is heated to the desired temperature and then poured into the mold cavity.
5. Cooling and Solidification The metal in the mold is allowed to cool and solidify. The cooling time varies based on the metal type and the size of the casting.
6. Mold Removal After cooling, the sand mold is broken apart to extract the casting. The sand can often be recycled for future use, making the process more sustainable.
7. Finishing The final step involves cleaning the casting to remove any sand, gates, or excess material. Finishing processes can include grinding, machining, or any additional treatment to achieve the desired surface quality.
Advantages of Sand Casting
Sand casting offers several advantages that make it a preferred choice across various applications
what is sand casting
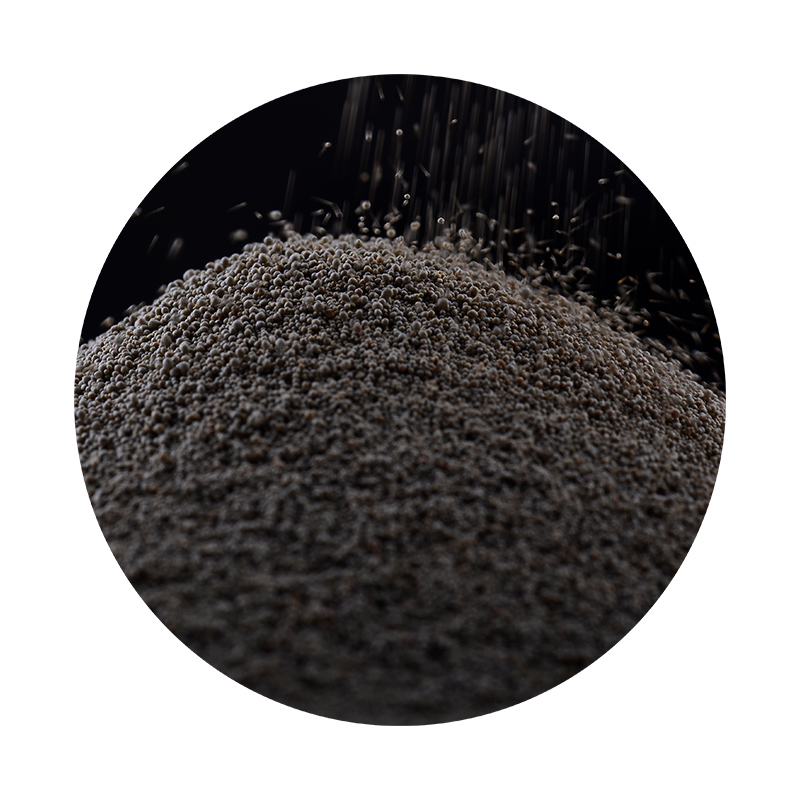
- Cost-Effectiveness The raw materials used in sand casting, primarily sand, are inexpensive and widely available. This makes the process economical, especially for large production volumes.
- Versatility Sand casting can produce a diverse range of complex shapes and sizes. It can accommodate various types of metals, making it suitable for numerous applications.
- Low Setup Costs Unlike other casting methods that require expensive machinery and equipment, sand casting can be performed with relatively simple tools, reducing initial investment costs.
- Large Scale Production This method is capable of producing both small and large quantities of parts efficiently
.Applications of Sand Casting
Sand casting is utilized in a multitude of industries, including
- Automotive Components like engine blocks, cylinder heads, and transmission cases are commonly produced using sand casting.
- Aerospace Critical parts that require high precision and strength can be effectively cast through this process.
- Consumer Products Household items, decorative pieces, and tools are often made using sand casting techniques.
Considerations in Sand Casting
While sand casting is highly beneficial, some considerations must be taken into account
- Surface Finish The surface finish of sand castings often requires additional machining or finishing to meet specific requirements.
- Dimensional Accuracy While sand casting can produce complex shapes, the dimensional tolerance may not be as tight as other casting methods, such as investment casting.
- Environmental Impact Although the sand can be reused, the process may still produce waste, necessitating proper handling and disposal.
In conclusion, sand casting is a time-honored method that continues to play a vital role in modern manufacturing. Its advantages in terms of cost-effectiveness, versatility, and capability for large-scale production make it an enduring choice for producing a wide variety of components across numerous industries.
Post time:okt . 13, 2024 09:22
Next:how to sand 3d prints