The Impact of Casting Sand Prices on the Foundry Industry
Casting sand, often referred to as foundry sand, plays a pivotal role in the metal casting process, providing the essential medium in which molten metal is poured to create intricate metal components. The pricing of casting sand is influenced by various factors, from raw material availability to market demand, and fluctuations in these prices can have significant ramifications for foundries and the industries they serve.
Understanding Casting Sand
Casting sand typically consists of silica, which offers the key attributes necessary for molding and casting processes. On the surface, it may seem simplistic, but the quality and type of sand can vary, leading to different pricing structures. Some foundries use silica sand, while others may require specialized sands such as resin-coated sand or zircon sand, each with unique properties that cater to specific casting processes.
Factors Influencing Casting Sand Prices
1. Raw Material Availability The supply chain dynamics for natural resources like silica sand directly impact prices. Locations where high-quality silica is abundant generally experience lower prices, whereas regions facing depletion of resources or strict environmental regulations may see an increase in costs. The extraction and processing of this sand can be subject to regulatory scrutiny, which may further affect production costs.
2. Market Demand The demand for casting sand is tightly linked to the performance of the manufacturing and automotive industries, as they are major consumers of cast metal components. Periods of economic growth typically lead to increased demand for casting, thereby raising casting sand prices. Conversely, during economic downturns, a decrease in manufacturing activity can result in lower sand prices due to reduced demand.
casting sand price
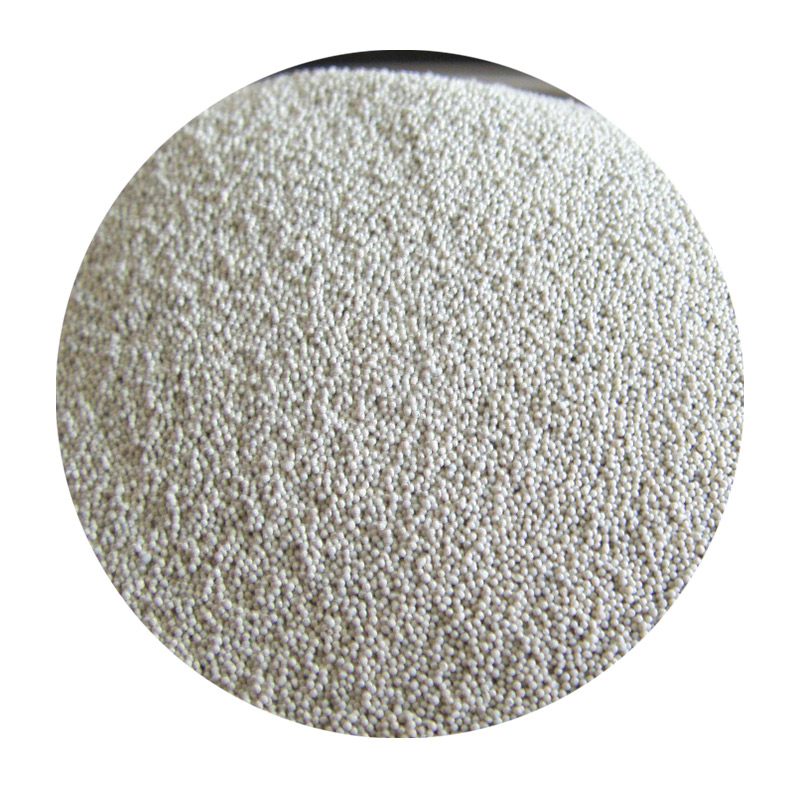
3. Transportation Costs Transportation plays a crucial role in the pricing structure of casting sand. Foundries often source sand from remote locations, meaning that shipping costs can significantly alter end prices. Increases in fuel prices or changes in transportation regulations can lead to higher prices for casting sand, exacerbating costs for foundries already facing tight margins.
4. Technological Advancements The introduction of advanced technologies in the production of casting sand has led to new types of sands and processes that improve casting quality and reduce waste. While these innovations can initially be costly, they may lead to long-term savings and efficiencies in casting operations, potentially offsetting rising prices.
Consequences of Rising Casting Sand Prices
When casting sand prices rise, foundries are faced with tough decisions. The immediate effect is an increase in production costs, which may lead foundries to pass these costs onto their customers in the form of higher prices for casted products. This chain reaction can make their products less competitive, especially in a global market where price sensitivity is high.
Moreover, increased costs can strain relationships with clients if foundries are unable to maintain quality while managing expenses. Some foundries may respond by exploring alternative materials or methods, which could impact the overall quality and reliability of their cast products. This adaptation period may also require investment in new technology or training, adding to the financial burden.
Conclusion
The prices of casting sand are influenced by a multitude of factors that reflect broader market dynamics. For foundries, these prices wield significant influence over operational decisions, economic viability, and competitive positioning within the industry. As global demand for cast metal components continues to rise, remaining cognizant of the factors influencing casting sand prices will be crucial for foundries aiming to thrive in a challenging yet opportunistic market. The balance between managing costs, maintaining quality, and fulfilling market demands will ultimately determine the future landscape of the foundry industry.
Post time:ডিসে. . 05, 2024 00:50
Next:Tips for Sanding Small 3D Prints for a Smooth Finish