Sand Casting Manufacturers A Comprehensive Overview
In the realm of manufacturing, sand casting holds a pivotal position as one of the oldest and most versatile techniques for producing metal parts. This method involves creating a mold from sand and then pouring molten metal into the mold cavity. Key to the success of this process are sand casting manufacturers who specialize in producing customized components across various industries. This article delves into the intricacies of sand casting, the role of manufacturers, and recent advancements in this age-old craft.
What is Sand Casting?
Sand casting, also known as sand molded casting, utilizes a sand-based mold to shape molten metal into a desired form. The process begins with creating a pattern, which is a replica of the final product. This pattern is typically made from metal, wood, or plastic and is placed into a mixture of sand and a binding agent, typically clay. The sand is packed around the pattern, and once it’s hardened, the pattern is removed, leaving a cavity in the shape of the part to be cast.
One of the primary advantages of sand casting is its adaptability. It accommodates a wide range of metals, including iron, aluminum, brass, and steel, making it suitable for an extensive array of applications, from automotive parts to art sculptures. Additionally, the sand casting process can produce intricate features and complex geometries, making it ideal for customized parts that would be challenging to produce using other manufacturing methods.
The Role of Sand Casting Manufacturers
Sand casting manufacturers play a crucial role in the lifecycle of a product, from initial design to mass production. Their responsibilities span several key areas
1. Design Consultation Manufacturers often collaborate closely with clients during the design phase. They provide insights into the feasibility of designs, suggest modifications for manufacturability, and optimize designs for performance and cost.
2. Pattern Making The creation of high-quality patterns is essential for achieving precise casting results. Manufacturers use advanced technologies, such as 3D printing, to produce patterns that enhance accuracy and reduce lead times.
sand casting manufacturers
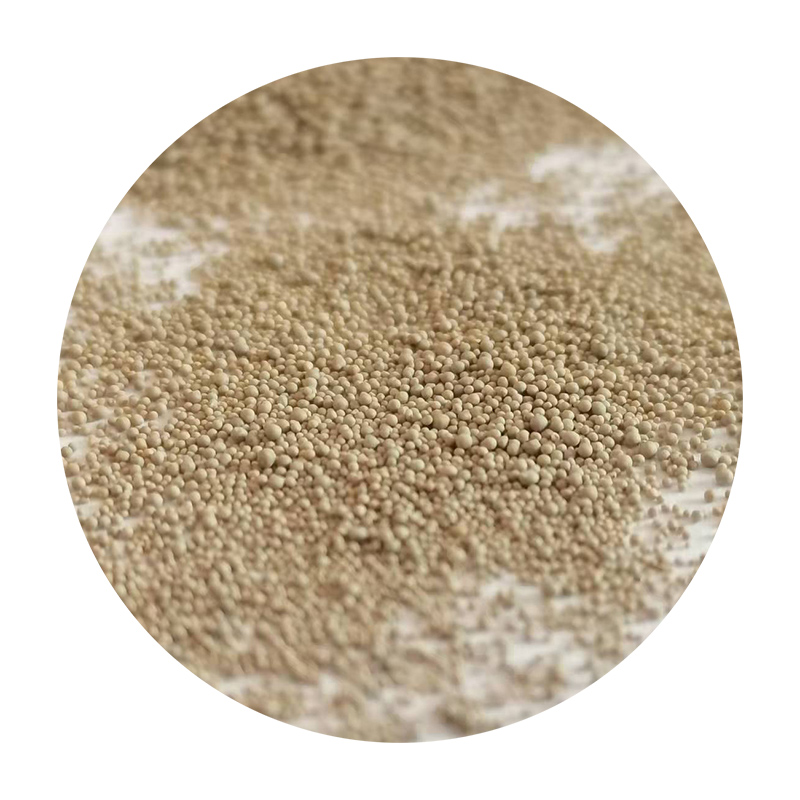
3. Mold Creation Once patterns are ready, manufacturers prepare the sand molds. This involves carefully mixing sand with binders and ensuring that the mold achieves the necessary strength to withstand the molten metal.
4. Metal Pouring and Solidification Skilled technicians manage the melting and pouring of metal into the molds. They monitor temperatures and timing to ensure that the metal fills the mold cavities effectively.
5. Finishing and Quality Control After the metal cools and solidifies, the casting is removed from the mold. Manufacturers often carry out various finishing processes, such as grinding and polishing, to meet the specifications of the final product. Rigorous quality control checks ensure that each component meets industry standards and client expectations.
Advancements in Sand Casting
Recent years have witnessed significant advancements in sand casting technology. Manufacturers are increasingly adopting automation and digital technologies to enhance efficiency and reduce costs. Innovations such as computer-aided design (CAD) and computerized numerical control (CNC) machining allow for more precise patterns and faster production processes.
Moreover, the environmental impact of sand casting is being addressed through improved recycling practices. Manufacturers are now implementing systems to reclaim and reuse sand, significantly reducing waste and conserving resources.
Another noteworthy trend is the rise of 3D printed molds, which allows for rapid prototyping and the ability to create complex shapes that were previously difficult or impossible to achieve with traditional methods.
Conclusion
In summary, sand casting remains a fundamental process in manufacturing, supported by dedicated manufacturers who are committed to quality, innovation, and customer satisfaction. From providing design assistance to implementing cutting-edge technologies, these manufacturers are vital to the successful production of a myriad of metal components. As industries continue to evolve, sand casting manufacturers are poised to adapt, ensuring that this timeless method remains relevant and effective in meeting the demands of modern production. Whether for automotive, aerospace, or art, the impact of sand casting and its manufacturers is undeniable, continuing to shape the way we create and build in a metal-rich world.
Post time:окт. . 22, 2024 07:25
Next:3d sand printer price