The Sand Casting Process An Overview
Sand casting is one of the oldest and most widely used metal casting processes in manufacturing. The method involves creating a mold from a mixture of sand and a bonding agent, pouring molten metal into the mold, and allowing it to solidify. This article will provide an overview of the sand casting process, its advantages, and applications.
The Sand Casting Process Steps
1. Pattern Making The first step in sand casting is the creation of a pattern, which serves as a replica of the final product. Patterns are typically made from materials such as wood, metal, or plastic. The pattern's design must include allowances for shrinkage, machining, and draft to facilitate mold removal.
2. Mold Preparation The next step is preparing the sand mold. A mixture of sand, clay, and water is used to form the mold. The sand grains are coated with clay and moisture, which helps them stick together when packed around the pattern. The pattern is placed in a two-part mold, known as a cope and drag, and sand is tightly packed around it to form the mold cavity.
3. Core Making In cases where the casting has internal features or complex geometries, cores made of sand are also created. These cores are inserted into the mold cavity to shape the inside of the casting.
4. Mold Assembly Once the sand is packed around the pattern, the mold halves are removed, and the pattern is taken out, leaving a cavity in the shape of the desired part. The two halves of the mold are then reassembled and secured.
5. Pouring Molten metal is heated to its liquid state and then poured into the mold cavity through a pouring gate. The temperature, composition, and fluidity of the metal are critical to ensure proper flow and fill-out of the mold.
describe sand casting process
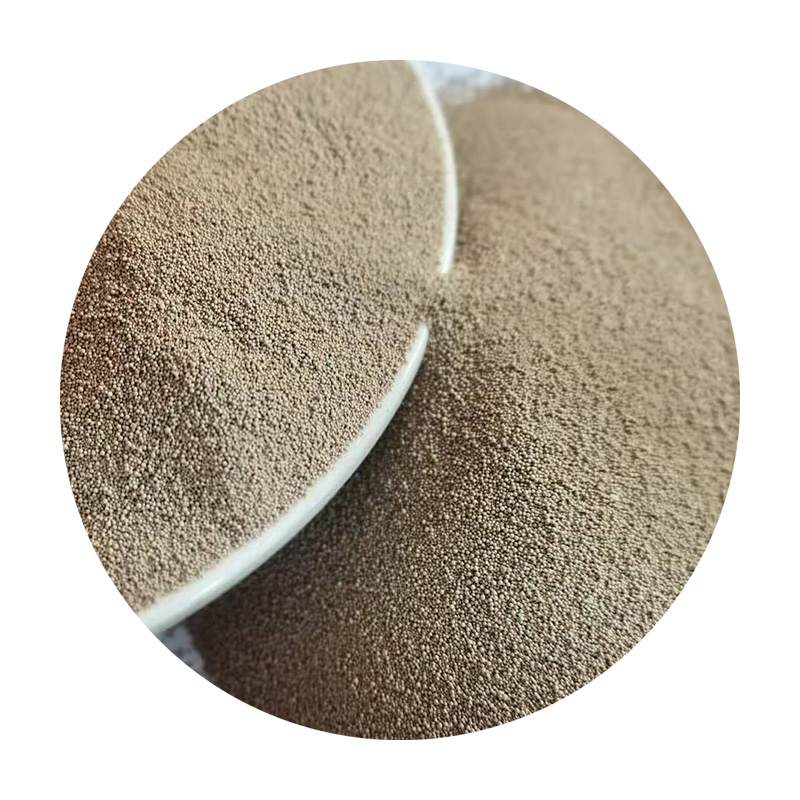
6. Cooling and Solidification After pouring, the molten metal begins to cool and solidify within the mold. The cooling time depends on the size and complexity of the part. Once solidified, the mold is broken apart to extract the casting.
7. Finishing The final step involves cleaning and finishing the casting. Any excess material, called gating and riser, is trimmed away. Additional processes such as machining, surface treatment, and inspection may also be required to ensure the casting meets specific tolerances and surface quality.
Advantages of Sand Casting
Sand casting offers several advantages. It is a versatile process capable of producing a wide range of metal alloys and complex shapes. The materials used are relatively inexpensive and readily available, making it cost-effective for both small and large production runs. Moreover, the flexibility in design allows for easy modification of patterns without significant tooling costs.
Applications
Sand casting is used in various industries, including automotive, aerospace, construction, and art. Common products made through sand casting include engine blocks, housing for pumps, and intricate sculptures.
In conclusion, the sand casting process is a vital manufacturing technique known for its adaptability and economic efficiency. From the initial pattern to the finished casting, this process embodies a blend of tradition and technology, playing a crucial role in modern metalworking and production. Its enduring popularity is a testament to its effectiveness in meeting the diverse demands of various industries.
Post time:ное. . 04, 2024 06:03
Next:golden sands company