Sand Casting Foundry A Cornerstone of Metalworking
Sand casting is one of the oldest and most versatile metalworking processes, dating back thousands of years. The method involves creating a mold from sand, which is then filled with molten metal to form various components. This technique is particularly favored in foundries for its ability to produce intricate shapes and sizes, catering to a myriad of industries, from automotive to aerospace. This article delves into the sand casting process, its advantages, and the role of foundries in modern manufacturing.
The Sand Casting Process
The sand casting process begins with creating a mold. The foundry typically utilizes fine, high-quality sand mixed with a binding agent to ensure the mold holds its shape when the molten metal is poured in. This mixture is compacted around a pattern, which is a replica of the object to be cast. Patterns can be made from various materials, including metal, wood, or plastic, depending on the production volume and complexity of the component.
Once the mold is formed, it is split apart, and the pattern is removed, leaving a cavity that will shape the final product. The next step involves preparing the molten metal, which is heated above its melting point and then carefully poured into the mold cavity. After the metal has cooled and solidified, the mold is broken apart to reveal the cast part.
Advantages of Sand Casting
One of the primary advantages of sand casting is its adaptability. Foundries can produce a wide range of sizes — from small components to large machinery parts, with weights ranging from ounces to several tons. This process is also cost-effective for low to medium production volumes, as the sand molds can be reused multiple times.
Moreover, sand casting allows for complex geometries that would be challenging to achieve with other casting methods. The process is also less restricted by the limits of metal flow, which can sometimes impose constraints in other casting techniques. Furthermore, the use of sand as a mold material provides a great degree of flexibility and ease in adjustments during the design phase.
sand casting foundry
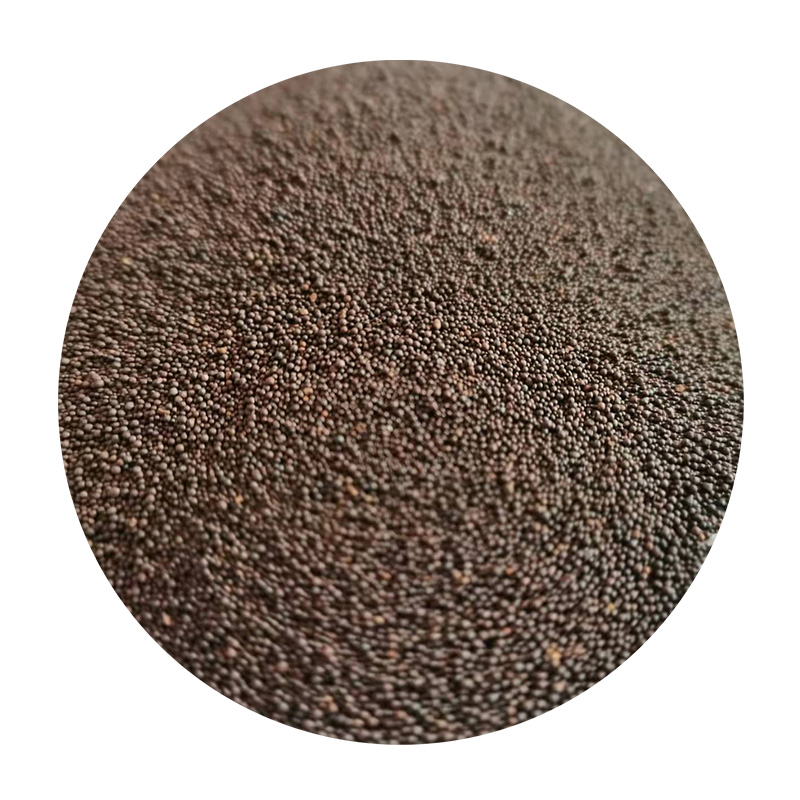
Environmental Considerations
As industrial practices evolve, foundries are increasingly focused on sustainability. Sand casting processes are generally more environmentally friendly compared to other methods, as they produce less waste and utilize recyclable materials. The sand used in molds can be reclaimed and reused, significantly reducing the environmental footprint. Additionally, advancements in technology have improved the efficiency of melting furnaces and reduced emissions, further aligning the industry with green manufacturing principles.
Role of Foundries in Modern Manufacturing
In the modern industrial landscape, foundries play a vital role in fulfilling specific demands across various sectors. They are integral to the supply chain, as many products rely on cast components. The ability of foundries to produce custom solutions makes them invaluable partners in industries such as automotive, construction, and consumer goods.
Moreover, as technology advances, many foundries are adopting computer-aided design (CAD) and computer-aided manufacturing (CAM) systems, allowing for even greater precision and efficiency. The integration of robotics and automation into the sand casting process has streamlined operations, reducing labor costs and improving product consistency.
Conclusion
Sand casting remains a foundational technique within the metalworking industry, offering unmatched flexibility, cost-effectiveness, and the ability to produce complex shapes. Foundries that specialize in sand casting are adapting to modern demands, focusing on sustainability while embracing technological advancements. As industries continue to evolve, the significance of sand casting and the foundries behind this age-old method will undoubtedly endure, shaping the future of manufacturing.
Post time:ное. . 30, 2024 01:31
Next:Tips for Smoothing Small 3D Prints with Sanding Techniques