The Significance of Sand Cast Iron in Modern Manufacturing
Sand cast iron has long been a cornerstone of industrial manufacturing, proving its versatility and robustness across a multitude of applications. The process of sand casting, which dates back to ancient civilizations, involves the use of a mold made from sand to shape molten metal into desired forms. This method is particularly favored for iron casting due to its efficiency, cost-effectiveness, and ability to produce complex shapes.
One of the most notable advantages of sand cast iron is its excellent strength-to-weight ratio. Cast iron, primarily composed of iron, carbon, and silicon, exhibits high tensile strength while remaining relatively lightweight compared to other metals. This makes it an ideal choice for various applications, from machinery components and automotive parts to intricate art pieces. Its durability also means it can withstand high levels of stress and temperature fluctuations, making it particularly suitable for environments such as foundries and heavy machinery.
The manufacturing process of sand cast iron begins with creating a mold. A pattern of the desired object is made, typically from materials such as wood or metal. This pattern is then placed in sand mixed with a binding agent, forming the mold cavity. Once the mold is prepared, molten iron, heated to temperatures exceeding 1,200 degrees Celsius, is poured into the cavity. After sufficient cooling, the sand mold is broken away, revealing the cast iron object within. This process allows for intricate designs and uniform thicknesses, often minimizing the need for further machining.
sand cast iron
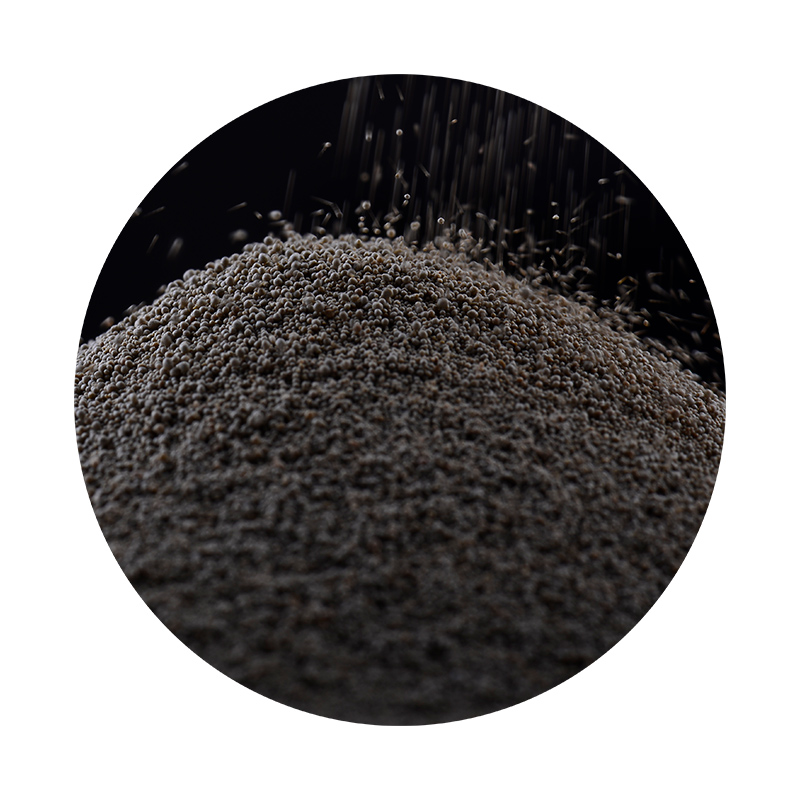
In addition to its mechanical properties, sand cast iron is widely praised for its casting surface finish. The sand used in casting provides a relatively smooth surface, reducing the need for additional polishing. This not only saves time but also helps maintain the integrity of the design. Furthermore, variations in sand composition can yield different finishes and textures, providing manufacturers with the flexibility to achieve specific aesthetic qualities.
Sustainability is becoming increasingly important in manufacturing, and sand cast iron offers several environmentally friendly advantages. The sand used in the casting process can be recycled numerous times, minimizing waste. Additionally, the energy required to melt iron can be reduced through the use of electric induction furnaces, which are more energy-efficient than traditional methods. This focus on sustainability aligns well with modern manufacturing demands for greener practices.
The applications of sand cast iron are extensive. In the automotive industry, it is utilized to produce engine blocks, cylinder heads, and exhaust manifolds due to its ability to endure high temperatures and pressures. In construction, sand cast iron components are found in architectural fixtures, railings, and decorative elements, combining strength with aesthetic appeal. Moreover, the cooking industry has embraced sand cast iron for cookware, such as skillets and Dutch ovens, prized for their heat retention and distribution properties.
In conclusion, sand cast iron remains a vital material in the realm of manufacturing. Its remarkable strength, adaptability, cost-effectiveness, and sustainability continue to make it a preferred choice for industries around the globe. As technology advances, the processes associated with sand cast iron are likely to evolve, further enhancing its role in the future landscape of manufacturing.
Post time:окт. . 30, 2024 22:48
Next:what is sand casting used to make