Materials Used for Sand Casting
Sand casting is a widely utilized metal casting process that involves pouring molten metal into a mold created from sand. This method has been in use for centuries, primarily due to its flexibility, cost-effectiveness, and ability to produce complex shapes. The materials used in sand casting play a crucial role in determining the quality and integrity of the final product. Below, we will explore the primary materials involved in sand casting, including sand, binders, and additives.
1. Sand
The primary material in sand casting is, unsurprisingly, sand itself. The type of sand used is critical to the success of the casting process. The most commonly used sand is silica sand, largely due to its high melting point and availability. Silica sand, composed primarily of silicon dioxide (SiO2), can withstand high temperatures, making it suitable for casting metals.
In addition to silica, there are also other types of sand that can be utilized. For example, olivine sand, which is composed mainly of magnesium iron silicate, has excellent thermal stability and is less abrasive than silica. Its resistance to sticking to molten metal makes it a preferred choice for certain applications where higher precision is essential.
Another important factor in the choice of sand is its grain size. The sand should be coarse enough to allow for sufficient drainage of molten metal but fine enough to produce a smooth surface finish on the casting. A mix of sand grains of different sizes is often used to achieve the best results.
2. Binders
what materials are used for sand casting
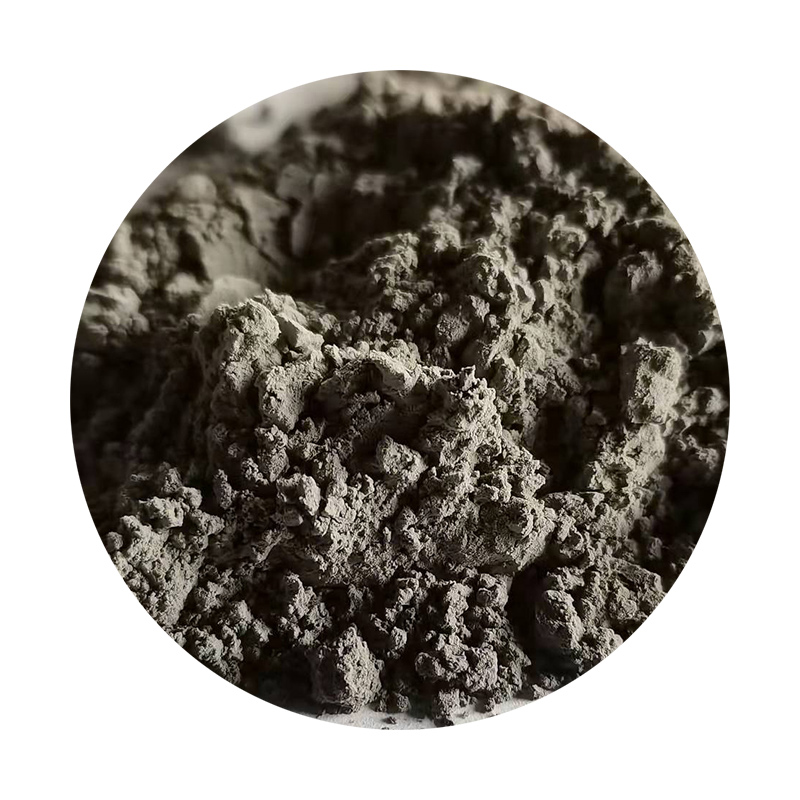
To maintain the shape of the mold and to ensure that the sand grains adhere together, binders are added to the sand mixture. The most common types of binders used in sand casting are clay and resin. Clay is often added in the form of sodium bentonite, which helps to increase the cohesion of the sand particles, providing strength to the mold.
Synthetic resin binders are also popular, especially in modern sand casting applications. These resins can be tailored to create molds with specific properties, such as faster curing times or enhanced durability. The use of resin binds can significantly improve the surface finish of castings and reduce the amount of sand required. However, they can be more expensive than traditional clay-based methods.
3. Additives
In addition to sand and binders, various additives can be included in the mixture to enhance the performance of the casting process. One such additive is a release agent, which is applied to the mold to prevent the molten metal from sticking to the mold surface, facilitating easier removal of the finished casting.
Other additives can modify the thermal properties of the sand mixture. For example, some foundries use graphite as an additive to improve the thermal conductivity and enhance the surface finish of the casting. Likewise, other materials can be incorporated to improve the flow characteristics of the sand, helping to fill complicated molds more effectively.
Conclusion
In conclusion, the materials used in sand casting are fundamental to the effectiveness and quality of the casting process. The selection of appropriate sand, binders, and additives can greatly influence the desired properties of the final product, such as strength, surface finish, and dimensional accuracy. As the industry evolves, new materials and technologies continue to emerge, enhancing the capabilities of sand casting and broadening its applications across various sectors. Understanding these materials not only aids in optimizing the casting process but also in producing superior castings that meet the demanding requirements of modern manufacturing.
Post time:окт. . 18, 2024 10:28
Next:Exploring the Role of Sand in the Casting Process and Its Impact on Quality