Understanding Sand Casting in Engineering
Sand casting is one of the oldest and most versatile methods of metal casting used in engineering and manufacturing. This intricate process involves pouring molten metal into a mold made from sand to create various metal components. Its significance in the engineering field cannot be overstated, as it produces complex shapes and sizes that meet varied industrial demands.
The Process of Sand Casting
The sand casting process begins with the creation of a mold. Engineers or technicians prepare a mixture of sand (usually silica), clay, and water, which holds the sand particles together. This mixture is compacted into a two-part mold, typically consisting of a cope (the top half) and a drag (the bottom half).
Once the mold is built, the next step involves creating a cavity that resembles the desired final product. This can be achieved by using a pattern, which is an accurate replica of the object. Patterns can be made from various materials such as metal, plastic, or wood, depending on the production requirements. The pattern is placed in the sand to form the impression, which is later removed to leave a cavity.
After the mold is prepared, the next step is to heat the metal until it reaches a molten state. Common metals used in sand casting include aluminum, iron, and bronze. The molten metal is then poured into the mold through a pouring system, filling the cavity created by the pattern.
Once the metal solidifies, the mold is broken apart to reveal the cast part
. This final step often includes additional finishing processes such as grinding, machining, or polishing to achieve the desired surface quality and tolerance.what is sand casting in engineering
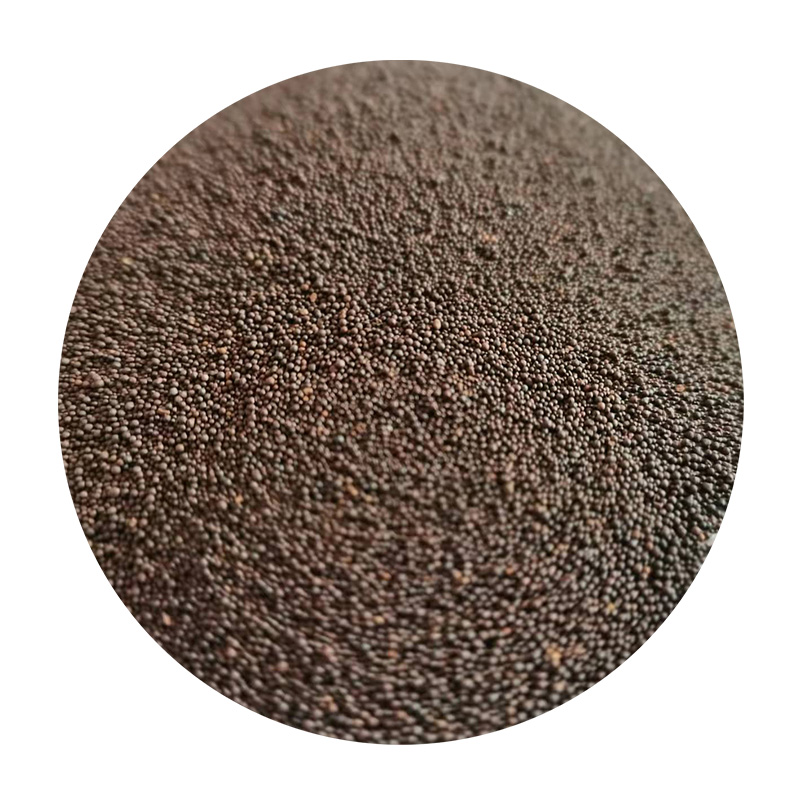
Applications of Sand Casting
Sand casting is widely used in various industries due to its adaptability. It is frequently employed in the automotive sector for producing engine blocks, cylinder heads, and other components. It is also prevalent in the aerospace industry, where high-performance parts are required. Beyond these applications, sand casting is utilized in art and sculpture, producing intricate designs and unique pieces.
Advantages and Disadvantages
One of the primary advantages of sand casting is its cost-effectiveness. The materials required for creating molds are relatively inexpensive, and the process accommodates both low and high production volumes. Additionally, complex shapes can be fabricated that might be challenging to produce using other casting techniques.
However, sand casting is not without its drawbacks. The surface finish may not be as smooth as other methods, and the dimensional precision might vary, especially for intricate designs. Moreover, the sand molds are non-reusable, which may increase material waste.
Conclusion
In summary, sand casting stands as a foundational technique in the realm of engineering and manufacturing. Its ability to create complex shapes from molten metal makes it invaluable across various industries. While it has its limitations, the benefits of cost-effectiveness and versatility continue to enhance its application in modern engineering projects. As the industry evolves, improving technologies and methods will likely refine sand casting processes, ensuring it remains a vital technique for engineers and manufacturers alike.
Post time:сеп. . 06, 2024 16:30
Next:The Sand Cast - Crafting Unique Sand-Based Creations