The Importance of High-Quality Sand Casting in Modern Manufacturing
Sand casting is a well-established manufacturing process that has been used for centuries. It remains one of the most versatile and cost-effective methods for producing complex metal parts. With advancements in technology and increasing demands for precision and quality, the focus on high-quality sand casting has become more critical than ever before. This article explores the vital aspects of high-quality sand casting and its implications for modern manufacturing.
Understanding the Sand Casting Process
Sand casting involves creating a mold from sand, which is then used to shape liquid metal. The process typically begins with the design of a reusable pattern — a replica of the final product — usually made from wood, plastic, or metal. This pattern is placed in a sand mixture, forming a mold cavity once the sand is compacted around it. After removing the pattern, molten metal is poured into the mold to form the desired shape. Once cooled, the sand mold is broken away, leaving the finished casting.
The simplicity of the casting process is one of its many advantages; however, it is the quality of the sand, mold, and overall casting technique that largely determines the accuracy and finish of the final product.
Factors Influencing Sand Casting Quality
1. Sand Quality The type and quality of sand used are paramount. High-quality silica sand is often preferred due to its excellent thermal properties and ability to maintain shape under high temperatures. The addition of binders strengthens the sand mixture, reducing the likelihood of defects such as eroded mold surfaces or poor dimensional accuracy.
2. Moisture Control The moisture content of the sand is critical. Too much water can lead to gas defects due to steam formation, while too little can prevent the sand from binding properly. A balanced moisture level is essential to ensure that the mold maintains its shape and integrity during the casting process.
3. Pattern Design The intricacy of the pattern can affect the final outcome. Complex designs may require specialized patterns that can withstand the rigors of the casting process without deforming. Additionally, incorporating draft angles and fillets can help reduce stress concentrations and enhance the ease of moldmaking and metal flow.
4. Pouring Temperature The temperature at which metal is poured into the mold significantly affects the quality of the casting. The metal should be poured at an optimal temperature to ensure fluidity, which allows it to fill intricate mold features without trapping air. However, excessively high temperatures can lead to oxidation and other defects.
high quality sand casting
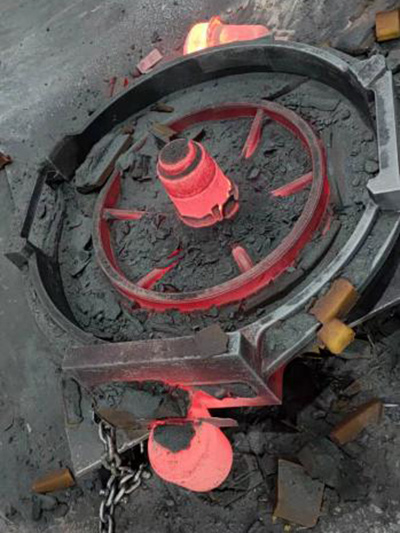
5. Cooling Rate The cooling rate of the casting influences its microstructure and mechanical properties. Controlled cooling is essential to prevent internal stresses and enhance the overall durability of the final product. Implementing techniques such as chills can help manage cooling rates in specific areas of the casting.
Impacts of High-Quality Sand Casting
High-quality sand casting has several profound impacts on manufacturing, particularly in industries such as automotive, aerospace, and heavy machinery. The benefits include
- Enhanced Precision High-quality sand casting allows for tighter tolerances and improved surface finishes, reducing the need for extensive machining and secondary processes.
- Reduction in Waste Investing in quality sand and advanced techniques minimizes defects, which in turn reduces material waste and associated costs. This sustainability aspect is increasingly critical as industries strive to adopt eco-friendly practices.
- Increased Strength and Durability Using superior materials and methods at every stage of production enhances the strength and longevity of the components produced, resulting in safer and more reliable products.
- Flexibility and Customization Sand casting techniques lend themselves well to both small and large production runs, enabling manufacturers to customize components to meet specific client needs without incurring excessive costs.
Conclusion
As industries continue to evolve, the importance of high-quality sand casting cannot be overstated. The capability to produce complex, durable components efficiently positions sand casting as a cornerstone of modern manufacturing. By focusing on factors that influence quality, manufacturers can significantly enhance their output, driving innovation and competitiveness in the global market. Emphasizing high-quality sand casting will not only benefit manufacturers and their clients but also contribute to sustainable and efficient production practices.
Post time:окт. . 16, 2024 05:13
Next:density of foundry sand