Sand Casting Metal An Overview
Sand casting, one of the oldest and most versatile metal casting processes, plays a crucial role in the modern manufacturing industry. This method involves using sand as the primary mold material to shape molten metal into desired components. The adaptability, cost-effectiveness, and ability to produce complex geometries have made sand casting a prevalent choice among engineers and manufacturers.
The Process of Sand Casting
The sand casting process begins with the creation of a mold. Sand, usually mixed with a binding agent (such as clay or resin), is packed around a pattern that represents the desired shape of the final product. The pattern can be made from various materials, including metal, plastic, or wood, and is removed once the sand has set, leaving a cavity in the shape of the desired part.
Once the mold is ready, molten metal is poured into the cavity. The metal used can vary widely, including aluminum, iron, steel, and bronze, depending on the desired properties of the finished product. After the metal cools and solidifies, the mold is broken away, revealing the cast object. This final product can then be machined or processed further to meet specific tolerances and surface finishes.
Advantages of Sand Casting
One of the most significant advantages of sand casting is its versatility. The method can accommodate a wide range of sizes and shapes, from small intricate components to large structural parts. This flexibility allows manufacturers to produce custom designs without the need for expensive tooling costs.
Moreover, sand casting is particularly beneficial for limited production runs. Since creating a sand mold is relatively quick and inexpensive compared to traditional metal forming methods, it enables rapid prototyping and short-run production. This agility is invaluable in industries where the speed of development is critical, such as automotive and aerospace.
Another noteworthy advantage is that sand casting can use a variety of metal alloys
. The ability to work with different materials allows manufacturers to select metals with the properties best suited for their specific applications, whether it be strength, corrosion resistance, or thermal conductivity.sand casting metal
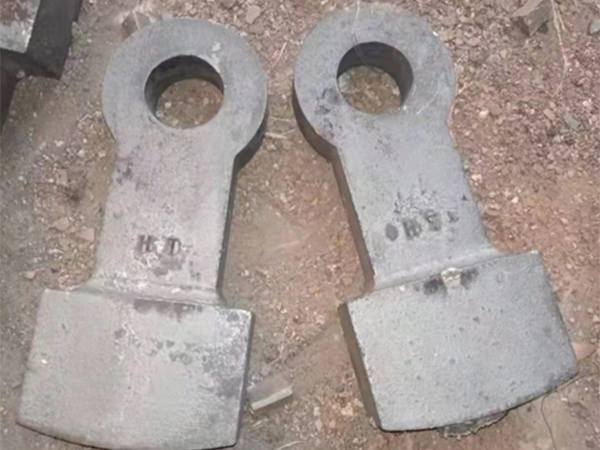
Applications of Sand Casting
Sand casting is utilized across numerous industries, including automotive, aerospace, marine, and machinery production. Components such as engine blocks, transmission cases, and turbine housings are frequently produced using this technique. Its ability to produce complex shapes with high precision makes it suitable for custom parts that require strict tolerances.
Additionally, sand casting is not limited to just industrial applications. It is also employed in making artistic sculptures and ornamental designs, showcasing the method's flexibility in various realms of production.
Challenges and Considerations
Despite its many advantages, sand casting is not without challenges. One of the primary concerns is the surface finish of the cast product, which may require additional machining to achieve a smooth finish. Furthermore, the dimensional accuracy can be a limiting factor, as sand molds can be subject to shrinkage and mold warping during the cooling process.
Another consideration is the environmental impact of sand casting. The use of sand and binding agents can contribute to waste, and the handling of molten metal poses safety risks. Manufacturers are increasingly exploring ways to minimize these impacts, such as implementing recycling programs for used sand and adopting modern technologies to improve safety and efficiency.
Conclusion
In conclusion, sand casting remains a vital and versatile method for metal production. Its ability to create complex shapes economically makes it a favored choice in many industries. As technology advances and industries evolve, sand casting will likely continue to adapt, maintaining its relevance in the ever-changing landscape of manufacturing. The combination of traditional techniques with modern innovations points toward a promising future for sand casting, proving that while the methods may be ancient, their applications are far from outdated.
Post time:dec . 25, 2024 21:41
Next:sand for metal casting