Advantages of Sand Casting
Sand casting, also known as sand mold casting, is one of the oldest and most widely used metal casting processes. It involves creating a mold from sand and then pouring molten metal into that mold to produce a desired shape. Despite the emergence of advanced casting techniques, sand casting remains popular due to its distinct advantages. This article explores some of the key benefits of sand casting that make it a preferred choice for many manufacturers.
1. Cost-Effectiveness
One of the primary advantages of sand casting is its cost-effectiveness. The materials used in sand casting, such as sand and binders, are relatively inexpensive and readily available. This makes it an economically viable option for small to large-scale production runs. Additionally, the equipment needed for sand casting is less complex than that required for other casting methods, leading to lower initial setup costs.
2. Flexibility in Design
Sand casting offers significant design flexibility. It can accommodate a variety of part sizes and shapes, ranging from small components to large industrial parts. The process allows for intricate designs, which can be achieved without the need for expensive tooling. This flexibility enables designers and engineers to experiment with prototypes and refine their designs, ultimately leading to innovative products.
3. Wide Material Range
Another advantage of sand casting is the ability to use a wide range of metals and alloys. From ferrous materials like cast iron and steel to non-ferrous metals such as aluminum, copper, and magnesium, sand casting can cater to various material requirements. This versatility allows manufacturers to select the most suitable material for their specific application, enhancing the overall performance of the final product.
advantages of sand casting
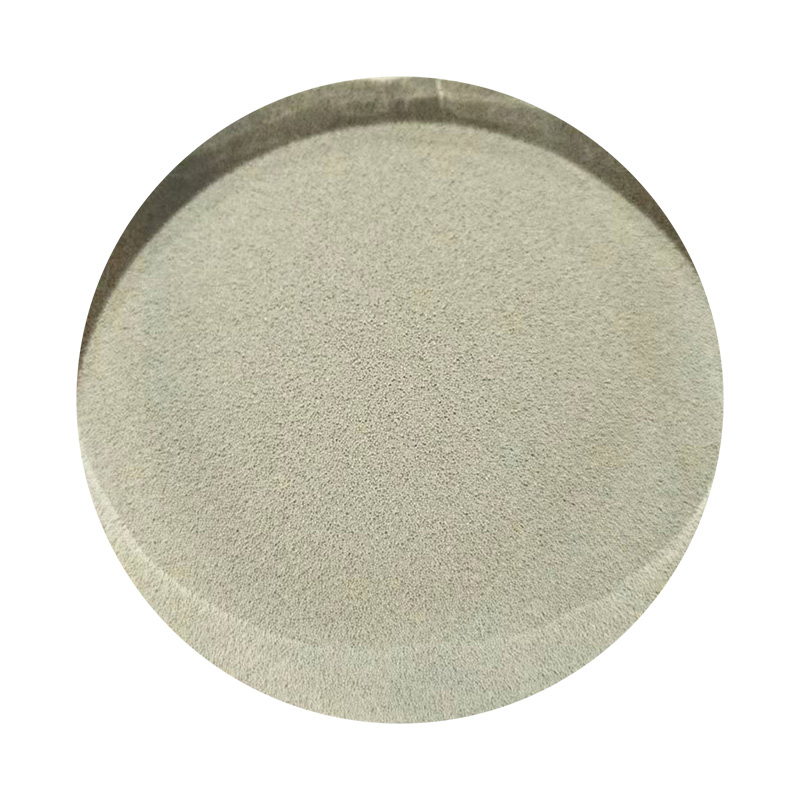
4. Excellent Surface Finish
While sand casting may not always deliver the same surface finish as other processes, it can achieve a satisfactory level of detail and smoothness. The surface finish of sand-cast components can be further improved through post-casting treatments such as polishing or machining. This adaptability allows manufacturers to meet aesthetic and functional requirements, making sand casting suitable for a vast array of applications.
5. High Tolerance Levels
Modern advancements in sand casting have improved its capability to achieve high tolerance levels. With the use of advanced sand molds, manufacturers can produce parts that meet stringent tolerance specifications. This precision makes sand casting suitable for industries that require high-quality components, such as automotive and aerospace.
6. Environmentally Friendly
Lastly, sand casting can be considered an environmentally friendly manufacturing process. The sand used in the molds can often be reused multiple times, reducing waste and minimizing the demand for new materials. Furthermore, since the process does not generate significant hazardous waste, it aligns well with the growing emphasis on sustainable manufacturing practices.
In conclusion, sand casting offers a range of advantages that make it a favored choice among manufacturers. Its cost-effectiveness, design flexibility, material versatility, ability to achieve decent surface finishes, high tolerance capabilities, and environmentally friendly nature contribute to its enduring popularity. As industries continue to evolve, sand casting will undoubtedly remain a crucial manufacturing process, providing solutions for a variety of metal casting needs.
Post time:নভে. . 14, 2024 10:06
Next:wet sanding resin