Achieving Smooth 3D Prints Without Sanding
3D printing has revolutionized the manufacturing landscape, allowing for the creation of highly intricate designs that were once deemed impractical. However, one common challenge faced by 3D printing enthusiasts and professionals alike is achieving a smooth surface finish. Many traditional methods require extensive sanding, which can be both time-consuming and frustrating. Thankfully, advancements in technology and techniques have opened up new possibilities for achieving smooth 3D prints without the need for sanding.
Understanding 3D Printing Textures
The texture of a 3D print can be significantly influenced by several factors the type of printer, the material used, and the slicing settings. The layer height, print speed, and nozzle size are critical parameters that play a substantial role in surface finish. A smaller layer height typically results in a smoother finish since it reduces the visibility of the individual layers. However, lowering the layer height increases printing time, which must be weighed against the desired quality.
Choosing the Right Material
Material selection is fundamental in achieving a smooth surface. Different filament materials offer varying degrees of smoothness when printed. For example, filaments like PLA (Polylactic Acid) are generally easier to work with and can yield smoother surfaces compared to ABS (Acrylonitrile Butadiene Styrene), which can emit fumes and warp more easily. Additionally, using high-quality, well-stored filament can also prevent inconsistencies that result in rough surfaces.
Optimizing Print Settings
Fine-tuning the printer settings can drastically improve the surface quality. Here are some effective strategies
1. Layer Height Using a smaller layer height can help create more refined finishes. While a standard layer height might be 0.2mm, reducing it to 0.1mm or lower can yield significantly smoother surfaces.
smooth 3d prints without sanding
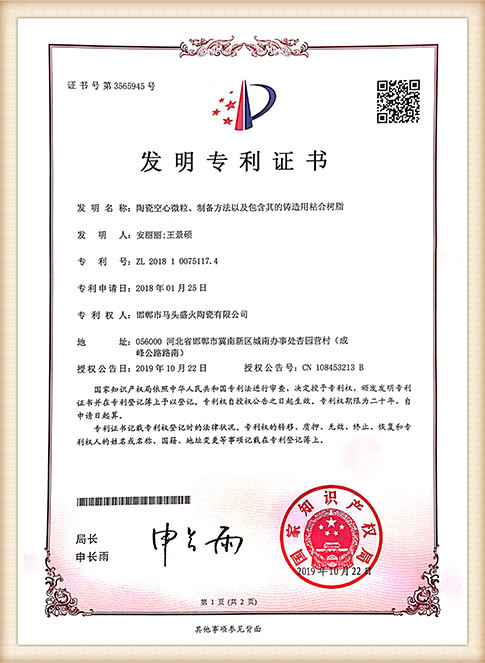
2. Print Speed Slowing down the print speed allows the material more time to settle and bond properly, reducing artifacts that can lead to a rough texture.
3. Nozzle Temperature Ensuring that the nozzle temperature is optimal for the filament type can also play a crucial role in surface quality. If the temperature is too low, the filament may not melt sufficiently, leading to poor layer adhesion and rough finishes.
4. Use of Supports and Rafts Strategically placing supports and rafts can prevent sagging and help maintain the structural integrity of features that would otherwise be prone to roughness.
Post-Processing Techniques
While the goal is to minimize sanding, some post-processing techniques can help achieve an extra level of smoothness without traditional sanding methods. One popular method is the use of vapor smoothing, particularly with ABS prints. A chamber filled with acetone vapor can slightly melt the outer layer of the print, resulting in a much smoother finish. This technique requires careful handling and safety precautions due to the flammability and toxicity of acetone.
Another innovative approach is the application of chemical smoothing agents. There are commercial products available specifically designed for smoothing 3D prints, which can be brushed or sprayed on to fill in layer lines and enhance appearance without the laborious task of sanding.
Conclusion
Achieving smooth 3D prints without sanding is not only possible but increasingly convenient with the right materials, settings, and post-processing techniques. By understanding the fundamental aspects of 3D printing and utilizing modern methods, creators can produce visually stunning and high-quality prints that require minimal finishing. As the technology and methods continue to evolve, we can expect even better solutions for achieving impeccable surfaces in the 3D printing realm.
Post time:ное. . 19, 2024 15:51
Next:Techniques for Finishing Glazed Ceramics Through Sanding and Surface Preparation