Types of Sand Used in Foundry
In the foundry industry, sand plays a crucial role as the primary molding material for casting metals. The characteristics of sand can significantly affect the quality of the cast products, making it essential to select the right type for specific applications. This article explores the different types of sand used in foundries, their properties, and their applications.
1. Green Sand
Green sand is one of the most commonly utilized molding materials in foundries. It is composed of silica sand, clay (typically bentonite), water, and various additives. The term green refers to the moisture content of the sand rather than its color. The notable properties of green sand include excellent moldability, good thermal conductivity, and the ability to create detailed mold patterns. Additionally, green sand can be reused multiple times, making it a cost-effective option for many foundries. Its application is widespread in the production of ferrous and non-ferrous castings.
2. No-Bake Sand
No-bake sand, also known as chemically bonded sand, refers to a molding material that hardens through a chemical reaction. Typically, this sand is mixed with a resin or hardener and does not require moisture to create molds. No-bake processes allow for intricate designs and can produce strong molds that resist distortion during casting. However, this type of sand is more expensive than green sand and is often used for producing high-quality or complex castings where precision is essential.
Lost foam sand casting is a relatively modern process in which a foam pattern is used to create a mold cavity. The foam is coated with a refractory material, and sand is packed around it. When molten metal is poured into the mold, the foam evaporates, leaving behind the desired shape. This technique allows for excellent surface finish and dimensional accuracy, making it ideal for intricate components. However, it requires specialized equipment and expertise, limiting its use primarily to specific applications.
types of sand used in foundry
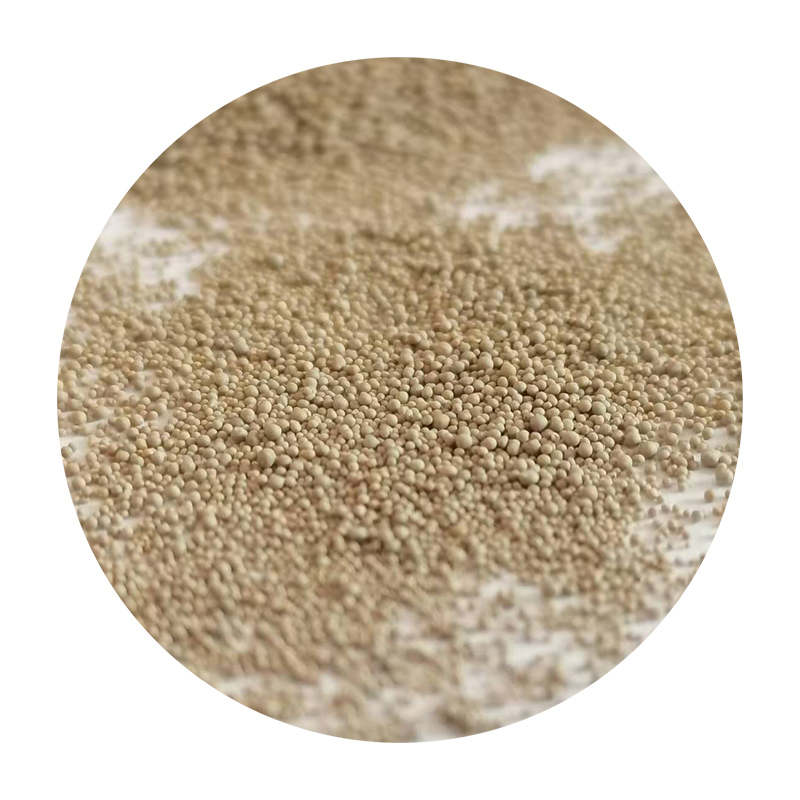
4. Core Sand
Core sand is specifically utilized for making cores, which are internal components used in molds to create hollow sections within castings. Cores can be made from various types of sand, most commonly oil sand, which consists of sand mixed with oil or resins. The use of core sand can significantly enhance the complexity of cast parts and is often employed alongside other molding sands to achieve desired internal geometries.
5. Oil Sand
Oil sand is a type of sand blend that incorporates oil—typically linseed or mineral oil—along with the sand and a binding agent. It is known for its strength and durability and is able to withstand higher temperatures without collapsing, making it suitable for high-performance applications. Oil sand is often used for larger castings and those requiring a high degree of precision.
6. Silica Sand
Silica sand, also known as quartz sand, is a primary component in many foundry sands due to its high melting point and excellent thermal stability. It is resistant to heat and other reagents, making it ideal for casting ferrous metals. Silica sand is used in various foundry processes, and its characteristics (like grain shape and size) can be modified to optimize performance for specific applications.
Conclusion
The choice of sand in foundry processes is determined by several factors, including the type of metal being cast, the complexity of the mold design, and the desired finish of the final product. From green sands for its versatility and cost-effectiveness to no-bake sands for intricate details and high-quality finishes, the selection of the right sand type can make a significant difference in the efficiency and output of a foundry. Understanding the properties and applications of these various sands is essential for anyone involved in the casting industry, as it directly impacts the quality and precision of the finished cast products.
Post time:অক্টো. . 22, 2024 03:39
Next:Exploring the Advantages and Techniques of Lost Foam Metal Casting Process