Advantages of Sand Casting
Sand casting, also known as sand mold casting, is one of the oldest and most widely used casting processes in the foundry industry. It involves creating a mold from sand and then pouring molten metal into it to produce various components and parts. This method offers several key advantages, making it a popular choice among manufacturers. In this article, we will explore the primary benefits of sand casting.
Cost-Effectiveness
One of the most significant advantages of sand casting is its cost-effectiveness. The materials used in sand casting, primarily sand and a binding agent, are relatively inexpensive and readily available. This makes the initial setup costs lower compared to other casting methods that may require more sophisticated materials or equipment. Furthermore, the simplicity of the process allows for a reduction in labor costs since fewer technicians are needed to operate the machinery and handle the casting process.
Versatility
Sand casting is highly versatile and can accommodate a wide range of metals, including aluminum, bronze, iron, and magnesium. This flexibility allows manufacturers to produce a multitude of parts and components, catering to various industries such as automotive, aerospace, and construction. Additionally, sand casting is capable of creating both small and large parts, which adds to its appeal in different manufacturing scenarios.
Complex Shapes and Designs
One of the standout features of sand casting is its ability to produce complex shapes and intricate designs. The sand mold can be easily modified to create various geometries, which might be difficult or impossible to achieve using other casting methods. This capability is particularly beneficial for industries that require customized or specialized components. Engineers and designers often prefer sand casting for prototypes and one-off parts due to this flexibility.
Good Surface Finish and Accuracy
advantages of sand casting
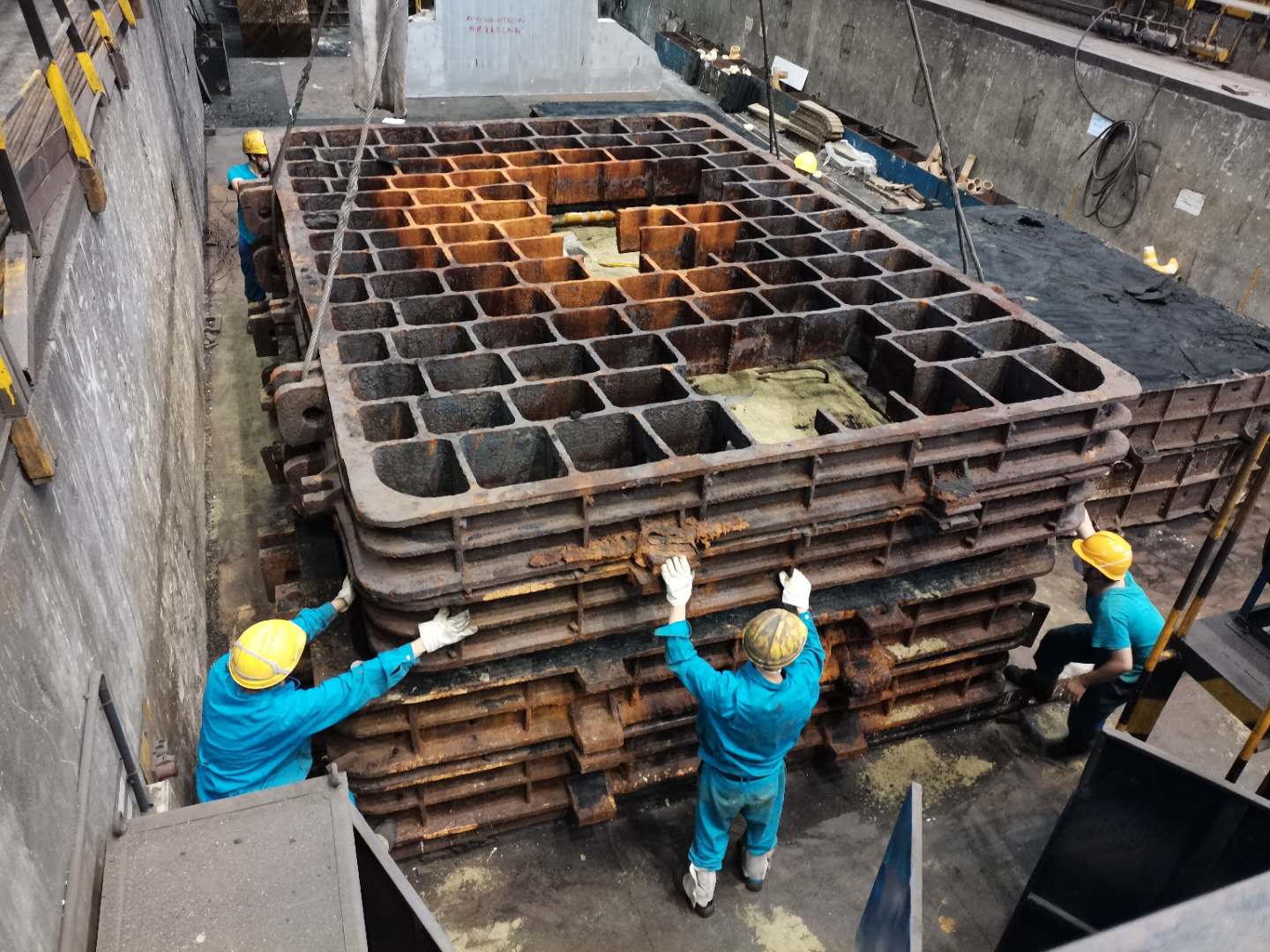
While sand casting is generally associated with a coarser surface finish compared to other casting methods, it can still achieve a relatively good surface quality when properly managed. Advanced techniques, such as the use of resin-bonded sand or ceramic sand, can enhance the surface finish, meeting the requirements for more demanding applications. Moreover, sand casting can deliver good dimensional accuracy, particularly when using modern molding techniques and precision tooling.
Environmental Impact
In recent years, there has been an increasing focus on sustainability in manufacturing processes. Sand casting is considered more environmentally friendly compared to other casting methods, primarily because sand is a natural resource that can be reused multiple times. After the casting process, the used sand can often be reclaimed and recycled, minimizing waste and reducing the need for new materials. Many foundries have implemented processes that allow them to reuse sand efficiently, leading to lower environmental impact.
Scalability
Sand casting processes can be easily scaled to accommodate different production volumes. Whether it is for low-volume production or mass production, sand casting can be adapted to meet these demands. This scalability is particularly important for manufacturers who may need to switch between small batches of custom parts and larger orders of standard components.
Quick Turnaround
With the ability to create molds quickly, sand casting provides a fast turnaround time for the production of parts. This speed is advantageous in industries where time-to-market is crucial. Rapid prototyping is made simpler with sand casting, allowing for quicker iterations and adjustments based on feedback or design changes.
Conclusion
In conclusion, sand casting is a versatile and cost-effective manufacturing process with numerous advantages. Its ability to produce complex shapes, accommodate various materials, and provide good surface finishes makes it an attractive option for many industries. With its environmentally friendly practices and scalability, sand casting remains a cornerstone of modern manufacturing, proving that traditional methods can still meet the challenges of today’s dynamic marketplace. Whether for prototypes or large-scale production runs, the benefits of sand casting make it a valuable technique in the foundry sector.
Post time:окт. . 22, 2024 10:55
Next:high volume sand casting