Parts of Sand Casting Understanding the Process and Components
Sand casting is one of the oldest and most widely used metal casting processes. This versatile technique allows for the production of intricate parts with high precision and relatively low cost. Understanding the various parts of the sand casting process is crucial for anyone involved in manufacturing, engineering, or metal working. In this article, we'll explore the fundamental components and stages of sand casting.
1. The Molding Process
The molding process is the first and perhaps most critical step in sand casting. It involves creating a mold from sand, which will form the exterior shape of the part being cast. The mold typically consists of two halves the cope (upper half) and the drag (lower half). These two halves are made from a mixture of sand, clay, and water, which allows the mold to hold its shape during the casting process.
The quality of the mold is vital, as it directly impacts the finish and dimensional accuracy of the final part. The sand used in molding is often a high-silica content, which provides excellent thermal stability and ensures that the mold can withstand the molten metal's heat without collapsing.
2. Core Creation
In many designs, especially those requiring internal cavities such as pipes or valves, cores are used. Cores are additional sand structures placed within the mold to create these internal features. They are typically made using a similar sand mixture and must be carefully designed and positioned to ensure they do not collapse during the pouring of the molten metal.
The core needs to be sufficiently strong to withstand the metal’s weight and thermal stress. Once the core is placed inside the mold, both the cope and the drag are assembled to complete the mold structure.
3
. PouringAfter the mold is assembled, the next step is pouring molten metal into the mold cavity. The metal is usually heated to a temperature that exceeds its melting point, transforming it into a liquid state. It is vital to pour the metal at the right temperature and amount to avoid defects such as cold shuts, where the metal solidifies before the mold is completely filled, or gas porosity, which results from trapped air or gases.
parts of sand casting
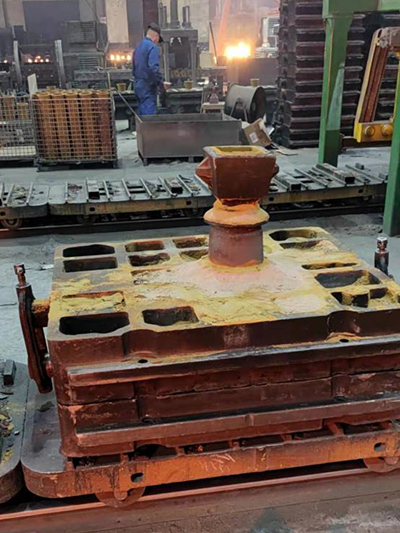
The pouring process must be executed carefully; improper techniques may lead to defects in the final cast part. Various pouring systems, like ladles or automated pouring machines, may be utilized, depending on the size and complexity of the parts being cast.
4. Cooling and Solidification
Once the molten metal has been poured into the mold, it needs to cool and solidify. This phase can take several hours, depending on the size and thickness of the part. During this time, the metal transitions from a liquid to a solid state, taking on the shape of the mold. The cooling rates can affect the mechanical properties of the metal, so controlled cooling is often necessary to achieve desired characteristics.
5. Mold Removal
After the metal has cooled and solidified, the next step is to remove the mold. This process involves breaking apart the cope and drag to extract the cast component. The sand mold can usually be reused for multiple casting cycles, but it may require some maintenance and reconditioning to ensure quality.
6. Finishing Operations
With the cast part removed, it will typically need some finishing operations to prepare it for use. These can include trimming excess material, grinding, sanding, or other machining processes to achieve the required surface finish and dimensional accuracy.
Conclusion
Sand casting is a flexible and cost-effective method for producing a wide range of metal parts. Each stage of the casting process, from mold making to finishing, plays a critical role in determining the quality and performance of the final product. By understanding each part of the sand casting process, manufacturers can optimize their operations, reduce wastage, and improve the overall quality of their cast components. The continued evolution of sand casting technology and practices promises to enhance its effectiveness further, catering to diverse industrial needs.
Post time:ডিসে. . 11, 2024 09:05
Next:fonderia di sabbia