Advantages and Disadvantages of the Sand Casting Process
Sand casting is one of the oldest and most widely used metal casting processes in the manufacturing industry. It involves creating a mold from sand, into which molten metal is poured to create a desired shape. While sand casting offers a range of benefits, it also comes with its set of disadvantages. Understanding both sides is essential for manufacturers to make informed decisions about the casting process that best suits their needs.
Advantages of Sand Casting
1. Cost-Effectiveness One of the primary advantages of sand casting is its cost-effectiveness, particularly for small to medium production runs. The materials used, primarily sand and binders, are relatively inexpensive compared to other casting methods. Furthermore, the sand casting process does not require expensive molds, which can significantly reduce production costs.
2. Flexibility in Design Sand casting allows for a high degree of flexibility in terms of design complexity. It can easily accommodate intricate shapes and large components. This makes it particularly useful for producing one-off items or prototypes where design modifications may be necessary.
3. Large Size Capability The sand casting process can support the creation of large components that are often challenging to produce using other methods. As the molds can be built up in layers, there is virtually no size limitation, making it an ideal choice for industries such as construction and automotive.
4. Material Versatility Sand casting can be used for a wide variety of metals, including aluminum, bronze, iron, and steel, making it a versatile choice for different applications. This versatility allows manufacturers to choose materials based on their particular properties, such as strength, weight, or corrosion resistance.
5. Simplicity of Process The sand casting process is relatively straightforward and can be performed with minimal training. This simplicity makes it accessible to smaller shops and facilitates quicker production times. Additionally, the equipment required for sand casting is often less complex than that of other casting processes.
advantages and disadvantages of sand casting process
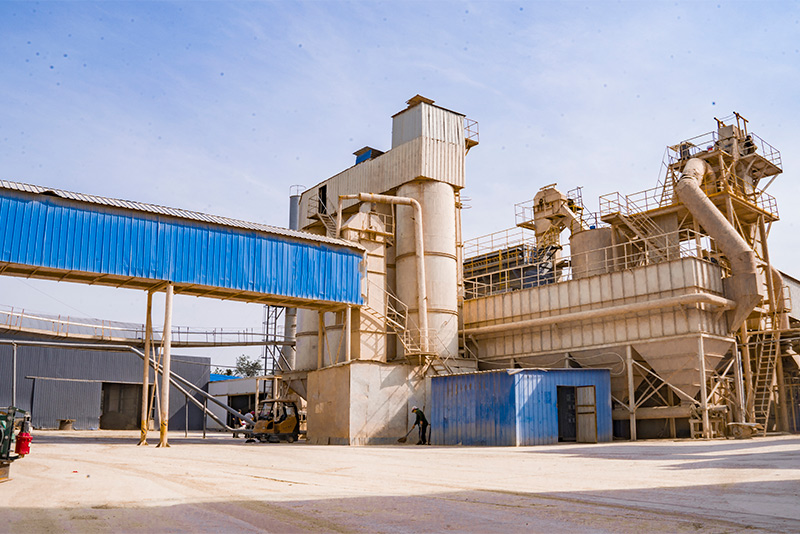
Disadvantages of Sand Casting
1. Surface Finish Quality One of the significant drawbacks of sand casting is that it often produces a rough surface finish compared to other casting methods. While some applications may tolerate this, others, particularly those requiring tight tolerances or high aesthetic quality, may need additional machining and finishing, leading to increased production time and costs.
2. Dimensional Tolerances Sand casting generally offers less precision in dimensions than other methods like investment casting or die casting. The variability in the sand properties, moisture content, and the mixing process can lead to inconsistencies in mold dimensions and, consequently, the final product.
3. Labor-Intensive Process While the basic sand casting process is simple, it can be labor-intensive. The manual steps involved in preparing molds, pouring metal, and cleaning up after casting can slow down production and increase labor costs, particularly for larger-scale operations.
4. Environmental Concerns The sand casting process can have environmental implications. The sand used in the molds must be disposed of or reused after casting, which can create waste management issues. Additionally, the use of resins and binders can contribute to air and ground pollution if not managed properly.
5. Limited Production Rate For large-scale production, sand casting might not be as efficient as other methods. The time taken to prepare molds, allow cooling, and clean the finished product can lead to longer cycle times, making it less suitable for high-volume manufacturing where speed is critical.
Conclusion
The sand casting process remains a fundamental technique in metal manufacturing, offering various advantages such as cost-effectiveness, design flexibility, and material versatility. However, it is essential to weigh these benefits against its disadvantages, including surface finish quality, dimensional tolerances, and environmental concerns. Ultimately, the choice to use sand casting should be based on specific project requirements and production goals, ensuring that manufacturers can leverage its strengths while mitigating potential drawbacks. By making informed decisions, manufacturers can enhance their competitive edge in an increasingly demanding market.
Post time:নভে. . 14, 2024 23:23
Next:custom sand casting