Materials Used for Sand Casting
Sand casting is a versatile and widely utilized manufacturing process that has been in use for centuries. It involves creating a sand mold into which molten metal is poured to form various metal parts and components. The choice of materials used in sand casting significantly influences the quality of the final product, the efficiency of the process, and the overall costs. This article delves into the various materials used in sand casting, including molding sand, core materials, bonding agents, and the types of metals usually cast.
Molding Sand
The primary material in sand casting is molding sand, which is used to form the molds. The best-suited sand for this process is silica sand due to its high melting point, good thermal conductivity, and ability to withstand the pressures of molten metal. Silica sand typically has a grain size between 0.1 mm to 0.5 mm and is chosen for its ability to retain the shape of the mold while also allowing gases to escape during the casting process.
To improve the properties of silica sand, several additives are often mixed in, such as clay. Clay serves as a bonding agent that increases the sand’s ability to hold its shape. Bentonite clay is particularly popular in sand casting due to its plasticity and strength. Other additives may include coal dust and other organic materials that enhance flexibility and promote binding.
Core Materials
In many sand casting applications, cores are required to create internal features within a casting. Cores are typically made from sand mixtures that include a higher percentage of binding agents to ensure they maintain their shape during metal pouring. Common materials used for cores include resin-coated sand, which provides enhanced strength and surface finish. Cores can also be made from other materials, such as metal, for specific applications requiring greater durability.
Resin systems used for core production come in various types, including phenolic and epoxy resins. These offer higher thermal strengths and improved accuracy in the final product. Depending on the desired end-use and characteristics of the casting, the choice between traditional sand cores and resin cores can significantly affect the casting process.
materials used for sand casting
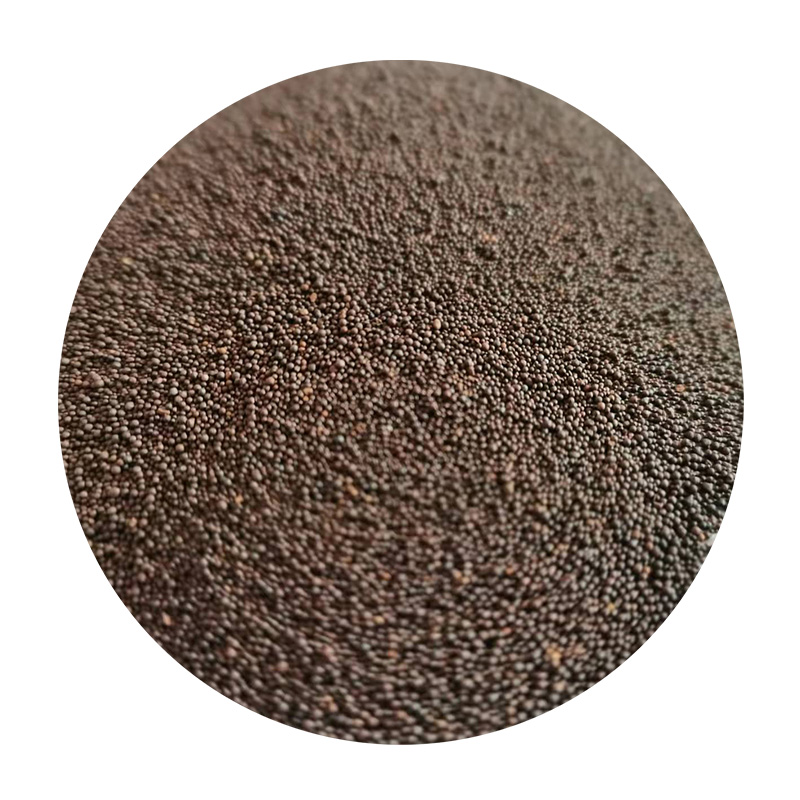
Bonding Agents
Bonding agents play a crucial role in determining the quality of the mold. Beyond clay, several other bonding agents may be employed depending on the specific casting requirements. Chemical binding agents, such as sodium silicate, are often used to create stronger molds that can sustain the heat of the molten metal. These agents react chemically to form a hard, rigid structure after the mold is formed.
Water is another essential component of molding sand. Its percentage is carefully controlled, as it activates the clay and influences the workability of the sand mixture. Too much water can lead to mold erosion and defects in the final casting, while too little can result in poor cohesion and increased breakage.
Metal Alloys
The type of metal used in sand casting is another critical factor. A wide variety of alloys can be cast using sand molding techniques, including ferrous metals like cast iron and steel, as well as non-ferrous metals like aluminum, magnesium, and copper. Each metal has specific properties that may necessitate particular considerations in the sand casting process. For example, aluminum alloys are often cast in sand molds due to their excellent fluidity and ability to fill intricate molds, leading to superior surface finishes.
Conclusion
Understanding the materials used in sand casting is vital for optimizing the casting process and ensuring quality in the final products. The choice of molding sand, core materials, bonding agents, and the metal itself can profoundly impact casting performance, cost, and the mechanical properties of the cast items. As technology continues to advance, the development of new materials and processes in sand casting will further enhance its efficiency and effectiveness in various industrial applications. By leveraging the right combination of materials, manufacturers can produce high-quality metal components that meet demanding specifications across a range of industries.
Post time:সেপ্টে. . 28, 2024 18:07
Next:Innovative Techniques in 3D Printing for Enhanced Sand Casting Processes