Understanding the Types of Sand Casting Processes
Sand casting, a widely used manufacturing process, plays a vital role in various industries, from automotive to aerospace. It is a technique that involves creating a mold from sand and then pouring molten metal into it to produce a desired object. The versatility of sand casting lies in its numerous types, each suited for different applications and material types. In this article, we will explore the main types of sand casting processes and their specific characteristics.
1. Green Sand Casting
Green sand casting is the most common and traditional form of sand casting. It utilizes a mixture of sand, clay, and water to create a mold. The term green refers to the moisture content of the sand, not the color. The mold is formed by packing the wet sand around a pattern, which is typically made from metal or wood. After the mold is created, it is dried partially before molten metal is poured in. Green sand casting is favored for its cost-effectiveness and ability to produce complex shapes. However, it does have limitations in terms of dimensional accuracy and surface finish.
2. Dry Sand Casting
Dry sand casting involves the use of sand that has been baked or treated to remove moisture, resulting in a stronger and more rigid mold. This technique improves the surface finish and dimensional accuracy of the final product. Dry sand molds have enhanced durability, allowing for multiple castings with minimal wear. This method is often used for large castings that require a higher level of precision and quality. The drawback is that the initial setup costs can be higher than those for green sand casting.
types of sand casting process
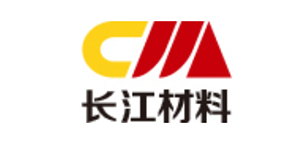
No-bake sand casting, also known as chemically bonded sand casting, uses a mixture of sand and a chemical binder that solidifies when a catalyst is added. Unlike green or dry sand processes, no-bake casting does not require moisture or heating to form the mold. This method allows for quick setup and the production of complex shapes with excellent surface finish. It is particularly useful for producing small to medium-sized parts with intricate designs. However, the cost of the chemical binders can make this process more expensive than traditional sand casting methods.
4. Lost Foam Casting
Lost foam casting is a unique sand casting method that uses a foam pattern instead of a traditional mold. The foam is coated in a sand mixture and then subsequently vaporized when molten metal is poured into the mold, creating a casting that closely matches the pattern. This method offers high precision and is ideal for complex geometries. While lost foam casting provides excellent surface finish and reduced machining time, it typically requires more advanced equipment and a higher level of experience.
5. Investment Sand Casting
Investment sand casting, or shell mold casting, involves creating a thin shell around a pattern made from a more durable material, such as metal. This process improves accuracy and surface finish significantly compared to traditional sand casting methods. The shell is formed by coating the pattern with a mixture of sand and a thermosetting resin. Following the hardening process, the shell is filled with molten metal. This technique is commonly used for producing small, intricate parts that demand higher tolerances.
Conclusion
Sand casting remains one of the most versatile and cost-effective manufacturing methods available. Understanding the different types of sand casting processes allows engineers and manufacturers to choose the best approach based on their specific project requirements. Each method has its unique advantages and challenges, and the choice often depends on factors such as complexity, size, and the material used. By leveraging these options effectively, industries can produce high-quality metal components that meet modern manufacturing standards.
Post time:নভে. . 28, 2024 03:41
Next:Innovative Uses and Techniques of Sand Casting in Modern Manufacturing Processes