Lost Foam Casting Method Revolutionizing Precision Manufacturing
The lost foam casting method is a highly efficient and innovative casting technique that has gained significant traction in various industries, including automotive, aerospace, and industrial machinery. This approach, which combines the advantages of traditional casting with modern technological advancements, has set a new standard for precision and complexity in manufacturing.
What is Lost Foam Casting?
Lost foam casting (LFC) utilizes a foam pattern coated with a refractory material to create complex shapes in metal. The process begins with the creation of a foam pattern, usually made from expanded polystyrene (EPS) or other similar materials. This foam pattern is then coated with a fine layer of sand mixed with a binding agent, creating a shell around it. Once the coating sets, the pattern is heated, causing the foam to evaporate completely, leaving behind a cavity that is then filled with molten metal.
Advantages of Lost Foam Casting
One of the most significant advantages of lost foam casting is its ability to produce highly intricate designs with excellent dimensional accuracy. Because the pattern evaporates rather than being removed, there are no draft angles or cores required, which simplifies the design and reduces tooling costs. This is particularly beneficial in manufacturing components with complex geometries that would be challenging or impossible to achieve using traditional casting methods.
Another key advantage is the reduction in material waste. During conventional casting processes, excess metal is often trimmed away, leading to material loss. In contrast, lost foam casting minimizes this waste by allowing for near-net-shape production. This not only enhances efficiency but also aligns with sustainable manufacturing practices.
Applications of Lost Foam Casting
lost foam casting method
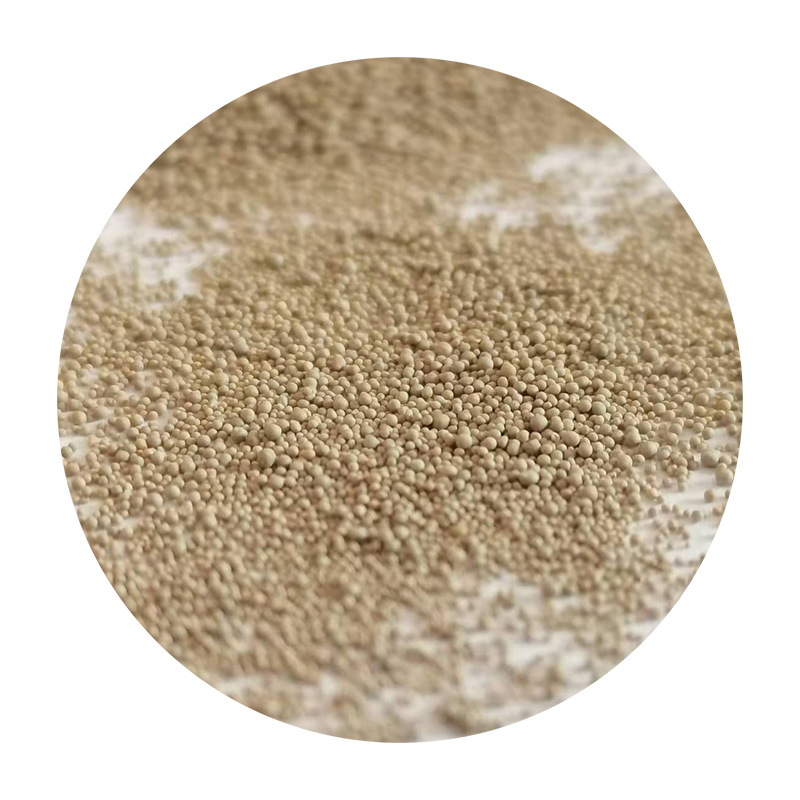
Lost foam casting is widely used in various sectors due to its versatility. In the automotive industry, for instance, manufacturers utilize this technique to create engine components, brackets, and housings that require high strength-to-weight ratios. The aerospace sector also benefits from lost foam casting, especially in the production of complex components that demand precision, such as turbine blades and housing structures.
Additionally, industries involved in heavy machinery often rely on lost foam casting to produce temperature-resistant parts and components that must withstand rigorous operational conditions. The ability to tailor the casting properties by adjusting the alloy composition further enhances the applicability of this method across diverse applications.
Challenges and Considerations
Despite its advantages, lost foam casting is not without challenges. One notable concern is the need for specialized knowledge and technology to properly implement the process. The evaporation of the foam must be controlled to prevent defects in the casted product. Furthermore, the initial investment in equipment and materials can be significant, which may deter smaller manufacturers from adopting this method.
Additionally, the use of expanded polystyrene as a pattern material raises environmental concerns, particularly related to the disposal of foam waste and emissions during the casting process. Manufacturers are increasingly exploring biodegradable alternatives and improved recycling methods to mitigate these issues.
Future of Lost Foam Casting
As industries continue to evolve and demand more complex components with shorter lead times, the lost foam casting method is poised for further growth and development. Advances in 3D printing technology may also complement the lost foam casting process, allowing for rapid prototyping and customized pattern creation, enhancing the overall efficiency and capabilities.
In conclusion, the lost foam casting method represents a significant leap forward in precision manufacturing. With its ability to produce intricate designs, reduce material waste, and enhance design flexibility, it holds the potential to transform various industries. As manufacturers navigate the challenges associated with its implementation and continue to innovate, the future of lost foam casting looks promising, paving the way for a new era of casting technologies.
Post time:অক্টো. . 12, 2024 16:30
Next:resin and sand mix