Sand Casting Alloys An Overview
Sand casting, one of the oldest and most versatile metal casting processes, has stood the test of time due to its adaptability and efficiency in producing complex shapes. The technique is employed across a variety of industries, including automotive, aerospace, and general manufacturing. A crucial aspect of sand casting is the selection of the appropriate alloy, as the properties of the metal significantly influence the quality of the final product. This article explores the various alloys used in sand casting, their characteristics, and the applications they serve.
Understanding Sand Casting
Before diving into the specific alloys, it's important to understand the basic principles of sand casting. The process involves creating a sand mold in which molten metal is poured. Once the metal solidifies, the sand mold is removed to reveal the cast component. The types of molds can vary, but the common denominator is the use of sand as the primary molding material, often mixed with a binder for stability.
Common Alloys Used in Sand Casting
Several alloys are predominantly used in sand casting, each chosen based on the desired characteristics of the end product
1. Cast Iron Cast iron is perhaps the most common material used in sand casting due to its excellent castability and machinability. It has high fluidity and can be cast into intricate shapes with thin sections. Cast iron alloys vary, but grey cast iron and ductile iron (also known as nodular iron) are particularly noteworthy. Grey cast iron is excellent for damping vibrations and is widely used in engine blocks and machinery components, while ductile iron offers enhanced tensile strength and impact resistance, making it ideal for pipes and automotive parts.
2. Aluminum Alloys Aluminum is lightweight, corrosion-resistant, and possesses good thermal conductivity. Sand casting aluminum alloys are often used in the aerospace and automotive industries. Common alloys include 413, 380, and 356, each with unique properties. For instance, 356 aluminum alloy is known for its high strength and superior corrosion resistance, making it ideal for high-stress applications like engine components.
sand casting alloys
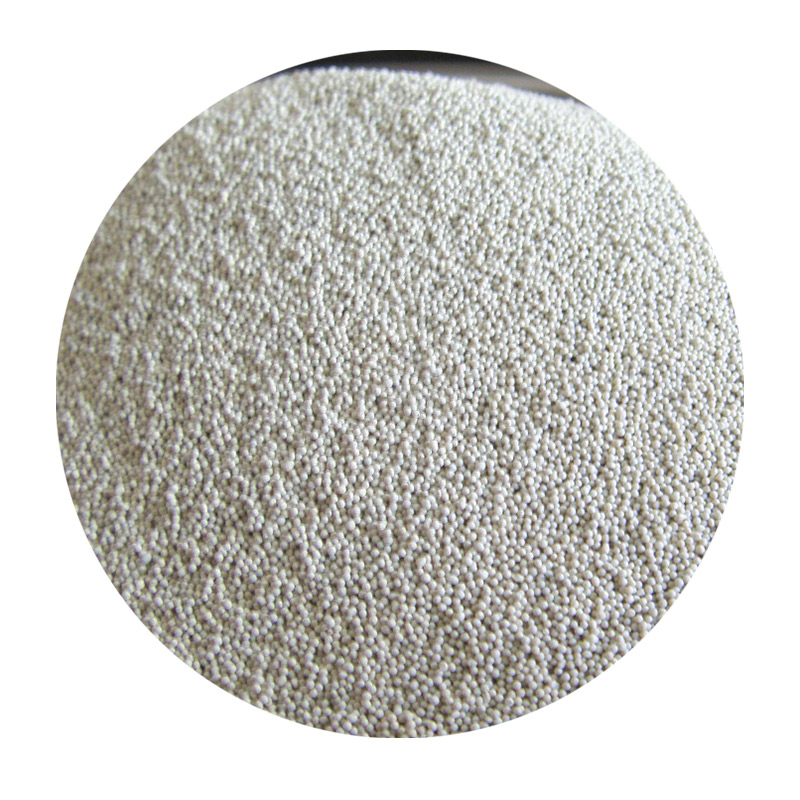
3. Bronze Alloys Bronze, an alloy primarily of copper and tin, exhibits excellent corrosion resistance and high fatigue strength. Sand casting of bronze is frequently used for marine applications, including propellers and shafting, due to its resistance to seawater corrosion. The addition of other elements, such as aluminum or phosphorus, can enhance the properties of bronze for specific applications.
4. Magnesium Alloys Magnesium alloys are gaining popularity in sand casting due to their lightweight and favorable mechanical properties. These alloys are particularly beneficial in industries where reducing weight is critical, such as aerospace. The most commonly used magnesium alloy in sand casting is AZ91, which offers a good balance of strength, ductility, and corrosion resistance.
5. Zinc Alloys Zinc alloys, typically used for their excellent fluidity and ability to fill intricate mold designs, are often used for producing components such as die-cast parts and decorative items. They have a low melting point, facilitating lower energy consumption during the casting process. Zinc-aluminum alloys are particularly popular, known for their good wear resistance and mechanical properties.
Factors Influencing Alloy Selection
Choosing the right alloy for sand casting depends on several factors, including
- Mechanical Properties The required strength, ductility, and hardness of the final product often dictate alloy selection. - Corrosion Resistance In environments prone to rust or chemical corrosion, alloys with higher resistance are preferred. - Casting Complexity The complexity of the shape and the tight tolerances needed can also influence the choice of material. - Cost Economic considerations often play a significant role, requiring a balance between performance and material cost.
Conclusion
In conclusion, sand casting remains a vital method for producing a wide array of components across various industries. The choice of alloy is critical, as it directly affects the mechanical properties, durability, and overall performance of the final product. Whether using cast iron for its robustness, aluminum for its lightweight properties, or specialized alloys for specific applications, understanding the characteristics of different materials is essential for successful sand casting operations. As technology advances and new alloys are developed, the future of sand casting looks promising, continuing to meet the diverse needs of modern manufacturing.
Post time:окт. . 06, 2024 07:36
Next:sand for resin