The Advantages of Sand Casting
Sand casting, also known as sand mold casting, is one of the oldest and most versatile casting processes in manufacturing. It involves creating a mold from a mixture of sand, clay, and water, into which molten metal is poured to form a part. This traditional method has stood the test of time due to its numerous advantages, making it a popular choice in various industries.
One of the primary benefits of sand casting is its cost-effectiveness. The materials required for making the sand molds are relatively inexpensive and readily available. Sand can be reused multiple times, which reduces the overall production costs. Furthermore, the equipment used for sand casting is simpler and less expensive than that used in other casting methods, making it accessible for small-scale operations and startups.
The Advantages of Sand Casting
Additionally, sand casting offers excellent thermal properties. The sand used in molds can withstand high temperatures, which is crucial when dealing with molten metals that can reach temperatures exceeding 1500°C. This capability allows manufacturers to work with various alloys and metals, including iron, aluminum, and bronze, without fear of mold degradation. This versatility makes sand casting a preferred method in various metallurgical applications.
advantage of sand casting
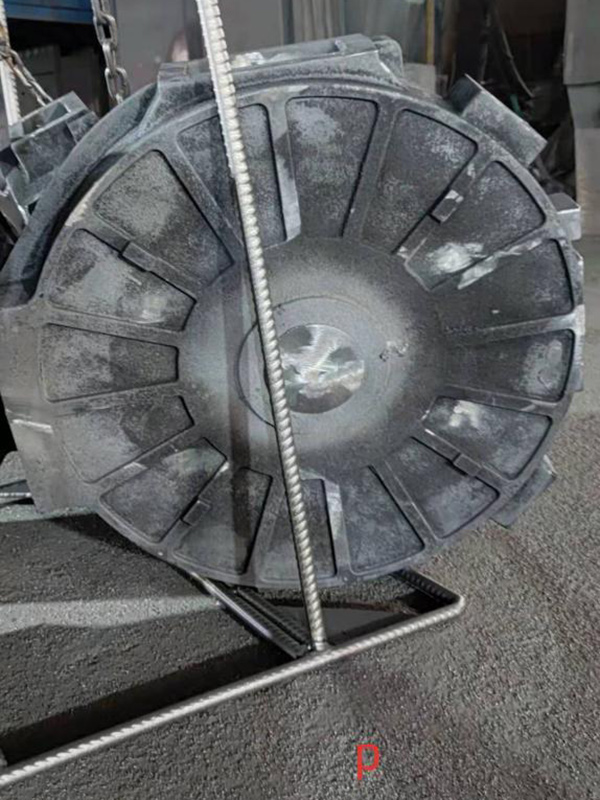
Moreover, sand casting is not limited to a specific type of material. Manufacturers can utilize an extensive range of metals and alloys, allowing for greater creativity and innovation in product design. This adaptability enables the production of parts that meet specific requirements for strength, weight, and corrosion resistance, providing manufacturers the flexibility to tailor products to customer demands.
Another advantage is the relatively quick turnaround time for prototypes and production runs. The sand molding process allows for rapid changes and adjustments, which is particularly advantageous during the design phase. Once a mold has been created, it can be reused for multiple cycles, significantly speeding up the manufacturing process. As a result, businesses can respond more swiftly to market demands and reduce lead times.
Furthermore, the sand casting process is environmentally friendly. The primary material, sand, is abundant and recyclable. Although there are some emissions associated with the production of metal, advancements in technology have improved emissions control and energy efficiency in modern foundries.
In conclusion, sand casting remains a highly beneficial method for producing metal parts due to its cost-effectiveness, versatility, and ability to manufacture complex shapes in various materials. Its adaptability to different sizes and thermal strengths, along with rapid production capabilities and environmental benefits, continues to make it a preferred technique in manufacturing industries. As technology evolves, the process may become even more efficient, ensuring that sand casting remains a viable option for the future of metal fabrication.
Post time:сеп. . 25, 2024 03:23
Next:Exploring Techniques for Effective Ceramic Surface Smoothing and Finishing