The Difference Between Die Casting and Sand Casting
When it comes to metal casting processes, two commonly discussed techniques are die casting and sand casting. Both methods are widely used in the manufacturing industry, particularly in producing complex shapes and components for various applications. While they share the fundamental concept of shaping molten metal into solid forms, they differ significantly in terms of processes, materials, applications, and advantages. Understanding these differences is crucial for manufacturers and engineers when selecting the appropriate casting method for their projects.
Definition and Process
Die casting is a process that involves forcing molten metal into a steel mold under high pressure. The molds, known as dies, are precision-engineered to create parts with fine details and smooth surfaces. Typically, non-ferrous metals such as aluminum, zinc, and magnesium alloys are used in die casting, owing to their low melting points and excellent fluidity. The process is fast, making it suitable for high-volume production runs. Once the metal cools and solidifies inside the die, the mold is opened to remove the finished part, which may require minimal finishing work.
On the other hand, sand casting is a more traditional method that involves creating a mold from sand, typically mixed with a binder. In this process, a pattern of the desired part is placed in a sand mixture to form the mold cavity. After the pattern is removed, molten metal is poured into the cavity, where it cools and solidifies. This technique can be used for ferrous and non-ferrous metals alike, allowing for greater versatility in material selection. Sand casting is generally slower than die casting and is more suited for lower-volume production runs or custom parts.
Cost
The cost structures of die casting and sand casting vary significantly. Die casting requires a significant initial investment in the design and manufacturing of the dies. These molds are expensive due to their complexity and the materials used. However, once the mold is created, the per-unit cost for high-volume production decreases dramatically, making it economically viable for mass production.
In contrast, sand casting requires a lower upfront investment since the molds can be made relatively quickly with less advanced machinery. The sand used in this process is inexpensive as well. However, the per-unit cost tends to be higher than die casting for large production runs, resulting in sand casting being more suitable for short runs or specialty applications.
difference between die casting and sand casting
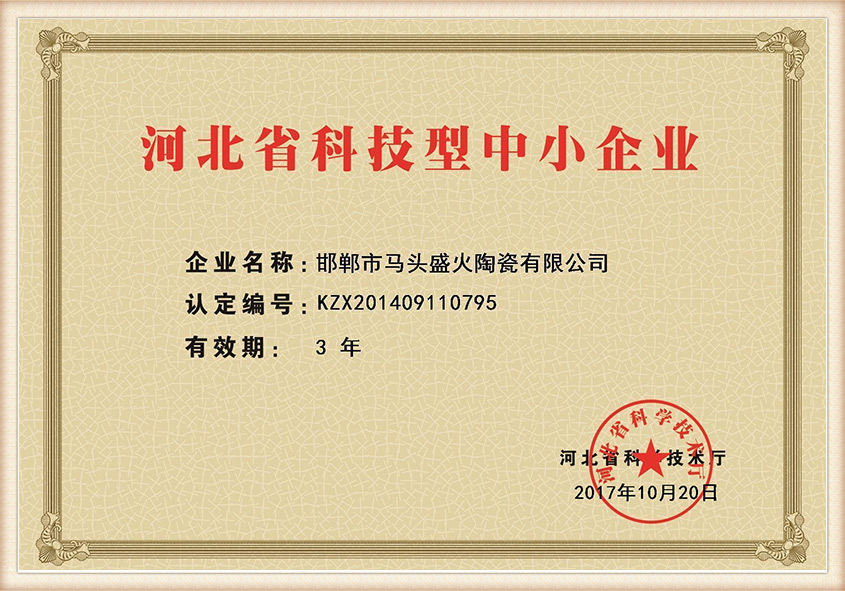
Surface Finish and Tolerances
Die casting typically produces parts with superior surface finishes and tighter tolerances compared to sand casting. The high-pressure injection of molten metal into a precisely machined die results in smoother surfaces, which often require minimal post-processing. This aspect is particularly beneficial in industries that demand high precision, such as automotive and aerospace.
In contrast, parts produced via sand casting often exhibit rougher surfaces and the potential for irregularities, which may necessitate additional finishing operations. Sand casting does allow for the casting of larger and more intricate shapes, but the surface quality and dimensional accuracy may not match that of die casting.
Applications
The choice between die casting and sand casting often depends on the specific requirements of the project. Die casting is ideal for producing large quantities of components with consistent quality, such as automotive parts, electronic housings, and appliance components. Its speed and efficiency make it a go-to method for industries looking to mass-produce high-quality parts.
Conversely, sand casting is favored for creating larger, more complex parts, such as engine blocks, pipes, and architectural fixtures. This method is particularly useful in industries where lower volumes of customized parts are needed or where cost constraints limit investment in expensive dies.
Conclusion
In summary, both die casting and sand casting have unique advantages and are suited for different types of applications. Die casting offers high precision, excellent surface finish, and cost efficiency for large volumes, making it ideal for mass production. In contrast, sand casting provides flexibility, lower initial costs, and the ability to produce larger parts, making it suitable for smaller production runs and complex designs. Ultimately, the choice of casting method will depend on the specific requirements of the project, including material, complexity, volume, and budget considerations. Understanding these differences is essential for ensuring the successful production of quality metal components.
Post time:dec . 03, 2024 18:53
Next:sand casting mass production