Different Types of Foundry Sand
Foundry sand plays a crucial role in the metal casting industry, as it serves as the primary material for creating molds and cores. The choice of sand can significantly influence the quality and characteristics of the final product, as well as the efficiency of the casting process. Here, we explore various types of foundry sand and their unique properties.
1. Silica Sand Silica sand is the most commonly used type of foundry sand, primarily due to its abundance and favorable properties. It consists mainly of silicon dioxide (SiO2) and provides excellent thermal stability, strength, and permeability. Silica sand is ideal for steel and iron castings because it can withstand high temperatures without breaking down. However, silica sand can also pose health risks during handling due to the potential for respiratory issues if dust is inhaled.
Different Types of Foundry Sand
3. Resin-Bonded Sand This type of sand is coated with a synthetic resin that hardens when exposed to heat. Resin-bonded sand offers improved dimensional accuracy and surface finish compared to traditional sand types. It is often used for complex shapes and detailed castings, making it popular in industries requiring high precision, such as aerospace and automotive manufacturing.
different types of foundry sand
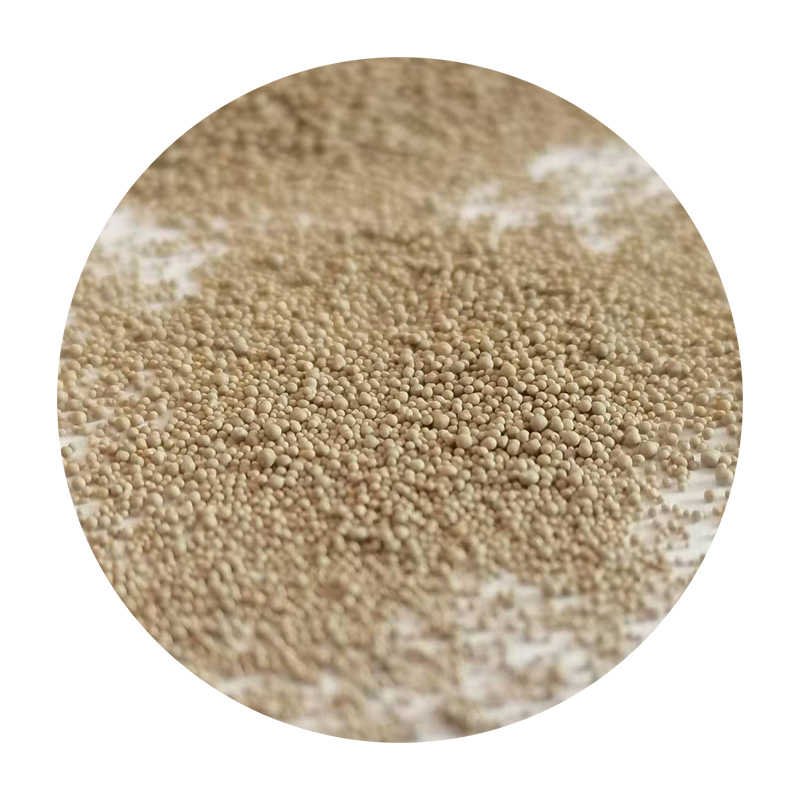
4. Zircon Sand Zircon sand is derived from zirconium silicate and is used for its excellent thermal properties and resistance to metal penetration. It is typically used for casting aluminum and high-temperature alloys, where traditional sands might fail. Although zircon sand is more expensive than other types, its ability to produce high-quality finishes and its reusability make it a favorable choice for specific applications.
5. Chromite Sand Chromite sand is composed of chromium oxide and is known for its high resistance to thermal shock and excellent casting properties. This sand is often used in high-performance applications, such as in steel industries for casting molds and cores that demand exceptional durability. Chromite sand also aids in reducing casting defects and improving the overall quality of the finished product.
6. Olive Sand A lesser-known type of foundry sand, olive sand is derived from olivine, a naturally occurring mineral. It has a high melting point and excellent thermal stability, making it suitable for casting high-temperature metals. Olive sand is also environmentally friendly and reduces the amount of harmful emissions compared to traditional foundry sands.
In conclusion, the various types of foundry sand each possess unique properties that cater to different casting requirements. Foundry engineers must carefully choose the appropriate sand to ensure optimal performance and high-quality castings while considering factors such as cost, environmental impact, and specific application needs.
Post time:сеп. . 05, 2024 06:15
Next:how do you sand resin