Understanding Hard Sand Casting A Comprehensive Overview
Hard sand casting, often referred to in industrial contexts as sand casting with added emphasis on its durability and strength, is a widely utilized manufacturing process for producing metal parts. This process is particularly notable for its versatility, allowing for the creation of complex shapes and large components at relatively low costs. In this article, we will delve into the intricacies of hard sand casting, exploring its methodology, advantages, applications, and the future it holds within the manufacturing arena.
The Fundamentals of Hard Sand Casting
At its core, sand casting involves creating a mold from a mixture of sand and a bonding agent. The process begins with forming a pattern, usually made from metal, plastic, or wood, which is a replica of the final product. Once the pattern is created, a mold cavity is formed by packing sand around the pattern to create two halves of a mold. The sand used for hard sand casting is typically a high-quality clay-bonded sand that offers excellent durability, strength, and reusability.
After the mold is prepared, it is subjected to a hardening process, often achieved by adding a resin or chemical hardeners. This is where hard casting comes into play; the hardened mold is much stronger than traditional sand molds, thus able to withstand high pouring temperatures and maintain dimensional accuracy.
The Advantages of Hard Sand Casting
One of the most significant advantages of hard sand casting is its ability to produce intricate designs with high precision. The hardened sand molds allow for finer details, which is essential in industries such as automotive, aerospace, and machinery manufacturing, where components must meet stringent specifications.
Additionally, hard sand casting enables manufacturers to produce large parts in a single piece. This is particularly beneficial in sectors that require large-scale components, such as heavy machinery or engine blocks. The process is also cost-effective, as the materials used in the sand casting are relatively inexpensive compared to other casting methods, and the molds can be reused multiple times.
The process itself is quite adaptable; manufacturers can easily adjust the mixture and the casting techniques to accommodate various metals, including aluminum, iron, brass, and steel. This flexibility makes hard sand casting an attractive option for producing both ferrous and non-ferrous metal components.
hard sand casting
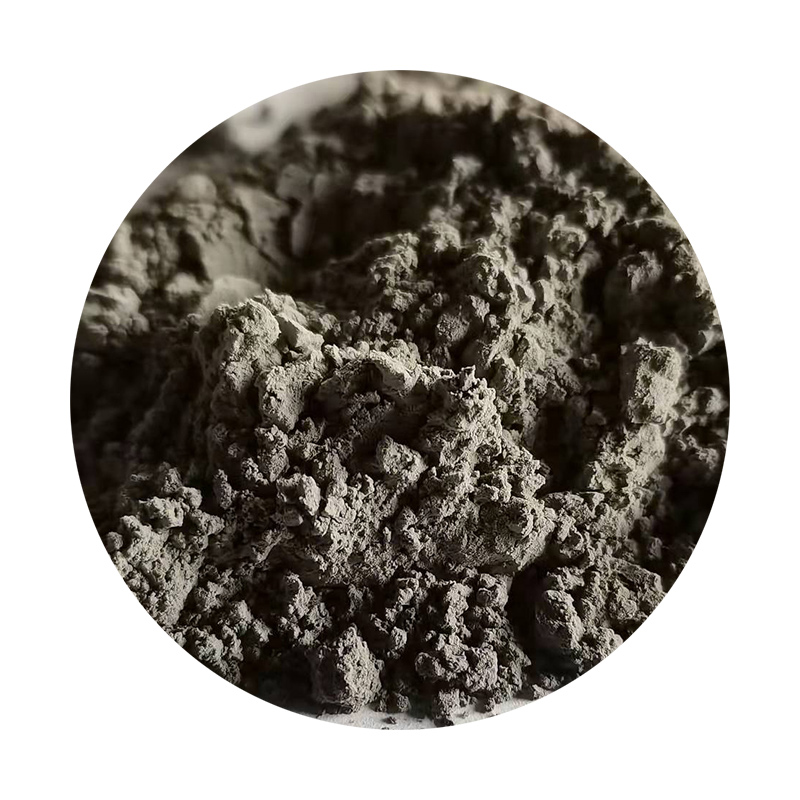
Applications of Hard Sand Casting
The applications of hard sand casting are vast and varied. It is commonly used in the production of automotive engine parts, industrial machinery components, pump housings, and even artistic sculptures. The ability to create complex shapes and robust parts has cemented its position in sectors where reliability and performance are paramount.
For instance, in the automotive industry, hard sand casting can be utilized to manufacture engine blocks and transmission cases that require both structural integrity and thermal stability. In the aerospace sector, where weight and strength are critical, parts produced through hard sand casting are integral to various aircraft systems.
The Future of Hard Sand Casting
As technology advances, the landscape of hard sand casting is also evolving. Automation and computer-aided design (CAD) are increasingly being integrated into the sand casting process. This incorporation not only enhances precision but also streamlines production times, improving overall efficiency. Furthermore, advancements in materials science are leading to the development of new bonding agents and sand mixtures that enhance the strength and durability of the molds used in hard sand casting.
Sustainability is another critical aspect influencing the future of hard sand casting. With growing emphasis on eco-friendly manufacturing practices, researchers are exploring ways to use recycled materials in sand casting processes. This shift could significantly reduce waste and energy consumption in the production of cast parts.
Conclusion
Hard sand casting is a robust and versatile manufacturing method that has stood the test of time, demonstrating its capability to produce complex and durable components across various industries. As technological innovation continues to reshape this traditional process, the future of hard sand casting appears bright, filled with opportunities for increased efficiency, sustainability, and creativity in manufacturing. As industries evolve and new challenges arise, hard sand casting will undoubtedly continue to play a vital role in meeting the demands of modern engineering and design.
Post time:ডিসে. . 25, 2024 22:43
Next:Furan Resin in Sand Casting Applications and Advantages for Foundry Processes