Iron Sand Casting A Revolutionary Approach to Metal Casting
Iron sand casting is an innovative method that utilizes iron-rich sand to create intricate metal components. This technique has emerged as a compelling alternative to traditional metal casting methods due to its unique benefits and the advancements in casting technology.
The process begins with the collection of iron sand, which is primarily composed of magnetite or hematite. These forms of iron oxide are abundant in nature and can often be found in coastal regions. Once extracted, the iron sand undergoes a series of preparations to ensure it is suitable for casting. This includes cleaning, drying, and sometimes mixing it with other materials to enhance its properties, such as flowability and bonding strength.
One of the standout features of iron sand casting is its environmental sustainability. Traditional metal casting processes often involve mining and refining metals, which can lead to significant ecological disruption. In contrast, iron sand utilizes a raw material that is more readily available in many parts of the world. Additionally, the energy consumption in extracting and processing iron sand can be lower than that for conventional metallurgical methods, thereby reducing the overall carbon footprint of the casting industry.
The casting process itself typically involves creating a mold from the prepared iron sand. This is done by compacting the sand around a pattern of the desired object, which could be anything from automotive parts to artistic sculptures. Once the mold is formed, molten metal is poured into the cavity, allowing it to take on the shape of the object. After cooling, the mold is broken away, revealing the cast item. The sand can often be reused in the next casting process, making it a cost-effective solution for manufacturers.
iron sand casting
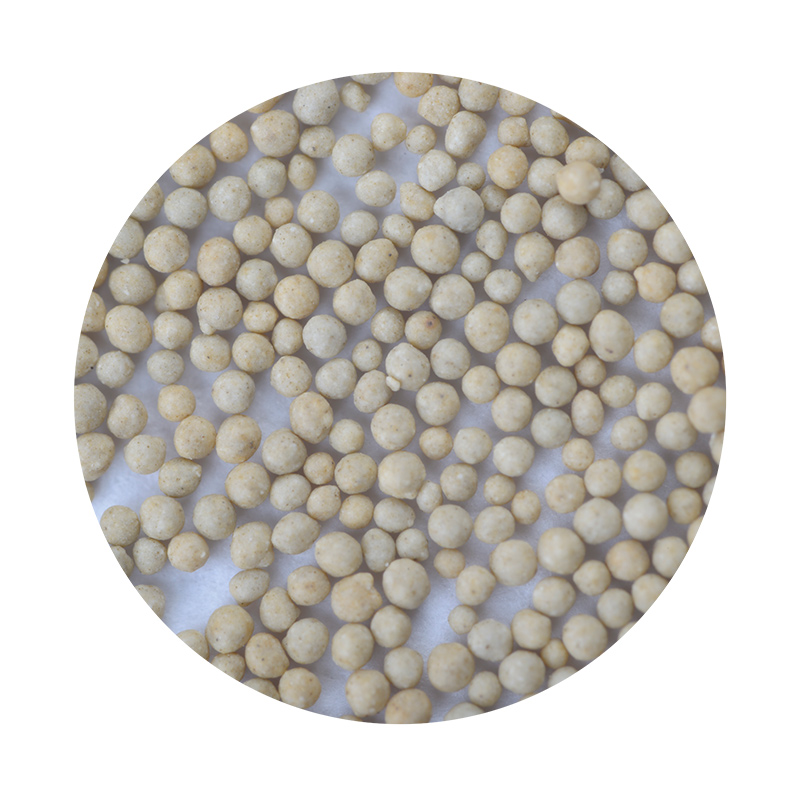
Another significant advantage of iron sand casting is the ability to produce complex shapes and fine details. The fine granularity of iron sand allows for high precision in mold making, which is essential for industries where intricate designs are a necessity. This technique provides manufacturers with the flexibility to create custom parts without the extensive lead times often associated with traditional casting methods.
Moreover, the properties of the materials used in iron sand casting can lead to enhanced strength and durability of the final products. Iron-based materials are known for their excellent mechanical properties, which can be further improved through alloying and post-casting treatments. As a result, components produced through this method can often withstand higher stress and wear compared to those made from lesser quality materials.
As industries continue to evolve towards more sustainable practices, iron sand casting stands out as a viable solution. The combination of environmental benefits, cost-effectiveness, and the ability to produce high-quality components makes it an attractive option for manufacturers worldwide. As technology progresses, we can anticipate further advancements in this field, optimizing the processes and expanding applications in various industries, from automotive to aerospace.
In conclusion, iron sand casting is not just a method but a transformative approach that embodies the future of metal casting. By harnessing natural resources more effectively and sustainably, it illustrates how innovation can lead to improved production techniques that are both economically beneficial and environmentally conscious. As this method gains popularity, it may well redefine standards in the manufacturing sector.
Post time:сеп. . 01, 2024 06:54
Next:best way to sand stainless steel