The Difference Between Die Casting and Sand Casting
Casting is a fundamental manufacturing process where molten material is poured into a mold to solidify into a desired shape. Among the various casting techniques, die casting and sand casting are two of the most prevalent methods, each possessing unique properties, advantages, and applications. Understanding the differences between these two casting processes is essential for manufacturers when deciding the best method for their specific needs.
Die Casting
Die casting is a high-volume manufacturing process characterized by the use of metal molds, known as dies. These molds are made from durable materials such as steel and can withstand high pressure and temperatures. In die casting, molten metal is forced into the mold cavity under pressure, which allows for the production of complex shapes with tight tolerances and smooth surfaces.
Advantages of Die Casting 1. High Accuracy and Detail Die casting can produce intricate shapes with high dimensional accuracy and minimal post-processing. 2. Excellent Surface Finish The molds used in this method provide a smooth surface finish, reducing the need for additional machining. 3. High Production Rates This process is ideal for mass production, as it allows for rapid cycle times and can produce millions of parts efficiently. 4. Material Efficiency The process minimizes waste as the excess material can often be recycled.
Applications of Die Casting Die casting is commonly used in the automotive, aerospace, and consumer electronics industries. Components such as engine blocks, transmission housings, and intricate parts of electronic devices are often produced using this technique.
Sand Casting
difference between die casting and sand casting
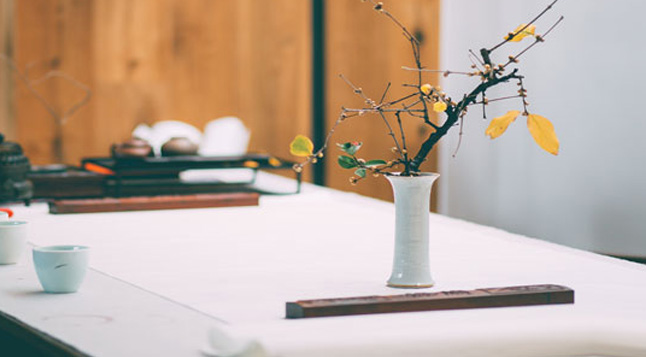
Sand casting, on the other hand, is one of the oldest known casting methods and involves creating a mold from sand. In this process, a pattern (which is a replica of the part to be cast) is covered with sand mixed with a binding agent to create a mold. After forming the mold, the pattern is removed, and molten metal is poured into the cavity left by the pattern. Once the metal cools and solidifies, the mold is broken apart to retrieve the cast product.
Advantages of Sand Casting 1. Versatility Sand casting can accommodate a wide variety of metals and can be used to create large parts, making it highly versatile. 2. Cost-Effective for Low Volume Production The materials (sand, binders) used are inexpensive, making it cost-effective for low to moderate production volumes. 3. Flexibility in Mold Design Sand molds can be easily modified, allowing for unique shapes and sizes to be created without extensive tooling changes.
Applications of Sand Casting Sand casting is commonly used for creating large and heavy components such as engine blocks, pipes, and machine frames. Its ability to produce complex shapes also makes it suitable for artistic and architectural applications.
Key Differences
1. Mold Material Die casting utilizes metal dies, while sand casting uses molds made of sand. 2. Production Volume Die casting is better suited for high-volume production due to its rapid cycle times, whereas sand casting is more cost-effective for lower production volumes. 3. Detail and Finish Die casting typically offers superior accuracy and a finer surface finish compared to sand casting, which may require additional machining for a smooth finish. 4. Cost of Tooling The initial cost of die casting molds is significantly higher than that of sand casting molds. However, die casting molds have a longer lifespan, which can offset the initial investment in high-volume applications.
Conclusion
Both die casting and sand casting are integral to the manufacturing industry, each serving specific roles based on their characteristics and advantages. Die casting is favored for high-volume, high-precision applications, while sand casting is prized for its versatility and cost-effectiveness in producing larger parts. By understanding the differences between these two casting methods, manufacturers can make informed decisions that enhance productivity and product quality, ultimately leading to more effective and sustainable manufacturing processes.
Post time:ное. . 05, 2024 04:19
Next:the golden sands