Parts of Sand Casting An In-Depth Overview
Sand casting, one of the oldest and most versatile manufacturing processes, is a technique used to shape metal into desired forms by creating a mold from sand. Despite the rise of more advanced manufacturing methods, sand casting remains highly relevant today due to its cost-effectiveness and capability to produce complex shapes. Understanding the parts of sand casting is essential for those involved in manufacturing, engineering, or materials science. In this article, we will explore the key components and steps involved in the sand casting process.
1
. PatternThe first step in sand casting is to create a pattern, which is a replica of the final product. Patterns can be made from various materials, including wood, metal, or plastic, and are designed to withstand the sand mold's pressure. The pattern is slightly larger than the final part due to shrinkage that occurs during the cooling process. Patterns can be simple or complex, depending on the design requirements. They can be one-piece or made in multiple parts to facilitate easy removal from the mold.
2. Mold
The mold is a crucial component of the sand casting process and is created by packing sand around the pattern. The sand used is typically a mixture of silica sand, clay, and water, which provides the necessary properties to retain its shape. Molds can be classified as either green sand molds (made from moist sand) or dry sand molds (made from sand that has been dried). The mold cavity formed after removing the pattern serves as the casting shape.
3. Core
In scenarios where the casted part requires internal cavities or complex geometries, cores are utilized. Cores are additional pieces made from sand bonded with a binder, and they are placed in the mold to create these internal features. Cores can be made of the same material as the mold or sometimes from different materials, depending on the design and requirements of the casting. They must be carefully designed to ensure they do not collapse during the pouring of molten metal.
4. Pouring System
parts of sand casting
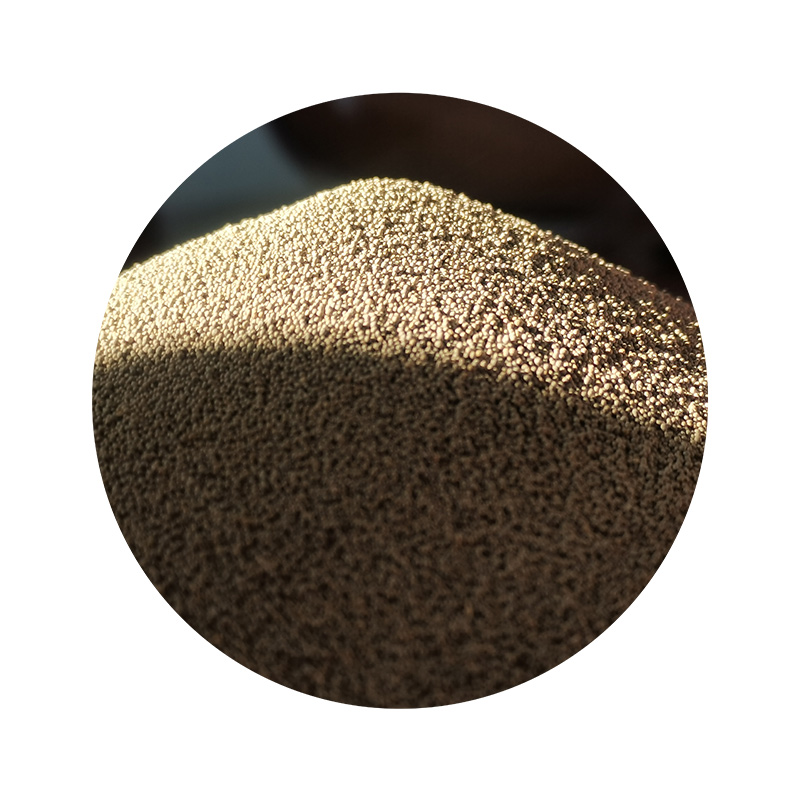
Once the mold and core are prepared, the next step is to establish a pouring system. This system includes the pouring cup, sprue, runner, and gates. The pouring cup is the opening from which the molten metal enters the mold, while the sprue is the vertical channel that leads the metal from the pouring cup into the runner. The runner delivers the molten metal to the gates, which distribute it into the mold cavity. This system must be designed to prevent air traps and ensure a smooth flow of metal to avoid defects.
5. Molten Metal
The type of metal used in sand casting can vary widely, including aluminum, iron, steel, and magnesium alloys. The selection of metal depends on the mechanical properties required of the final product. The molten metal is prepared by melting the raw material in a furnace, and its temperature must be carefully controlled to ensure proper flow and filling of the mold. The properties of the molten metal, such as viscosity and temperature, significantly affect the quality of the finished casting.
6. Cooling and Solidification
After the molten metal is poured into the mold, it must cool and solidify. This process may take several minutes to hours, depending on the size and complexity of the casting. As the metal cools, it shrinks and solidifies, taking the shape of the mold. Once solidified, the casting must be allowed to cool to a manageable temperature before being removed from the mold. This step is essential to prevent damage to both the casting and the mold.
7. Finishing
Finally, after the casting is removed from the mold, it often requires finishing processes such as cleaning, trimming, and machining. This step may include removing excess metal, smoothing surfaces, and applying surface treatments to enhance performance characteristics. Finishing ensures that the final product meets the desired specifications and quality standards.
Conclusion
Sand casting is a time-honored process that plays a vital role in manufacturing a wide array of metal parts. Understanding the various components involved—patterns, molds, cores, pouring systems, molten metals, cooling, and finishing—is essential for effective design and production. Despite newer technologies emerging in the manufacturing sector, the relevance and benefits of sand casting continue to hold strong, thanks to its adaptability and cost-effectiveness. Whether one is designing automotive parts, machinery components, or artistic sculptures, grasping the fundamentals of sand casting can significantly enhance the quality and efficiency of the production process.
Post time:окт. . 10, 2024 11:33
Next:Exploring the Applications and Benefits of Foundry Sand in Manufacturing Industries