Types of Sand Used in Foundry An Overview
In the foundry industry, sand plays a crucial role in the casting process, serving as the primary mold-making material. Different types of sand are utilized based on their properties, which directly impact the quality of the cast products. This article will explore the various types of sand used in foundries, their characteristics, and their applications.
1. Silica Sand
Silica sand is the most commonly used sand in foundries. Composed mainly of silicon dioxide (SiO2), silica sand offers a high melting point and excellent thermal conductivity, making it ideal for casting processes. Its granular structure creates a durable mold that can withstand the immense pressures of molten metal. Silica sand is often employed in the production of ferrous and non-ferrous metal castings. However, it does have a tendency to become less effective at high temperatures, necessitating the use of other materials in some scenarios.
2. Green Sand
Green sand, a mixture of silica sand, clay, and water, is another popular choice among foundries. The clay acts as a binding agent, providing strength and plasticity to the mold. When the mixture is dampened, it can be shaped easily, allowing for intricate mold designs. The term green refers not to the color but to the moisture content, meaning that the sand is used in its natural state without any pre-heating. Green sand molds are often used for casting iron, aluminum, and bronze, making them versatile in the foundry industry.
Resin-coated sand is a synthetic alternative to traditional sand types. In this process, a mixture of sand and phenolic resin is used to produce molds that offer high dimensional accuracy and surface finish. The resin hardens upon heating, creating a strong mold that can withstand high temperatures. This type of sand results in less casting defects, reducing the need for further post-casting processes. It is commonly used for high-performance applications in the aerospace and automotive industries due to its durability and finish.
types of sand used in foundry
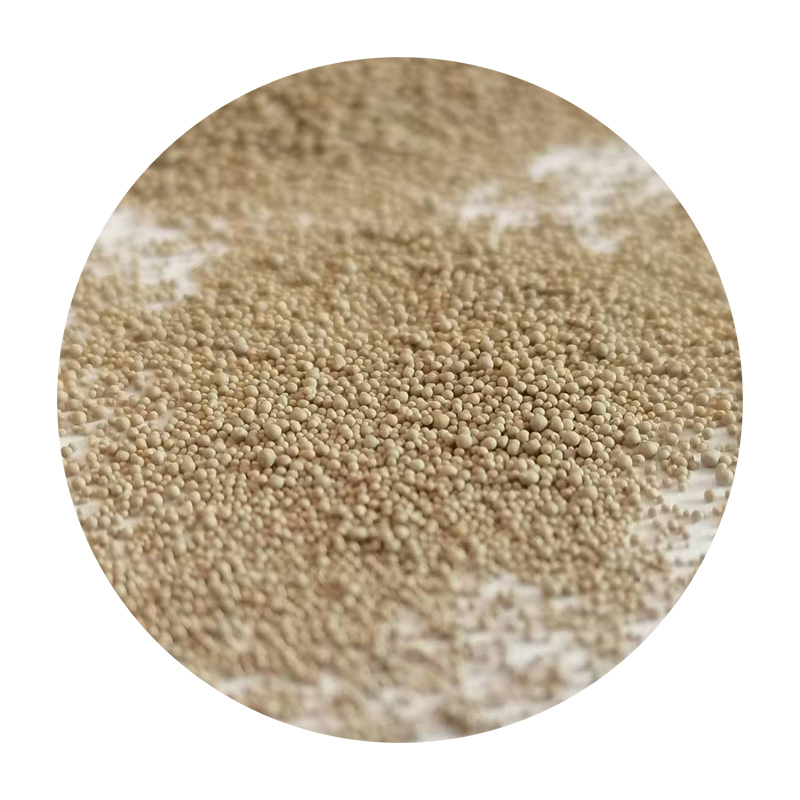
4. Chromite Sand
Chromite sand, derived from chromite ore, is known for its excellent thermal stability and high refractoriness. It is ideal for producing molds for casting steel and iron. Chromite sand is highly resistant to thermal shock, which makes it suitable for more complex geometries and applications that require a high level of precision. However, it is a more expensive option compared to traditional silica sand, limiting its usage primarily to specialized casting processes.
5. Zircon Sand
Zircon sand is another high-performance option used in foundries, particularly for casting applications where high resistance to thermal shock is necessary. This type of sand has a very high melting point and is chemically inert, which makes it an excellent choice for both ferrous and non-ferrous metal casting. Zircon sand provides a fine surface finish and reduces the occurrence of casting defects such as veining and rust, making it ideal for industries requiring precision castings.
6. Carbon Sand
Carbon sand is an innovative material that incorporates carbon particles with traditional sand grains. It is primarily used in applications that require superior thermal conductivity and minimal oxidation of molten metals. Carbon sand is particularly beneficial for casting steel and other alloys where heat retention is critical. The addition of carbon also helps improve the surface quality of the cast product.
Conclusion
The selection of sand in the foundry process is vital in achieving the desired quality of castings. Each type of sand offers unique properties that cater to specific casting requirements. Whether it is the versatility of green sand, the precision of resin-coated sand, or the stability of chromite and zircon sands, understanding these distinctions is essential for foundry engineers and operators. As technology advances and the demands for higher-quality cast products increase, the development and application of different sand types will continue to evolve in the foundry industry.
Post time:ডিসে. . 15, 2024 02:36
Next:proseso ng paghahagis ng buhangin ng foundry