The Role of Sand in Sand Casting
Sand casting is one of the oldest and most versatile casting processes used in metalworking. This method involves pouring molten metal into a mold made from sand. The sand used in sand casting has distinct properties that make it an ideal material for creating molds and cores. In this article, we will explore the various types of sand used for sand casting, their properties, and the factors that influence the choice of sand in this manufacturing process.
Types of Sand
The most commonly used type of sand in sand casting is silica sand, which is composed mainly of silicon dioxide (SiO2). Silica sand is favored due to its high melting point, low thermal expansion, and excellent molding properties. In addition to silica sand, there are other types of sand used in casting processes, including zircon sand, chromite sand, and olivine sand. Each of these sands has unique characteristics that may be beneficial depending on the specific requirements of the casting job.
Zircon sand, for instance, is known for its high thermal stability. It resists deformation at high temperatures, making it suitable for casting intricate shapes. Chromite sand, on the other hand, excels in applications where resistance to high temperatures is essential, particularly in steel foundries. Olivine sand has excellent properties for various molding processes because it doesn’t require as much binder, reducing costs while maintaining quality.
Properties of Casting Sand
The effectiveness of sand in casting is dictated by several key properties
1. Grain Size The size of the sand grains affects the mold's ability to capture fine details from the patterns. Finer sands create smoother finishes and better surface resolution, while coarser sands are often used when strength is more important than finish.
2. Mohs Hardness This property measures the hardness of the sand grains. The harder the sand, the better it can withstand the erosive forces of the molten metal. Silica sand typically has a hardness of around 7 on the Mohs scale, making it a suitable choice for most applications.
sand used for sand casting
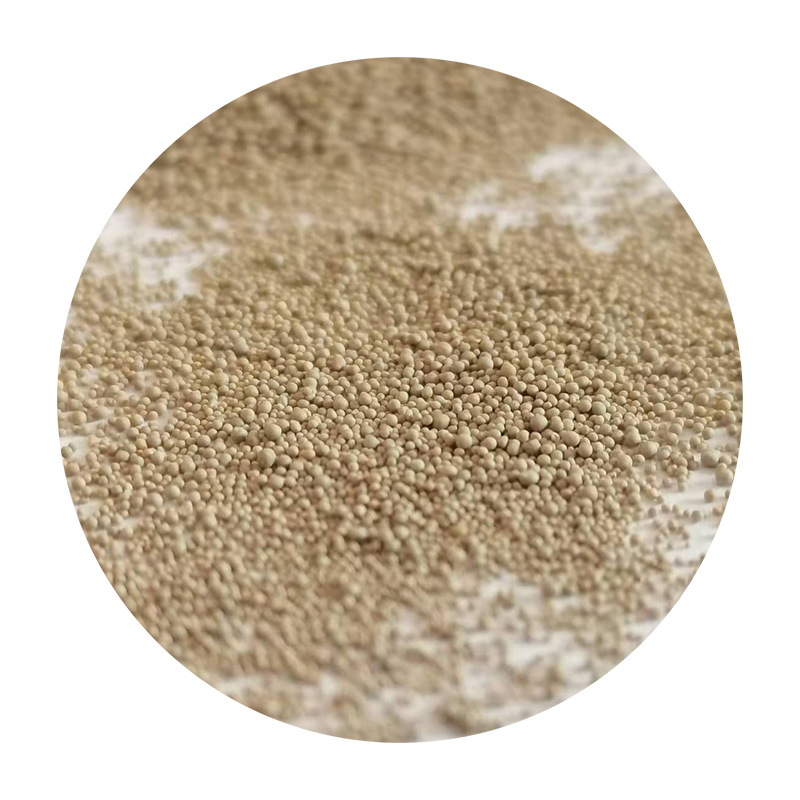
3. Refractoriness This is the ability of sand to resist melting and deformation at high temperatures. Sands used for casting processes need to maintain their structural integrity when exposed to molten metal, hence their composition is critical.
4. Green Strength This refers to the strength of the sand mold before it is heated. A higher green strength allows for better shape retention and minimizes the risk of mold failures during casting.
5. Moisture Content The amount of moisture in the sand affects its bonding properties. The right balance of moisture helps in forming a cohesive mold that can withstand the pouring of molten metal but also should not be too wet, which can lead to gas formation and defects in the casting.
Choosing the Right Sand
Selecting the appropriate sand for a particular casting operation depends on various factors, including the type of metal to be cast, the complexity of the part geometry, and the desired finish quality. Foundries often carry out preliminary tests to determine the most suitable sand type based on the physical and chemical properties required for the specific application.
In practice, while silica sand remains the predominant choice for sand casting, advancements in material science have led to more specialized sands being developed for specific applications. The ongoing research into sand properties and processing techniques continues to enhance the efficiency and quality of sand casting in industries ranging from automotive to aerospace.
Conclusion
In conclusion, sand is a fundamental component of the sand casting process, indispensable due to its unique properties and versatility. Understanding the different types of sand, their characteristics, and their applications is crucial for improving casting quality and efficiency. As technology advances, further improvements in sand casting processes will contribute to the production of higher-quality parts across various industries.
Post time:ное. . 04, 2024 23:16
Next:sanding a 3d print